Making a rubber expansion joint mold
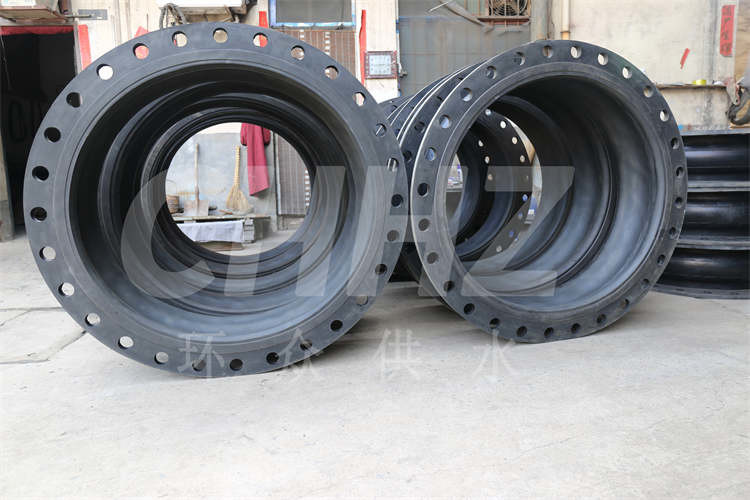
Making a rubber expansion joint mold involves a series of intricate steps to create a precise and durable mold that can be used in the production of rubber expansion joints. The creation of the mold is crucial in ensuring the quality, accuracy, and consistency of the final rubber expansion joints. Here's an overview of the process involved in making a rubber expansion joint mold.
Design and Prototyping: The mold-making process initiates with the design and prototyping phase. Skilled engineers and designers create detailed blueprints and 3D models of the expansion joint mold based on the specifications provided. These designs are meticulously crafted to ensure proper fit and functionality.
Material Selection: Once the design is finalized, the next step involves selecting the appropriate materials for constructing the mold. High-quality, durable materials such as silicone, rubber, or metal are often used, depending on the specific requirements of the expansion joint and the production environment.
Mold Fabrication: The chosen materials are then used to craft the mold. Depending on the complexity of the design, different mold-making techniques such as injection molding or CNC machining may be employed to shape the mold accurately. Skilled artisans ensure that every detail and contour of the mold matches the specifications.
Finishing and Polishing: After the basic mold structure is created, it undergoes a finishing process. The mold's surfaces are meticulously polished to achieve a smooth and flawless finish. This step is critical, as it ensures that the final rubber expansion joints will have a smooth and uniform surface.
Testing and Validation: Once the mold is constructed, it undergoes rigorous testing and validation to ensure its precision and functionality. The mold is tested by creating sample rubber expansion joints to verify that it can produce parts that meet the required specifications and standards. Any necessary adjustments are made based on the test results.
Quality Assurance: Throughout the mold-making process, stringent quality control measures are implemented to maintain the highest standards. Each stage of mold production is closely monitored to identify and rectify any potential defects or discrepancies.
Final Verification: Once the mold is validated and confirmed to meet the requisite standards, it is given a final inspection to ensure that it is ready for use in the production of rubber expansion joints.
In conclusion, the process of making a rubber expansion joint mold involves a comprehensive approach that combines precision design, quality materials, skilled craftsmanship, and thorough testing. This meticulous process ensures that the resulting mold is capable of producing high-quality rubber expansion joints that meet the required specifications and standards.
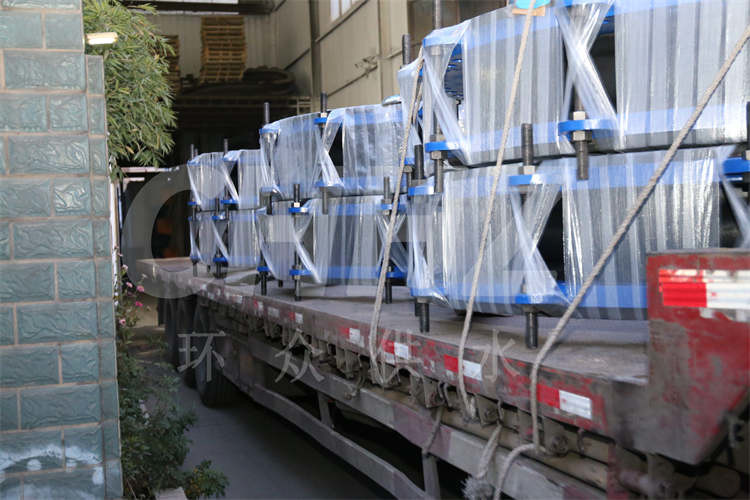