Welded Sleeve Compensator Corrosion Protection.
Welded Sleeve Compensator Corrosion Protection. Corrosion protection is a critical aspect of ensuring the longevity and reliability of welded sleeve compensators. These compensators play a vital role in absorbing movements and accommodating thermal expansion in piping systems. However, without proper corrosion protection measures, they can be susceptible to damage, compromising their performance and durability. In this essay, we will explore the importance of corrosion protection for welded sleeve compensators and discuss various strategies to prevent corrosion.
Corrosion Damage: Corrosion is a natural electrochemical process that occurs when metals come into contact with corrosive substances, such as water, chemicals, or gases. When a welded sleeve compensator is exposed to these corrosive elements, it can lead to the deterioration of the metal components. Corrosion damage can weaken the structure of the compensators and reduce their ability to absorb movements and accommodate thermal expansion.
Protective Coatings: Applying protective coatings is one of the most common methods to prevent corrosion on welded sleeve compensators. These coatings act as a barrier between the metal surface and the corrosive environment, preventing direct contact and minimizing the risk of corrosion. Coatings such as epoxy, polyurethane, or fusion-bonded epoxy (FBE) can provide excellent protection against corrosion, increasing the lifespan of the compensators.
Cathodic Protection: Cathodic protection is another effective corrosion prevention technique for welded sleeve compensators. It involves the use of sacrificial anodes or impressed current to neutralize the electrochemical reaction responsible for corrosion. Sacrificial anodes, typically made of zinc or magnesium, are connected to the compensator's metal surface. The anodes corrode instead of the compensator, prolonging its lifespan. Impressed current systems use an external electric current to protect the compensator from corrosion, thereby enhancing its durability.
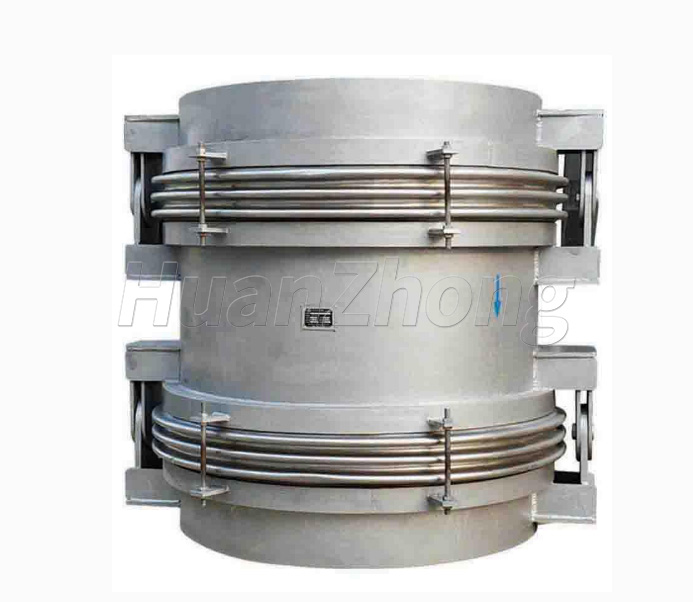
Material Selection: Choosing the right materials for welded sleeve compensators is crucial in preventing corrosion. Stainless steel or alloy materials are commonly used due to their inherent resistance to corrosion. These materials have a higher resistance to the corrosive effects of water, chemicals, and gases. Additionally, considering the specific environment and the corrosive substances the compensators will be exposed to is vital in selecting the appropriate material with the required corrosion resistance.
Regular Maintenance and Inspection: Regular maintenance and inspection are essential for identifying and addressing any signs of corrosion in welded sleeve compensators at an early stage. Routine cleaning, monitoring, and assessment of the compensators can help detect corrosion or any potential issues. Prompt repairs or recoating can be performed to mitigate the damage and prevent further deterioration.
In conclusion, corrosion protection is crucial for ensuring the performance and durability of welded sleeve compensators. By implementing protective coatings, cathodic protection, and selecting corrosion-resistant materials, the compensators can withstand corrosive environments and maintain their functionality. Regular maintenance and inspection further help identify and address any corrosion-related issues proactively. Incorporating corrosion protection measures in the design, installation, and maintenance of welded sleeve compensators is essential for extending their lifespan, reducing downtime, and optimizing the reliability of piping systems.