Specifications of Rubber Joints for Valve Fittings
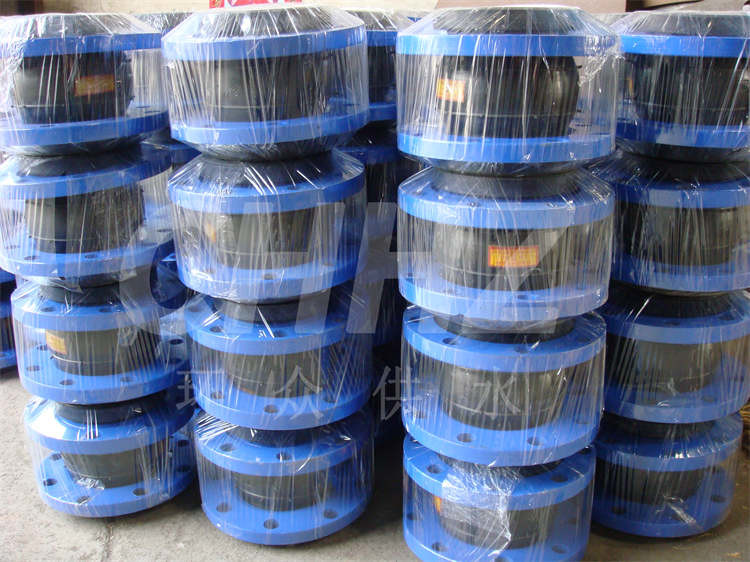
Rubber joints, also known as rubber expansion joints, play a crucial role in ensuring the smooth and efficient operation of valve fittings in various industrial applications. These flexible connectors are designed to absorb and isolate vibrations, compensate for misalignments, and provide an effective seal in piping systems. When selecting the appropriate rubber joint for valve fittings, several key specifications must be taken into consideration to meet the specific requirements of the application. In this article, we will explore the essential specifications used to define rubber joints for valve fittings.
Size and Dimensional Parameters: The size of rubber joints is a critical specification that must align with the dimensions of the valve fittings and the piping system. The inner diameter, outer diameter, and overall length of the rubber joint should be selected to match the nominal pipe size and accommodate any axial movements or deflections within the system. Additionally, considerations for flange dimensions and drilling patterns are essential to ensure proper fitting and alignment with the valve and piping components.
Material Composition and Performance Characteristics: The material composition of rubber joints significantly impacts their performance and durability in valve fittings. Common elastomeric materials used in rubber joints include natural rubber, EPDM, neoprene, nitrile rubber, and other synthetic elastomers. The material selection should be based on the operating temperature, chemical compatibility, and resistance to abrasion, corrosion, and other environmental factors. Furthermore, performance characteristics such as tensile strength, elongation, hardness, and resilience are crucial specifications that determine the suitability of the rubber joint for specific valve applications.
Pressure Rating and Temperature Limits: Rubber joints are subjected to internal pressure, external forces, and temperature variations within piping systems. It is essential to specify the maximum allowable pressure rating and the operating temperature range for the rubber joint to ensure safe and reliable performance. The pressure rating should consider both the system pressure and any surge or water hammer effects, while the temperature limits should accommodate the fluid media and ambient conditions.
Movement and Deflection Capacities: Valve fittings and piping systems often undergo thermal expansion, vibration, and movement due to dynamic loads and operational conditions. The rubber joint specification should define the axial, lateral, and angular movement capabilities to accommodate these dynamic factors and prevent stress on the valve and piping components. The design specifications should also consider the maximum allowable deflection and offset to maintain system integrity.
End Connections and Flange Standards: The method of connecting the rubber joint to the valve and piping system is defined by end connections such as flanges, threaded connections, or grooved ends. The specifications should account for the type of flange standard, such as ANSI, DIN, or JIS, as well as the material and facing requirements to ensure proper sealing and compatibility with the surrounding components.
In conclusion, selecting the right rubber joint for valve fittings involves a thorough consideration of size, material composition, performance characteristics, pressure and temperature limits, movement capacities, and end connections. Understanding and specifying these critical parameters are essential in ensuring the functionality, reliability, and longevity of rubber joints in valve applications. By adhering to these specifications, engineers and designers can effectively integrate rubber joints into valve fittings to optimize system performance and maintain operational integrity.
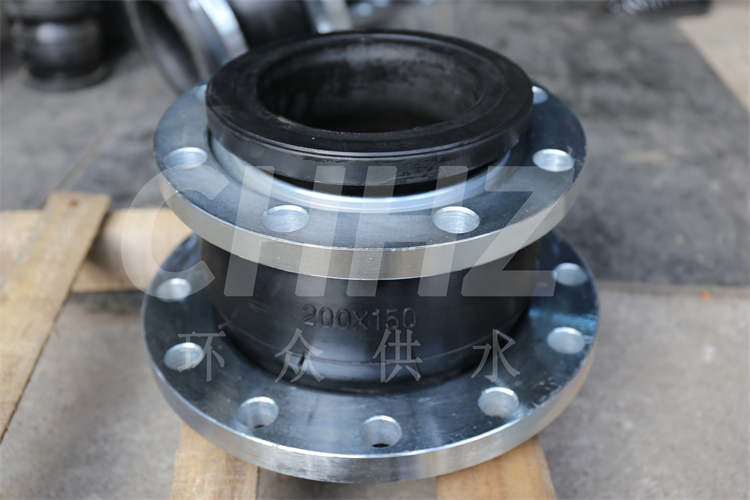