What are spherical rubber joints used for?
Firstly, because of the hollow shape of spherical rubber joints, they are suitable for transporting liquids, gases and solids. The second is that under the same weight condition, the spherical rubber joint has a larger cross-sectional modulus compared with other spherical rubber joint methods, i.e. stronger bending and torsional resistance, which is an economic section spherical rubber joint and high efficiency spherical rubber joint. General spherical rubber joints should have high corrosion resistance to a variety of corrosive media, good high-temperature strength and low-temperature resistance, and the processing technology and skill requirements in this regard are getting higher and higher. Secondly, the requirements of the scale and shape accuracy of spherical rubber soft joints also promote online detection and automatic control skills continue to progress.
The demand for lower cost of spherical rubber joints makes its production process develop in the direction of short process and near final molding. The advantage of spherical rubber joint is that it can damage the casting arrangement of the ingot, refine the grain of stainless spherical rubber joint, and eliminate the defects of microscopic arrangement, then make the metallographic arrangement of spherical rubber joint more dense and improve the mechanical function. This improvement is generally reflected in the direction of rolling, and then the stainless steel plate is no longer isotropic to a certain extent, together with the effect of high temperature and pressure welding previously poured bubbles, cracks and loose.
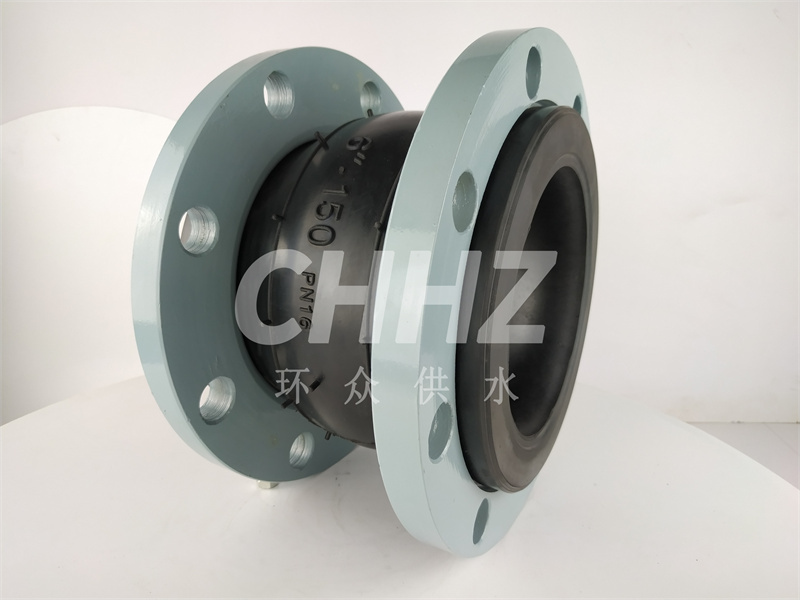
Spherical rubber joints also have defects, after hot rolling, stainless steel plate internal non-metallic inclusions (generally sulfides and oxides, and silicates) will be pressed into thin sheets, showing the phenomenon of delamination. Delamination will make the ball type rubber flexible joint along the thickness direction of the tensile function is greatly deteriorated, and there is a possibility of interlayer tearing when the weld is shortened. The partial strain induced by weld shortening often reaches several times the yield point strain, which is much stronger than the load-induced strain.