Rubber Hose Joint Molds: Enhancing Production Efficiency and Quality
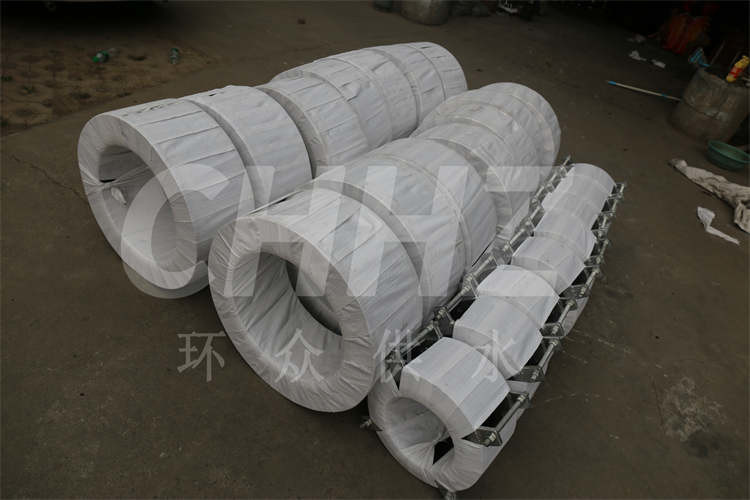
Rubber hose joints are integral components in various fluid conveyance systems, serving to connect hoses and facilitate the seamless transfer of liquids or gases. The production of these essential components often involves the utilization of molds to shape and form the rubber into the desired joint configurations. This article delves into the key aspects of rubber hose joint molds, highlighting their significance in enhancing production efficiency and ensuring high-quality end products.
Design Considerations: The design of rubber hose joint molds is a critical factor that influences the manufacturability, functionality, and durability of the resulting components. Molds must be meticulously designed to impart the precise geometrical features, sealing surfaces, and reinforcement structures required for optimal performance. Moreover, considerations such as mold material selection, cooling channels, and venting systems play pivotal roles in achieving uniform mold filling, reducing cycle times, and minimizing defects in the molded products.
Material Selection: Selecting the appropriate mold material is vital to withstand the demands of the rubber molding process, ensuring dimensional accuracy and surface finish of the molded hose joints. High-quality mold materials, such as tool steel or aluminum alloys, offer superior thermal conductivity, wear resistance, and machinability, contributing to consistent and reliable production outcomes. Furthermore, advanced surface treatments and coatings can enhance mold release properties, minimize adhesion of the rubber compound, and prolong the service life of the molds.
Precision Machining and Tooling: The precision machining of rubber hose joint molds is paramount for achieving tight tolerances, intricate details, and smooth surface finishes. Utilizing advanced tooling technologies, such as computer numerical control (CNC) machining and electrical discharge machining (EDM), enables the creation of highly complex mold cavities and cores with exceptional accuracy. Additionally, the incorporation of interchangeable mold inserts and flexible mold configurations facilitates rapid tooling changes and versatility in accommodating varying joint specifications and sizes.
Molding Process Optimization: Efficient and cost-effective production of rubber hose joints hinges on the optimization of the molding process parameters, including temperature, pressure, cure time, and demolding strategies. Well-engineered molds, coupled with precise control over the molding conditions, can minimize material waste, reduce cycle times, and uphold consistent part quality. Furthermore, the incorporation of innovative mold filling techniques, such as injection-compression molding or vacuum-assisted molding, can enhance the replication of intricate details and reinforce the structural integrity of the hose joints.
In conclusion, the design, material selection, precision machining, and process optimization of rubber hose joint molds are pivotal in elevating the efficiency and quality of production processes in rubber molding facilities. By leveraging advanced mold technologies and adhering to best practices, manufacturers can ensure the seamless and reliable production of high-performance rubber hose joints while maintaining a competitive edge in the market.
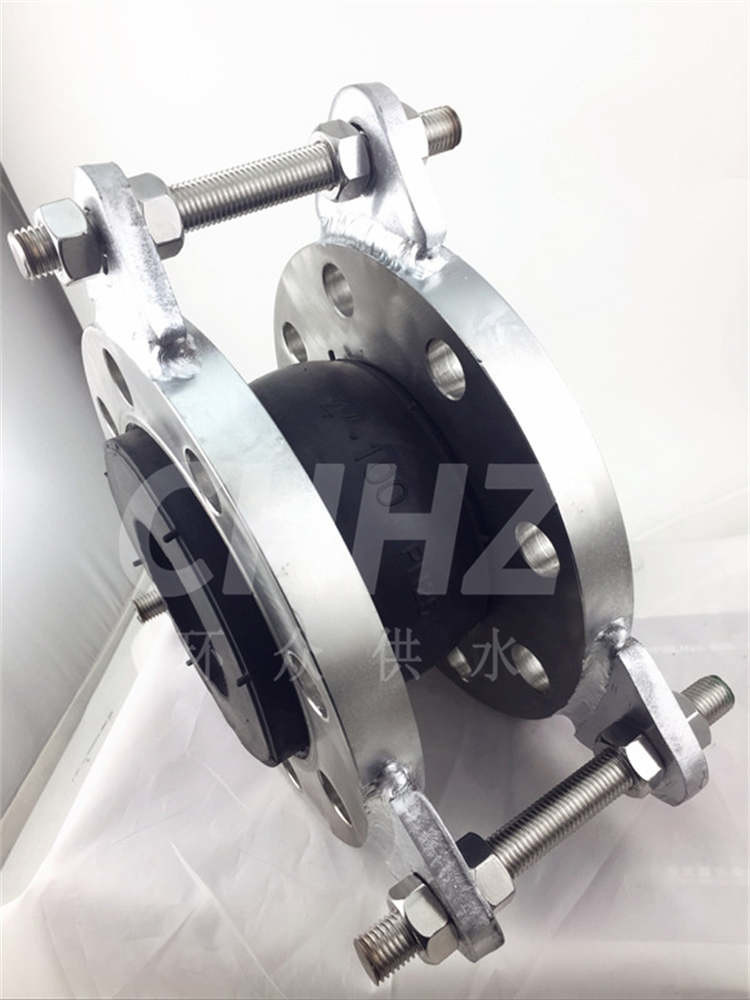