Customizing Rubber Expansion Joints to Meet Your Needs
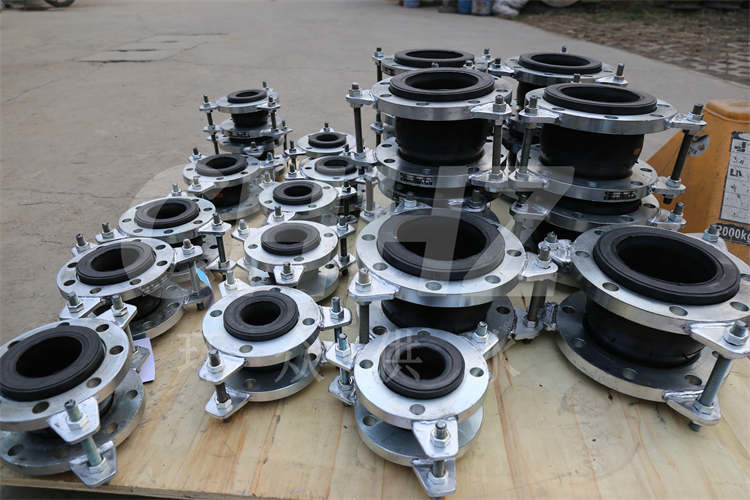
Rubber expansion joints play a critical role in various industrial applications, providing flexibility, vibration isolation, and movement absorption in piping systems. In today's dynamic industrial landscape, the ability to customize rubber expansion joints to specific requirements is imperative. This article explores the significance of tailored rubber expansion joints and the process of custom manufacturing to meet individual needs.
Why Customization Matters Off-the-shelf expansion joints may not always address the unique demands of every application. Variances in pipe diameters, pressure ratings, temperature ranges, chemical compatibility, and spatial constraints necessitate customized solutions. By tailoring the design, materials, and configurations of rubber expansion joints, manufacturers can ensure optimal performance and longevity in diverse operating environments.
Design and Engineering Expertise Customization begins with a comprehensive understanding of the application's operating conditions, including fluid media, pressure fluctuations, axial and angular movements, and thermal cycling. Experienced engineers leverage this information to design expansion joints that precisely accommodate the system's requirements. Factors such as shape design, reinforcement layers, lining materials, and end connection types are meticulously evaluated and optimized to deliver a bespoke solution.
Material Selection and Compatibility One of the key advantages of customization lies in the ability to select materials that align with the specific needs of the application. Whether it's EPDM, Nitrile, Neoprene, Viton, or other elastomers, the choice of rubber compounds is tailored to ensure chemical resistance, temperature tolerance, and longevity. Furthermore, custom fabric reinforcements and corrosion-resistant hardware are integrated to enhance the expansion joint's durability and reliability.
Precision Manufacturing and Testing The custom manufacturing process involves precision fabrication, meticulous assembly, and comprehensive quality testing. Advanced manufacturing techniques such as molding, vulcanization, and thermal bonding are employed to craft expansion joints that precisely conform to the specified dimensions and performance characteristics. In-process and post-production testing, including hydrostatic tests, vacuum tests, and dimensional inspections, validate the integrity and functionality of the customized expansion joints.
End-to-End Support and Collaboration A key aspect of customizing rubber expansion joints is the collaborative partnership between manufacturers and end-users. Effective communication, detailed project requirements, and technical consultations enable manufacturers to tailor expansion joints that align with the specific needs of the application. From initial design concepts to post-installation support, a customer-centric approach ensures that the customized expansion joints seamlessly integrate into the piping system.
Conclusion As industrial processes become increasingly demanding and diverse, the role of customized rubber expansion joints is pivotal in providing tailored solutions for complex applications. By leveraging design expertise, material selection, precision manufacturing, and collaborative partnerships, customized expansion joints empower industries to achieve operational efficiency, reliability, and safety tailored to their unique requirements.
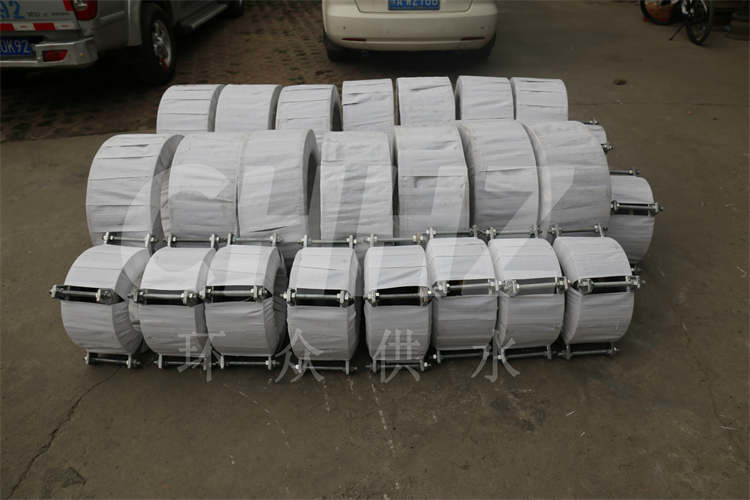