Rubber Molds for Electrical Wire Connectors
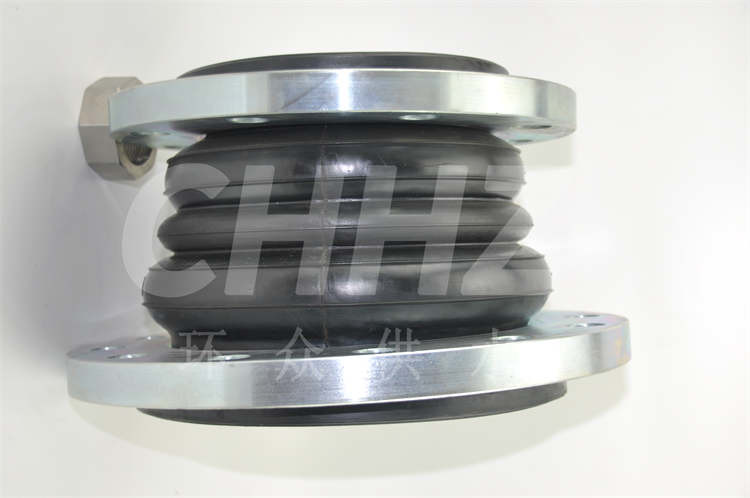
Rubber molds play a crucial role in the production of electrical wire connectors. These molds are used to shape, form, and create the insulating rubber components that are integral to the connector's functionality and safety. Below is a detailed overview of the process and significance of rubber molds in the manufacturing of electrical wire connectors.
Design and Fabrication: The creation of rubber molds for electrical wire connectors involves precision engineering and design. CAD software is often employed to design the mold, ensuring that it accurately reflects the necessary dimensions and specifications for the rubber components.
Material Selection: High-quality, durable materials are selected for constructing the rubber molds, as they must withstand the pressures and temperatures involved in the molding process. Silicone rubber or other specialized mold-making materials are commonly used due to their resilience and ability to capture intricate details.
Molding Process: The rubber molding process for electrical wire connectors typically involves compression or injection molding techniques. In compression molding, the rubber material is placed in the mold cavity, and then pressure and heat are applied to facilitate curing and solidification. Injection molding, on the other hand, involves injecting molten rubber into the mold under high pressure to achieve the desired shape.
Precision and Consistency: The rubber molds must be designed to ensure consistency across multiple production cycles. This includes features such as precise cavities and parting lines to guarantee that the molded rubber components maintain uniformity and quality, meeting industry standards and regulatory requirements.
Insulating Properties: The rubber components produced from these molds serve a critical function in electrical wire connectors by providing insulation and protection. The molds are engineered to create rubber parts that exhibit high dielectric strength and resistance to heat, moisture, and other environmental factors, ensuring the safety and reliability of the connectors.
Durability and Longevity: Rubber molds for electrical wire connectors must be durable and capable of enduring numerous molding cycles without compromising the quality of the produced components. Proper mold maintenance and periodic inspections are essential to extend the lifespan of the molds and uphold manufacturing efficiency.
Quality Control: Rigorous quality control measures are implemented throughout the mold-making and molding process to validate the accuracy and performance of the rubber components. This includes dimensional inspections, material testing, and visual assessments to identify any defects or deviations from specifications.
In conclusion, the use of rubber molds in the production of electrical wire connectors is indispensable, ensuring the manufacture of high-quality, reliable, and safe components for various electrical applications. These molds serve as the foundation for creating insulating rubber parts that are essential for the proper functioning and longevity of electrical wire connectors in diverse industrial and commercial settings.
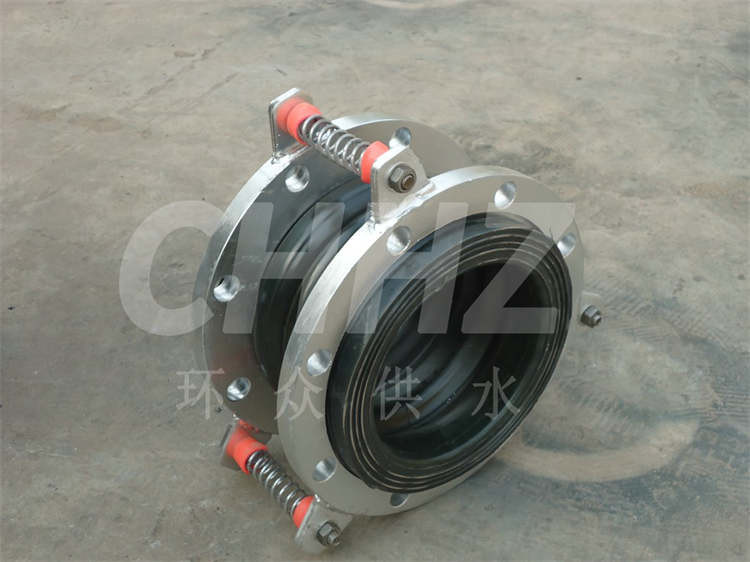