Processing Methods for Rubber Expansion Joints

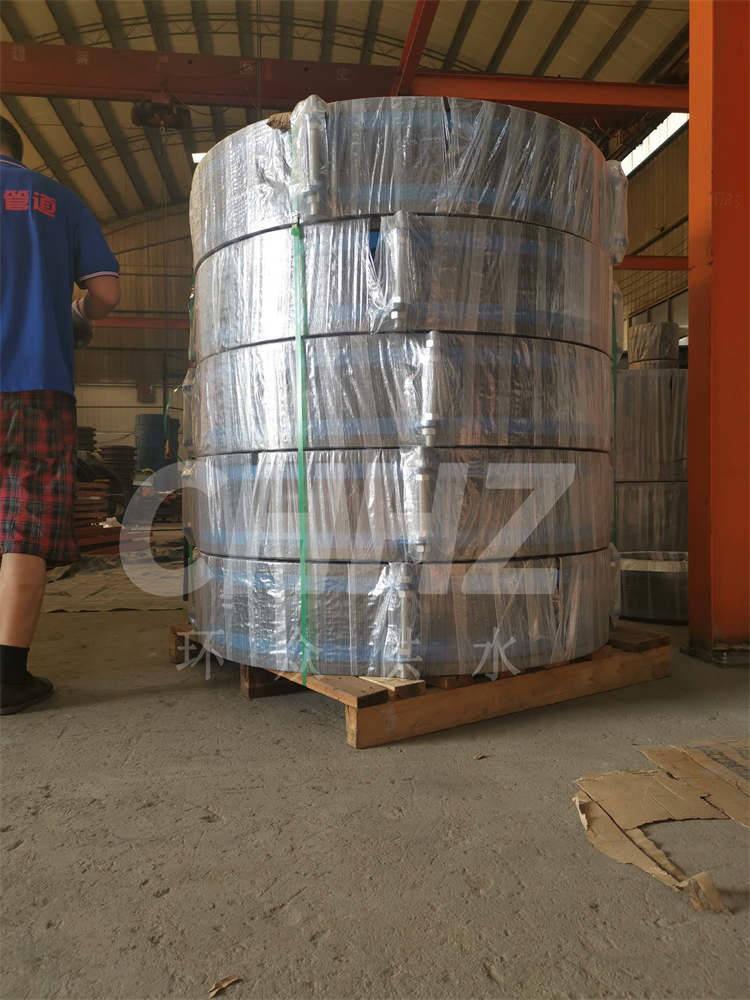
Rubber expansion joints are crucial components in piping systems, providing flexibility and vibration isolation to accommodate movement and thermal expansion. This article explores the various methods utilized in the processing of rubber expansion joints from raw blanks to finished products in industrial applications.
The processing of rubber expansion joints begins with the fabrication of raw blanks, typically composed of premium-grade synthetic rubber compounds with reinforcing elements such as fabric or metal inserts. The first step involves the cutting of the rubber material into precise shapes and sizes using die-cutting or water jet cutting equipment to form the basic components of the expansion joint.
Next, the raw rubber blanks undergo the process of molding or shaping, where the rubber material is placed into a mold cavity and subjected to heat and pressure to achieve the desired shape and structural integrity. This step is crucial in ensuring that the expansion joint conforms to specific dimensional requirements and exhibits consistent material properties.
Following molding, the raw rubber blanks are prepared for the insertion of reinforcing elements, such as internal nylon or metal rings, to enhance the structural strength and pressure resistance of the expansion joint. This may involve the use of adhesive bonding or mechanical fastening methods to securely integrate the reinforcing elements within the rubber structure.
Once the reinforcement is in place, the next stage involves the vulcanization or curing process, wherein the rubber material is exposed to elevated temperatures and pressure to induce cross-linking of the polymer chains, resulting in improved elasticity, durability, and resistance to environmental factors such as heat, chemicals, and weathering.
Subsequently, the finished expansion joint undergoes precision trimming and finishing to achieve the desired dimensional tolerances and surface smoothness. Advanced cutting and grinding techniques are employed to remove excess rubber material and ensure uniformity in shape and appearance.
Quality control assessments are an integral part of the processing methods for rubber expansion joints, involving rigorous testing and inspections to verify dimensional accuracy, material strength, and leak-tightness. This includes pressure testing, visual inspections, and material property evaluations to ensure that the final product meets the required standards and specifications.
In conclusion, the processing of rubber expansion joints involves a series of meticulous steps, from the fabrication of raw blanks to the final finishing and quality control processes. By employing advanced manufacturing techniques and stringent quality assurance measures, manufacturers can produce high-quality rubber expansion joints that offer reliable performance, durability, and longevity in various industrial piping systems.
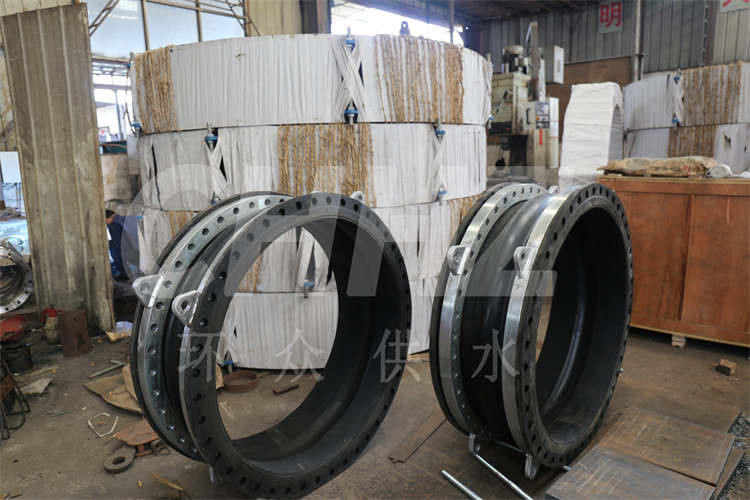