Casting Rubber Flexible Joint Moulds
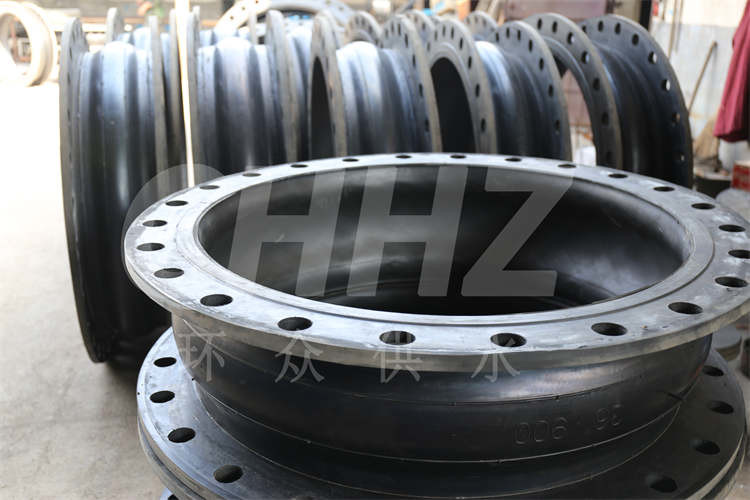
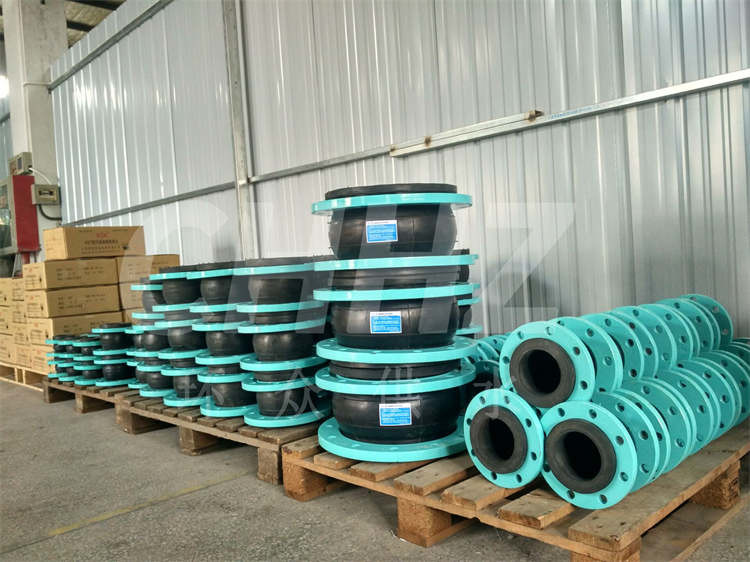
The casting of molds for rubber flexible joints is a crucial process that enables the production of high-quality components used in various piping and industrial applications. This article aims to provide insights into the mold casting process for rubber flexible joints, emphasizing the key steps involved in creating durable and precise molds to meet industry standards and specific application requirements.
Design and Pattern Preparation: The mold casting process begins with the creation of a detailed design and pattern for the rubber flexible joint. This involves meticulous engineering and design work to ensure that the final mold will accurately capture the dimensions, contours, and features of the intended product. Patterns serve as the basis for creating the mold cavity and are crafted with precision to account for shrinkage and other factors affecting the final product's dimensions.
Material Selection: The choice of mold material is critical to the overall quality and performance of the rubber flexible joint. Depending on the application, molds are typically made from materials such as metal alloys, such as aluminum or steel, or high-quality polymer composites. The selection of the material is based on factors such as durability, thermal conductivity, mold life, and the number of casts required.
Mold Making: The pattern is used to create the mold cavity through various mold-making techniques such as sand casting, investment casting, or die casting, depending on the complexity, size, and production volume of the rubber flexible joint. Skilled craftsmen and advanced machinery are employed to ensure that the mold cavity accurately reproduces the intricate details of the pattern.
Core Making: In cases where the rubber flexible joint requires internal features, cores are produced using sand or metal to create the desired internal geometry. Precision core-making processes are employed to ensure that the cores fit seamlessly within the mold cavity, enabling the casting of complex and hollow components.
Casting and Solidification: Once the mold cavity and cores are prepared, the casting process begins. The chosen material is melted and poured into the mold cavity, allowing it to solidify and take the shape of the rubber flexible joint. Attention is given to factors such as cooling rate, feeding systems, and heat flow to optimize the casting process and minimize defects.
Finishing and Quality Assurance: After solidification, the cast rubber flexible joint is removed from the mold, and any excess material or imperfections are carefully removed. The final product undergoes rigorous quality checks to ensure dimensional accuracy, surface finish, and material integrity, meeting industry standards and customer specifications.
In conclusion, the process of casting molds for rubber flexible joints requires careful planning, precise execution, and adherence to quality standards to produce components that meet the demands of diverse industrial and piping applications. By focusing on design accuracy, material selection, and meticulous craftsmanship, manufacturers can ensure the production of reliable and durable rubber flexible joints that contribute to the efficiency and safety of various systems.
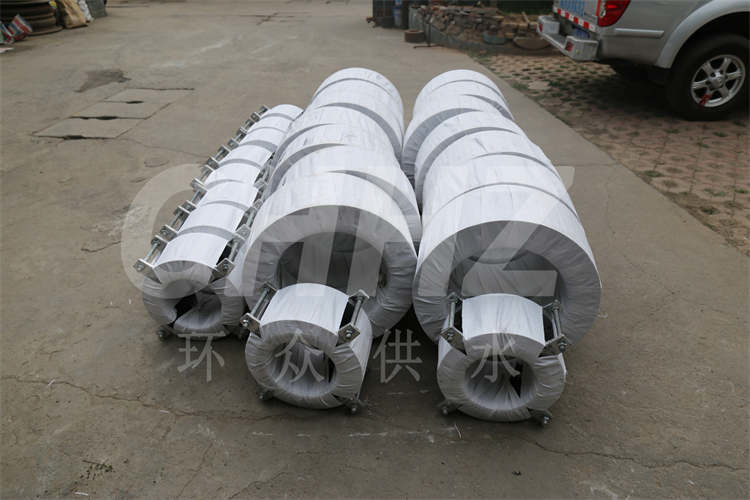