Specifications for Rubber Joints in Power Plant Installations
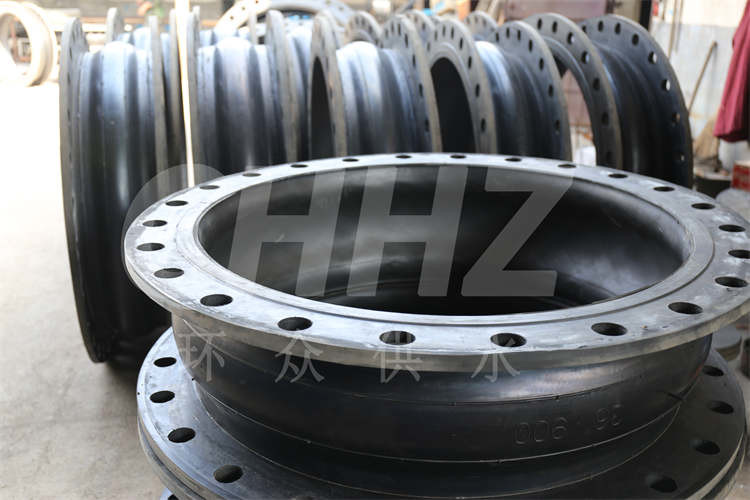
Rubber joints play a critical role in power plant installations, where they are utilized to absorb vibrations, compensate for thermal expansion, and mitigate misalignments in piping systems. Adherence to specific standards and specifications is essential to ensure the effective performance and longevity of rubber joints in these demanding environments.
Material Selection: The selection of rubber materials for joints in power plant installations should adhere to industry standards and guidelines. High-grade synthetic rubber compounds with reinforcement materials, such as polyester or nylon, are commonly employed. These materials must exhibit excellent resistance to chemicals, high temperatures, and pressure differentials to withstand the harsh operating conditions typical of power plants.
Design and Engineering: The design of rubber joints for power plant applications must accommodate the unique demands of the environment. Considerations for multidirectional movement, pressure ratings, temperature ranges, and corrosion resistance are crucial elements of the design process. The joints should be engineered to effectively absorb movements and shocks and protect the interconnected piping and equipment from damage.
Installation Practices: The installation of rubber joints in power plant piping systems requires meticulous attention to ensure optimal performance. Adequate anchoring, proper alignment, and effective sealing are critical aspects of the installation process. Engineers must carefully select the appropriate size and type of joint based on the specific requirements of the power plant, taking into account parameters such as flow rates, operating pressure, and the nature of the conveyed media.
Compliance and Certification: Adherence to relevant industry standards and regulatory requirements is paramount in power plant installations. Rubber joints must conform to recognized standards such as ASTM International, ASME, or other applicable regional standards. Certification by accredited bodies ensures that the rubber joints meet the necessary quality and performance benchmarks required for use in power plant applications.
Maintenance and Inspection: Regular maintenance and inspection protocols are essential to uphold the performance and integrity of rubber joints in power plant installations. Visual inspections for wear, tear, and degradation, as well as assessments of anchoring and sealing integrity, are critical for identifying potential issues. Timely replacement or repair of worn-out joints is necessary to prevent system failures and maintain safety and efficiency.
In conclusion, the specifications for rubber joints in power plant installations encompass material selection, design and engineering considerations, installation practices, compliance with standards, and maintenance protocols. Adhering to these specifications is crucial for ensuring the reliability and longevity of rubber joints, thereby contributing to the safety and efficiency of power plant piping systems.
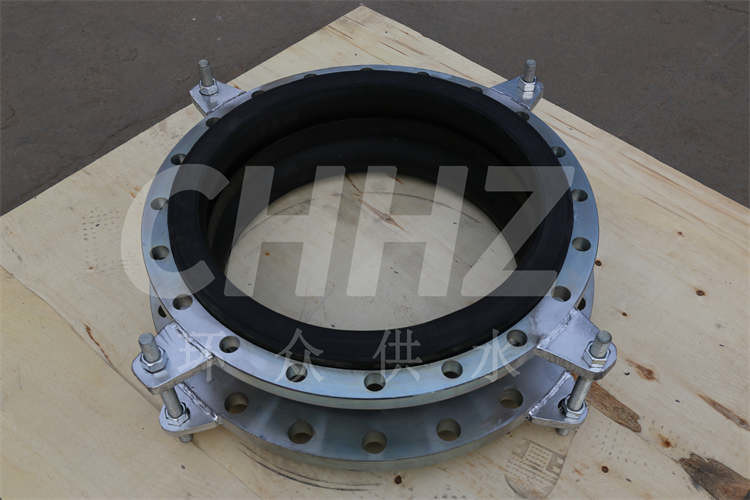