Rubber Joints-Specific Machinery
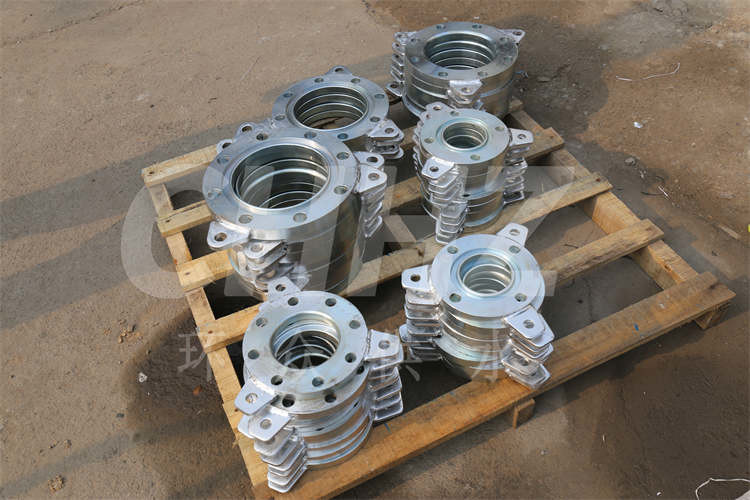
When it comes to the production and assembly of rubber joints, a range of specialized machinery is utilized to ensure efficient and precise manufacturing processes. These machines are designed to handle various aspects of rubber joint production, including material preparation, shaping, bonding, and quality control. In this article, we will explore several key types of machinery commonly used in the manufacturing of rubber joints and their crucial roles in the production process.
Rubber Mixing Mills: Rubber mixing mills are essential for preparing rubber compounds used in the production of rubber joints. These mills consist of two counter-rotating rolls that efficiently blend and homogenize rubber compounds with other additives and fillers. The resulting rubber sheets or strips serve as a fundamental input for subsequent processes, laying the foundation for the quality and performance of the final rubber joints.
Hydraulic Presses: Hydraulic presses are widely employed in the production of rubber joints to shape and mold rubber compounds into the desired configurations. These presses provide the necessary force and precision for shaping rubber sheets or strips into bellows, flanges, or other intricate components required for assembling rubber joints. The versatility of hydraulic presses enables the creation of a wide variety of rubber joint designs, meeting diverse industrial requirements.
Vulcanizing Autoclaves: Vulcanizing autoclaves play a critical role in the rubber joint manufacturing process by facilitating the curing and bonding of rubber components under controlled temperature and pressure conditions. These autoclaves provide an ideal environment for the cross-linking of rubber polymers, ensuring the proper strength, durability, and resilience of the final rubber joints. Vulcanizing autoclaves contribute significantly to the quality and performance of the finished products.
Molding Machines: Molding machines are utilized for the production of rubber joint components with intricate shapes and precise dimensions. These machines use molds and high-pressure methods to form rubber components such as expansion joints, couplings, and connectors. Injection molding and compression molding processes are commonly employed to create uniform and high-quality rubber joint components, meeting the demanding specifications of various industrial applications.
Quality Testing Equipment: Quality testing equipment, including devices for hardness, tensile strength, and dimensional analysis, is indispensable in ensuring the reliability and functionality of rubber joints. These testing machines assess the properties and performance characteristics of rubber joint components, verifying compliance with stringent quality standards and specifications. By conducting thorough quality testing, manufacturers can guarantee the superior performance and longevity of their rubber joint products.
In conclusion, the specialized machinery used in the manufacturing of rubber joints plays a crucial role in every stage of the production process, from material preparation and shaping to curing and quality assurance. By leveraging advanced machinery tailored to the specific requirements of rubber joint production, manufacturers can achieve precise, efficient, and consistent manufacturing processes, ultimately delivering high-quality and reliable rubber joint products to meet diverse industrial needs.
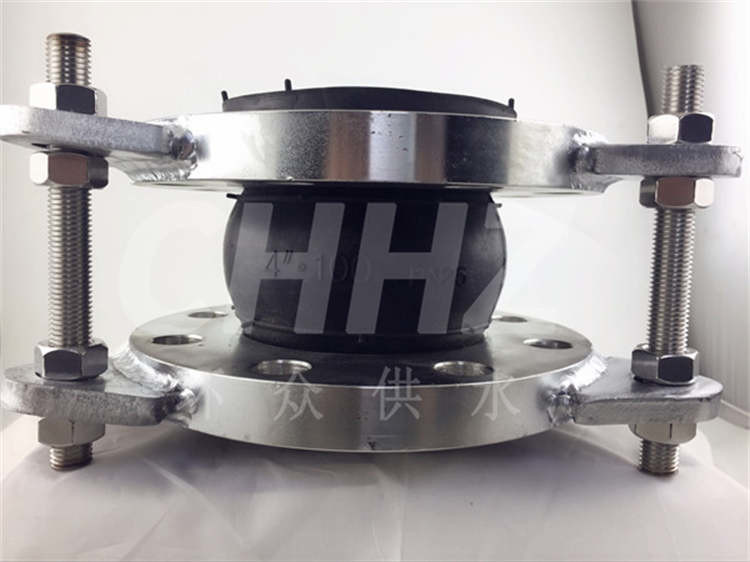