Expansion Joints for Building Mechanical and Electrical Systems
Expansion joints, also known as flexible connectors, play a crucial role in building mechanical and electrical systems. These joints are designed to accommodate movement, vibration, and misalignment in piping systems, thereby reducing stress and extending the life of pipelines and associated equipment. This article provides an overview of the application and manufacturing of expansion joints in building mechanical and electrical systems.
In building mechanical and electrical systems, expansion joints are used to connect various components, such as pumps, chillers, air handling units, and other mechanical equipment, to the piping system. They allow for thermal expansion, contraction, and vibration, which occur as a result of temperature variations and operational dynamics. By absorbing these movements, expansion joints help to prevent damage to the piping system and the connected equipment.
The manufacturing process for expansion joints involves several key steps. It begins with the selection of high-quality rubber compounds, such as natural rubber, EPDM, neoprene, or nitrile rubber, depending on the specific requirements of the application. These compounds offer durability, flexibility, and resistance to various environmental conditions and chemicals.
Once the rubber compound is selected, it undergoes a mixing process to achieve the desired properties and uniformity. Additives such as curing agents, accelerators, and reinforcing materials are blended with the rubber to enhance its strength, elasticity, and resilience. This mixing process is critical to ensuring that the resulting expansion joints meet the performance requirements of building mechanical and electrical systems.
After the mixing phase, the rubber compound is shaped and molded into the desired form using specialized techniques such as compression molding or injection molding. The specific method used depends on the complexity of the expansion joint design and the manufacturing requirements. The joints are then subjected to curing or vulcanization, a process that imparts the necessary mechanical properties to the rubber, including resilience, elasticity, and resistance to deformation over a wide range of temperatures.
Finally, the manufactured expansion joints undergo rigorous inspection and quality control measures to ensure that they meet the required specifications and standards. Testing for physical properties, dimensional accuracy, and leak resistance is conducted to verify the performance of the expansion joints.
In conclusion, expansion joints are essential components in building mechanical and electrical systems, providing flexibility and resilience to piping systems. The manufacturing process involves selecting high-quality rubber compounds, mixing and shaping the rubber, curing the material, and conducting stringent quality control checks. By facilitating movement and accommodating thermal expansion, expansion joints contribute to the efficient and reliable operation of building mechanical and electrical systems.
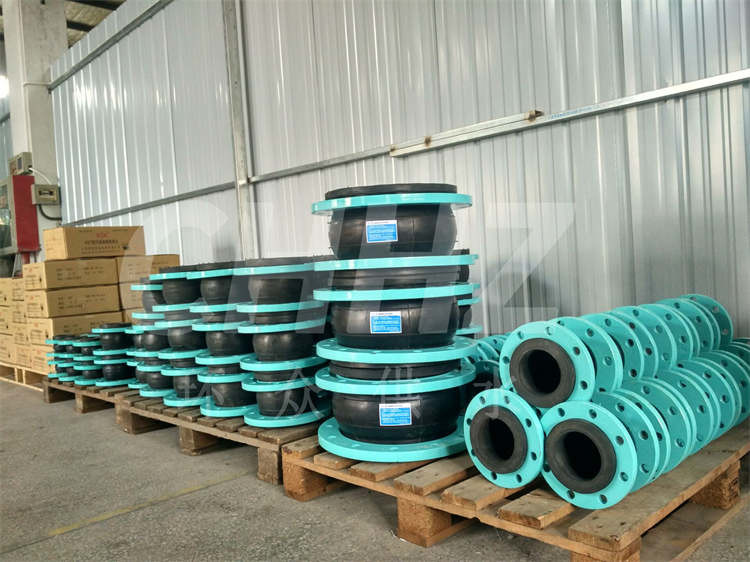