Mold Design for Rubber Flexible Joints
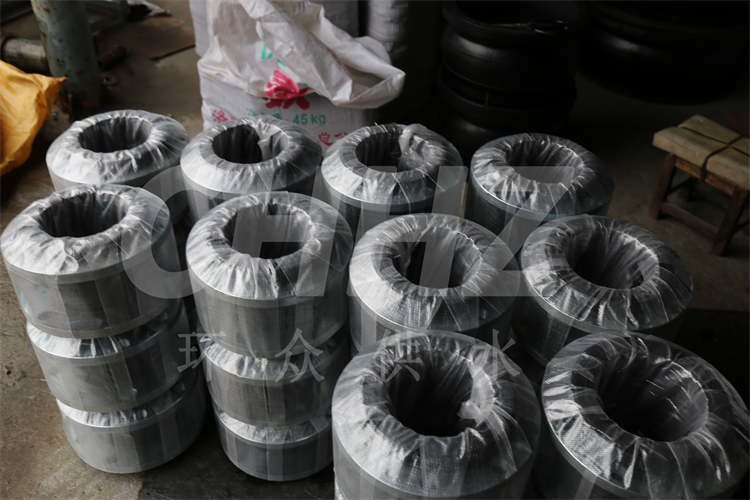
Mold design plays a critical role in the production of rubber flexible joints, as it directly influences the quality, performance, and efficiency of the manufacturing process. Rubber flexible joints, also known as expansion joints, are crucial components used in various industries to absorb movement, reduce vibration, and compensate for misalignment in piping and ducting systems. This article will discuss the significance of mold design for rubber flexible joints, key considerations in the design process, and the impact of advanced mold technology on the quality and production of these vital components.
Significance of Mold Design for Rubber Flexible Joints:
The design of molds for rubber flexible joints is pivotal in ensuring that the finished components meet the stringent requirements of different applications. The mold design directly influences the dimensional accuracy, surface finish, and durability of the rubber joints. It is essential for achieving the desired flexibility, strength, and resistance to environmental factors such as temperature, pressure, and chemical exposure. A well-designed mold is critical for producing rubber flexible joints that effectively accommodate movement and vibration while maintaining sealing integrity in piping and ducting systems across industries such as HVAC, industrial processing, and transportation.
Key Considerations in Mold Design:
The design of molds for rubber flexible joints involves several key considerations to optimize the performance, manufacturability, and consistency of the components. Firstly, the mold design must accommodate the specific geometry and size requirements of the flexible joints, ensuring that the molds can accurately replicate the desired shape and dimensions. Additionally, considerations for material flow, venting, and parting lines are critical to avoid defects such as air bubbles, voids, or flash during the molding process. The selection of mold materials and surface treatments also influences the release properties and durability of the molds, impacting the overall production efficiency and tool longevity.
Furthermore, the incorporation of advanced features such as mold inserts, multi-cavity designs, and precision cooling systems can enhance the productivity and repeatability of the molding process, allowing for the efficient mass production of rubber flexible joints with consistent quality and performance characteristics. Mold designers must also account for factors like gate locations, ejection methods, and de-molding requirements to streamline the manufacturing process and minimize cycle times, contributing to cost-effective production.
Impact of Advanced Mold Technology:
The use of advanced mold technology, including computer-aided design (CAD), computer-aided manufacturing (CAM), and simulation software, has significantly impacted the design and production of molds for rubber flexible joints. CAD/CAM software enables the precise modeling and visualization of complex mold geometries, facilitating the development of intricate flexible joint designs that meet diverse application requirements. Additionally, mold flow analysis and simulation tools allow designers to optimize the mold design for material flow, air evacuation, and cooling, ensuring the uniformity and integrity of the molded parts.
Moreover, the integration of innovative mold manufacturing techniques such as additive manufacturing (3D printing), high-precision CNC machining, and advanced surface coatings has enhanced the precision, customization, and tooling lifespan of molds for rubber flexible joints. By leveraging these technologies, manufacturers can achieve greater design flexibility, rapid prototyping capabilities, and enhanced mold durability, ultimately contributing to the production of high-quality rubber flexible joints with reduced lead times and enhanced performance attributes.
In conclusion, mold design for rubber flexible joints is a critical aspect of the manufacturing process, essential for producing components that meet the stringent requirements of diverse industrial applications. By addressing key considerations in mold design and leveraging advanced mold technology, manufacturers can achieve the efficient production of rubber flexible joints with precise dimensions, consistent quality, and optimal performance characteristics. The continuous advancement of mold design and manufacturing techniques underscores the pivotal role of mold technology in meeting the evolving demands of industries relying on rubber flexible joints for piping and ducting systems.
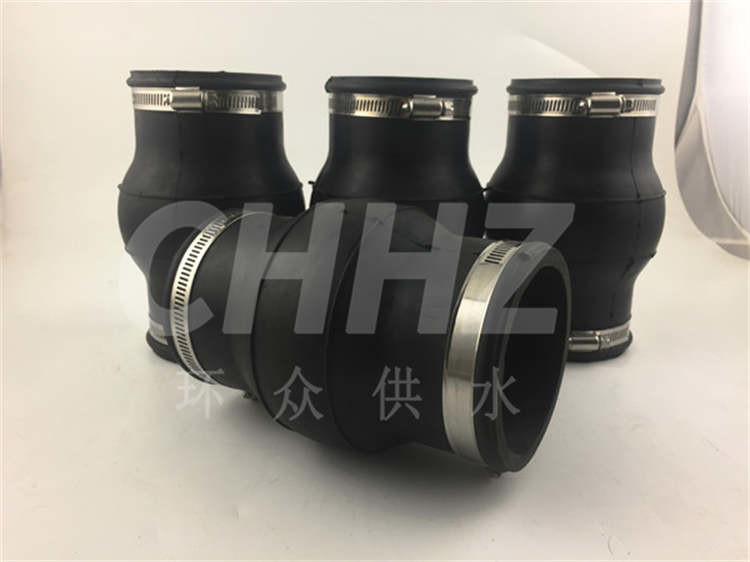