explaining the engineering applications of rubber flexible joints:
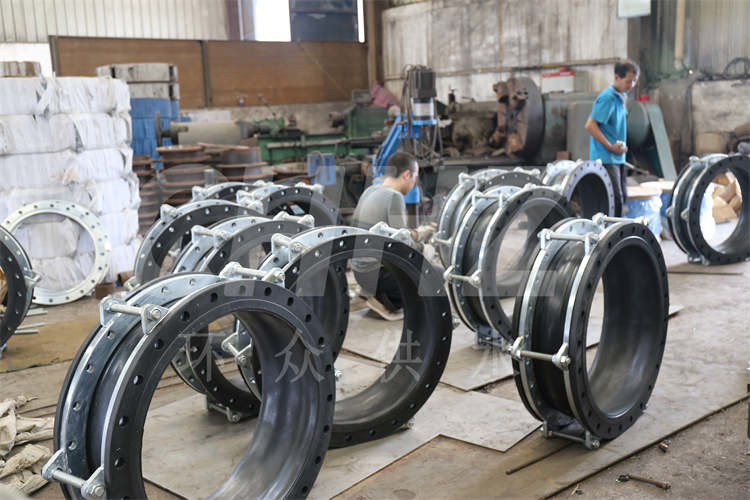
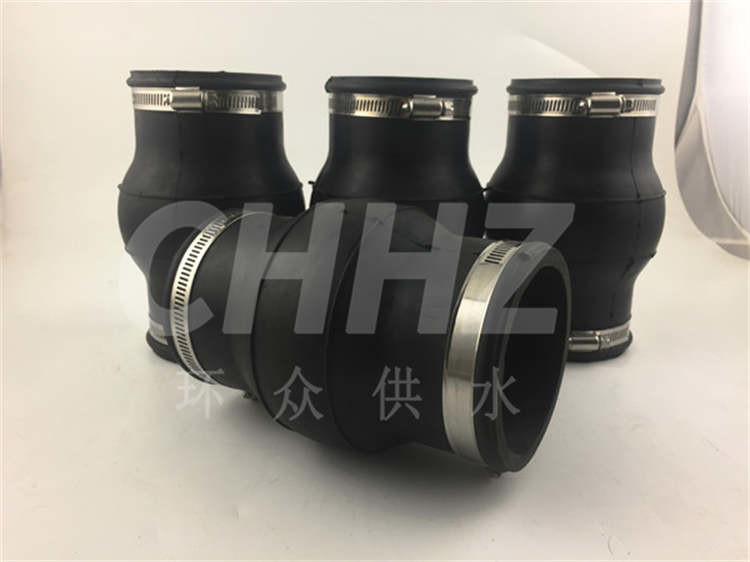
Rubber flexible joints find extensive use in a wide range of engineering applications where the absorption of vibration, thermal expansion, and misalignment compensation are essential. These components are designed to provide flexibility and movement in piping systems, machinery, and mechanical equipment, ensuring smooth operation and prolonged service life. The engineering applications where rubber flexible joints are commonly used include:
Piping Systems: In industrial facilities, rubber flexible joints are employed in piping systems that transport various fluids such as water, chemicals, or gases. These joints accommodate movement and vibration caused by factors such as thermal expansion, equipment operation, or external forces, thereby reducing stress on the piping system and its components. They help to minimize the risk of pipe damage and extend the lifespan of the overall infrastructure.
HVAC Systems: Heating, ventilation, and air conditioning (HVAC) systems require rubber flexible joints to mitigate the effects of vibration, thermal expansion, and contraction. These joints help to absorb the movement and oscillation associated with HVAC equipment, including air handlers, chillers, and ductwork. By incorporating rubber flexible joints, HVAC systems can operate more smoothly and efficiently, reducing the risk of structural damage and enhancing overall
Power Generation: Power plants and energy generation facilities utilize rubber flexible joints in a range of applications, including exhaust systems, steam piping, and cooling water circuits. These joints play a critical role in absorbing movement and vibration, especially in large-scale machinery such as turbines, generators, and pumps. By incorporating rubber flexible joints, power generation systems can effectively manage dynamic stresses and maintain operational reliability.
Industrial Machinery: In manufacturing and industrial environments, rubber flexible joints are utilized in various types of machinery and equipment. These joints provide flexibility to accommodate movements and vibrations in conveyors, crushers, mixers, and other industrial machinery. By integrating rubber flexible joints, the risk of structural fatigue and mechanical failures is minimized, contributing to increased equipment longevity and operational efficiency.
Shipbuilding and Marine Applications: Rubber flexible joints are essential components in marine engineering, where they are used in shipboard piping systems, offshore platforms, and marine equipment. These joints provide critical flexibility to withstand the dynamic forces and vibrations encountered during marine operations, including wave motion, engine vibration, and hull movement. By utilizing rubber flexible joints, marine systems can maintain integrity and reliability under challenging maritime conditions.
In summary, rubber flexible joints find extensive application in a diverse range of engineering fields, including piping systems, HVAC, power generation, industrial machinery, and marine engineering. These components play a crucial role in absorbing movement, vibration, and misalignment, contributing to the smooth operation, longevity, and reliability of various engineering systems and equipment. Their versatile functionality makes them indispensable in ensuring the efficient and resilient performance of critical engineering infrastructure across multiple industries.
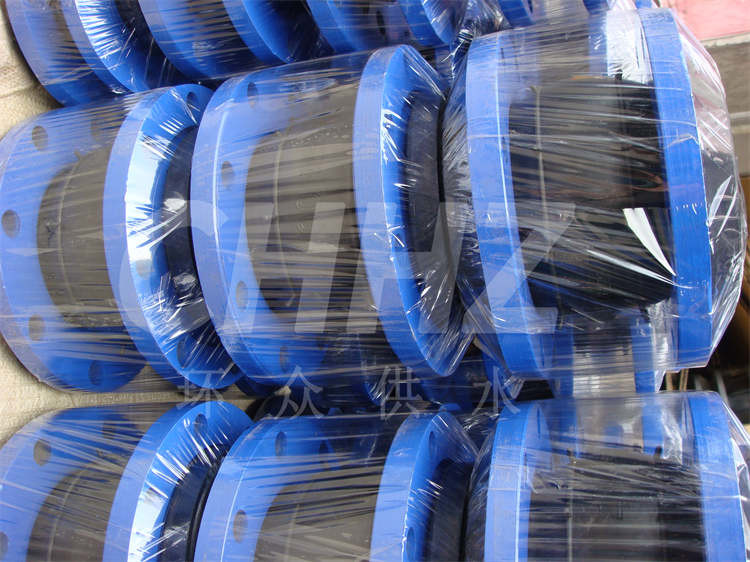