What are the methods of the components of the flexible waterproof casing type B.
What are the methods of the components of the flexible waterproof casing type B. The flexible waterproof casing (type B) is an essential component in various industries, including the automotive, electronics, and telecommunications sectors. This casing is designed to provide protection against water, dust, and different environmental conditions. To ensure its effectiveness, several methods are employed during the manufacturing process. In this article, we will discuss the key methods used for each component of the flexible waterproof casing type B.
Outer Covering: The outer covering is the first line of defense for the casing. It is typically made from durable and waterproof materials such as silicone or thermoplastic elastomers (TPE). A molding method called injection molding is commonly used to produce these outer coverings. In this method, the material is melted and injected into a mold cavity, taking the desired shape. After solidification, the outer covering is removed from the mold and undergoes further processing, such as trimming or surface texturing.
Sealing Mechanism: The sealing mechanism is crucial for preventing water ingress into the casing. There are various methods employed for effective sealing, including compression seals and gaskets. Compression seals involve using the compressibility of materials like silicone foam or rubber to create a tight seal between the casing components. Gaskets, on the other hand, are made from materials such as neoprene or rubber and are placed between mating surfaces to create a watertight seal. These gaskets can be custom-made based on the specific design requirements of the casing.
Connector Protection: Connectors are vulnerable points in a waterproof casing, as they provide access for cables or other components. To protect connectors, methods like overmolding or potting are utilized. Overmolding involves the encapsulation of connectors with a layer of waterproof material using injection molding techniques. This provides both mechanical protection and water resistance. Potting, on the other hand, involves filling the area around the connectors with a liquid or a gel-like material such as epoxy or silicone. This method ensures a complete seal and prevents water or dust ingress.
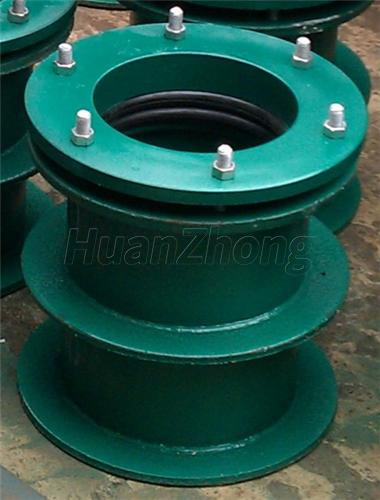
Ventilation: Ventilation is essential to allow the equalization of pressure within the casing while maintaining its waterproof properties. One common method is the use of breathable membranes or vents. These membranes are made from materials that allow air molecules to pass through while blocking water droplets. Membranes are often placed in strategic locations to facilitate pressure equalization without compromising the waterproof integrity of the casing.
Testing and Quality Control: Throughout the manufacturing process, it is crucial to conduct rigorous testing and quality control to ensure the reliability and effectiveness of the flexible waterproof casing. Testing methods may include water immersion, pressure testing, or environmental simulation tests. Additionally, inspection and quality control processes are implemented to identify any defects or inconsistencies in the casing components.
In conclusion, the flexible waterproof casing type B relies on various methods for its components. The outer covering is produced through injection molding, while the sealing mechanism incorporates compression seals or gaskets. Connectors are protected using overmolding or potting methods, and ventilation is facilitated by breathable membranes. Lastly, rigorous testing and quality control ensure the reliability of the casing. These methods combine to create a robust and effective waterproof casing suitable for a wide range of applications.