Customized Rubber Flexible Joint Processing Tutorial
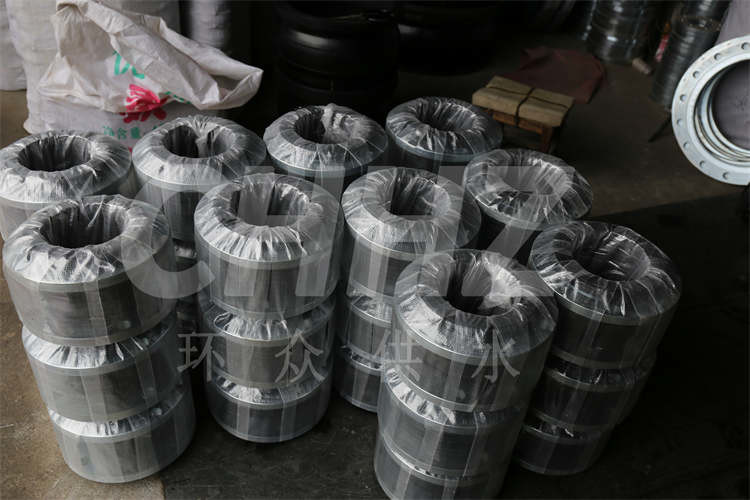
Rubber flexible joints are crucial components in various engineering and industrial applications due to their ability to absorb and isolate vibration, reduce noise, and compensate for thermal expansion. Customizing these rubber flexible joints involves a detailed and precise manufacturing process to ensure optimal performance. This article presents a comprehensive guide to the processing of customized rubber flexible joints.
Material Selection: The first step in the processing of customized rubber flexible joints is the careful selection of raw materials. High-quality synthetic rubber, such as EPDM, NBR, or neoprene, is commonly used for its excellent resilience, flexibility, and chemical resistance. The selection of the right material depends on the specific application and environmental conditions the joint will be exposed to.
Mold Design and Fabrication: Once the material is selected, the next step is the design and fabrication of the mold. The mold is a critical aspect of the manufacturing process and determines the final shape and dimensions of the rubber flexible joint. Computer-aided design (CAD) software and precision machining are often employed to ensure accuracy and consistency in the mold fabrication process.
Rubber Mixing and Compounding: After the mold is ready, the rubber material is mixed with various additives and compounds to achieve the desired physical and chemical properties. This includes the precise measurement and mixing of rubber, curing agents, accelerators, and fillers to achieve the required hardness, elasticity, and resistance to environmental factors.
Vulcanization and Molding: The mixed rubber compound is then shaped and vulcanized using heat and pressure in the mold. Vulcanization is a crucial process that transforms the rubber compound into a durable and stable material by creating strong cross-links between the polymer chains. The pressure and temperature conditions are carefully controlled to ensure uniform curing throughout the entire joint.
Quality Control and Testing: Once the rubber flexible joint is molded, it undergoes rigorous quality control and testing to verify its performance and durability. This may include dimensional measurements, hardness testing, and inspection for any defects or imperfections. Additionally, the joint may undergo functional tests to ensure its ability to withstand the intended operating conditions.
Customization and Assembly: Finally, the customized rubber flexible joint is assembled according to the specific requirements of the application. This may involve adding flanges, threads, or other connection features to enable seamless integration into the system it is intended for.
In conclusion, the processing of customized rubber flexible joints requires meticulous attention to detail, from material selection to final assembly, to ensure the highest quality and performance. By following a systematic and precise manufacturing process, customized rubber flexible joints can be tailored to meet the exact needs of various industrial and engineering applications.
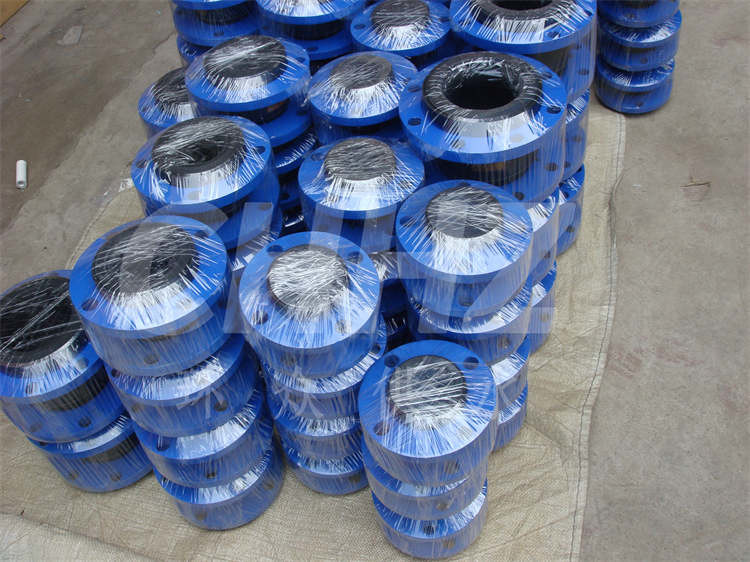