The Rubber Joints in Petroleum Pipeline
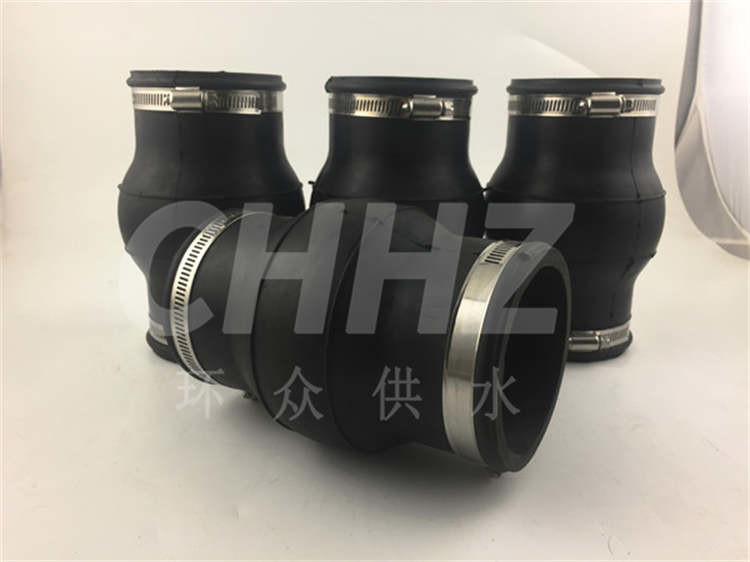
In petroleum pipelines, rubber joints play a crucial role in compensating for movement, misalignment, and vibration, offering flexibility and stability to the pipeline system. This article aims to delve into the significance of rubber joints in petroleum pipelines and their essential functions.
Petroleum pipelines are essential for the transportation of crude oil, refined products, and other hydrocarbons over long distances. These pipelines are subject to various mechanical forces, including thermal expansion, ground movement, and operational vibrations. To accommodate these forces, rubber joints are utilized at strategic points along the pipeline to provide flexibility and absorb movement-induced stress.
Rubber joints, also known as expansion joints or flexible connectors, are designed to absorb axial, lateral, and angular movements in pipelines, thereby minimizing the stress and potential damage to pipeline components. Their flexibility allows for thermal expansion and contraction without inducing excessive strain on the pipeline system. Moreover, they help in dampening vibrations that could otherwise compromise the integrity of the pipeline.
The construction of rubber joints typically involves the use of high-quality elastomeric materials such as natural rubber, neoprene, or EPDM (ethylene propylene diene monomer). These materials offer excellent resilience, resistance to chemical attack, and durability, making them well-suited for the demanding conditions encountered in petroleum pipelines.
Rubber joints are also effective in isolating vibration and reducing noise transmission within pipeline systems. By absorbing and dissipating energy from operational and environmental vibrations, rubber joints help to minimize the transmission of vibration-induced noise through the pipeline, contributing to a quieter and more stable operation.
In addition to their role in accommodating movement and vibration, rubber joints also serve to compensate for misalignment between pipeline sections and equipment. They can accommodate minor deviations in alignment, reducing the stress on pipeline components and ensuring a more uniform distribution of forces within the system.
The installation and maintenance of rubber joints in petroleum pipelines are critical for ensuring their continued effectiveness. Proper installation techniques, along with periodic inspections and maintenance, are essential to the long-term performance of rubber joints in pipeline applications. Regular maintenance helps to detect any wear, deterioration, or damage to the rubber joints, allowing for timely replacement or repairs as necessary.
In conclusion, rubber joints play a vital role in ensuring the integrity and reliability of petroleum pipeline systems. By providing flexibility, stability, and vibration isolation, these essential components contribute to the safe and efficient transportation of hydrocarbons through pipelines. With ongoing advancements in material science and engineering, the design and performance of rubber joints are expected to continue evolving, further enhancing their effectiveness in petroleum pipeline applications.
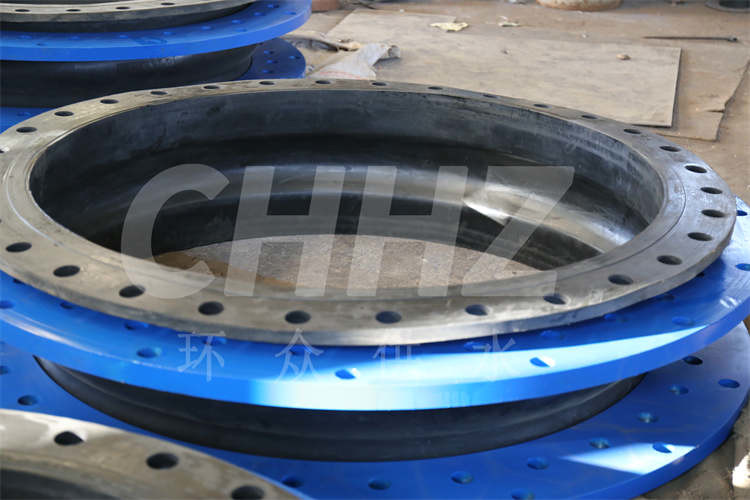