Oil Resistant Rubber Joints Product Advantages and Structural Features.
Oil Resistant Rubber Joints Product Advantages and Structural Features. Oil-resistant rubber joints are specifically designed to withstand exposure to oils, fuels, and other petroleum-based substances. In this article, we will discuss the product advantages and structural features of oil-resistant rubber joints, highlighting why they are commonly used in various industries.
One of the key advantages of oil-resistant rubber joints is their exceptional resistance to oil and fuel. The rubber material used in these joints is formulated with special additives that enhance its resistance to petroleum-based substances, ensuring that it remains unaffected even when in prolonged contact with oils, fuels, and other hydrocarbons. This resistance is crucial in industries where the piping systems are exposed to these substances, such as in oil refineries, chemical plants, and automotive manufacturing facilities. By using oil-resistant rubber joints, operators can prevent degradation, swelling, and premature failure of the joints, ensuring the integrity of the entire piping system.
Another advantage of oil-resistant rubber joints is their excellent flexibility and ability to accommodate movement. These joints are designed to compensate for thermal expansion, contraction, and other types of movement that may occur in the piping system. This flexibility helps to absorb vibrations, shocks, and forces, reducing stress on the system and preventing damage. The ability of oil-resistant rubber joints to accommodate movement is particularly beneficial in applications where there are temperature fluctuations or where the equipment generates vibrations, such as in engines, pumps, and compressors.
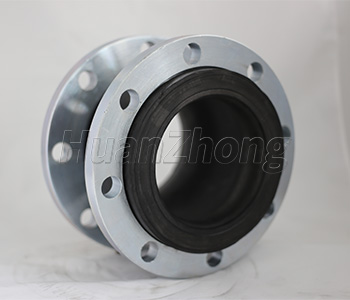
Structurally, oil-resistant rubber joints have a multi-layer construction that enhances their performance. The inner layer of the joint is typically made of a high-grade rubber material that is specially engineered to resist oil and fuel. This layer acts as a barrier, preventing the penetration of these substances into the joint and protecting the underlying layers. The outer layer is often reinforced with fabric or metal, providing added strength and durability. This multi-layer construction ensures that the joint can withstand the harsh conditions found in oil-based environments, including exposure to chemicals, high temperatures, and mechanical stresses.
Additionally, oil-resistant rubber joints are often designed with flanged or threaded ends, making them easy to install and connect to adjacent pipes or equipment. This simplifies the installation process, reducing the need for specialized tools or complex procedures. Furthermore, if maintenance or repairs are required, oil-resistant rubber joints can be easily removed and replaced, minimizing downtime and operational disruptions.
In conclusion, oil-resistant rubber joints offer several advantages in applications where exposure to oils and fuels is a concern. Their exceptional resistance to oil and fuel, along with their flexibility, ability to accommodate movement, and multi-layer construction, make them ideal for various industries. By incorporating oil-resistant rubber joints into the piping system, operators can ensure the durability, reliability, and integrity of the system, even in demanding oil-based environments.