Usage of Rubber Joint Molds for Automotive Glass - A 500-word Article
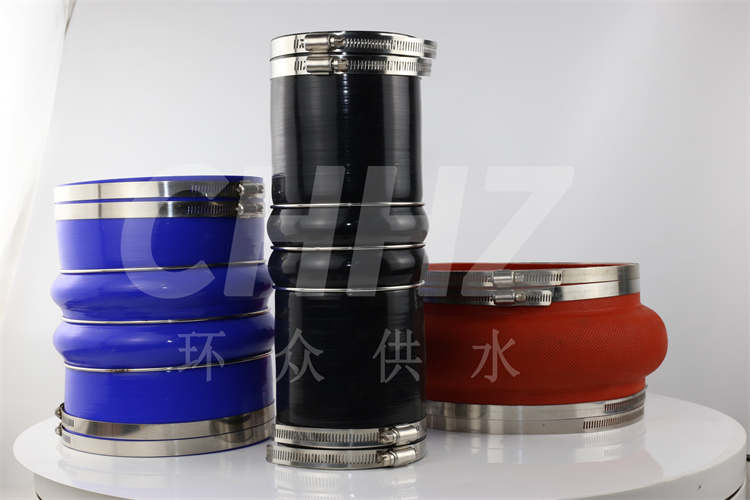
Rubber joint molds are essential tools used in the automotive industry for creating high-quality rubber joints for car windows and windshields. These molds play a crucial role in ensuring the precise and accurate production of rubber joints, which are integral to the functionality and safety of automotive glass. Here's a comprehensive guide on how to use rubber joint molds for automotive glass:
Mold Preparation: Before using rubber joint molds, it is vital to ensure that the molds are clean and free of any residue from previous use. Thorough cleaning and inspection of the mold's surfaces help prevent defects in the final rubber joint and ensure consistency in the production process.
Rubber Material Selection: Choosing the right rubber material is crucial for creating durable and weather-resistant rubber joints. The selected rubber compound should possess the necessary properties, including flexibility, resilience, and weather resistance. Additionally, it should be compatible with the specific adhesive and priming agents used in the automotive glass assembly process.
Molding Process: The rubber molding process begins with the preparation of the rubber material, which is carefully weighed and mixed according to the manufacturer's specifications. The prepared rubber compound is then placed into the rubber joint mold, ensuring that the mold cavity is entirely filled and free from air pockets or voids.
Curing: Once the mold is filled with the rubber compound, it undergoes a curing process to allow the rubber to solidify and take the desired shape. The curing conditions, including temperature and duration, are determined based on the specific rubber compound used, ensuring optimal curing and cross-linking of the rubber material.
Demolding: After the curing process is complete, the rubber joint is carefully demolded from the rubber joint mold. Careful handling is crucial to avoid any damage to the newly formed rubber joint. Any excess rubber material or flash is trimmed away to achieve the desired final dimensions and ensure a precise fit with the automotive glass.
Quality Control: Strict quality control measures are implemented throughout the rubber molding process to ensure that the produced rubber joints meet the required specifications, including dimensional accuracy, surface finish, and material properties. In-process and post-molding inspections are carried out to identify and rectify any defects or deviations from the set standards.
Installation: The molded rubber joints are then installed in the automotive glass assembly process, providing a secure and weatherproof seal between the glass and the surrounding framework. Proper installation techniques, including the use of adhesives and priming agents, are essential to achieving a reliable and long-lasting bond.
In conclusion, rubber joint molds are indispensable tools in the production of high-quality rubber joints for automotive glass applications. By following the proper procedures and adhering to quality standards, manufacturers can ensure the consistent production of durable and reliable rubber joints essential for automotive safety and performance.
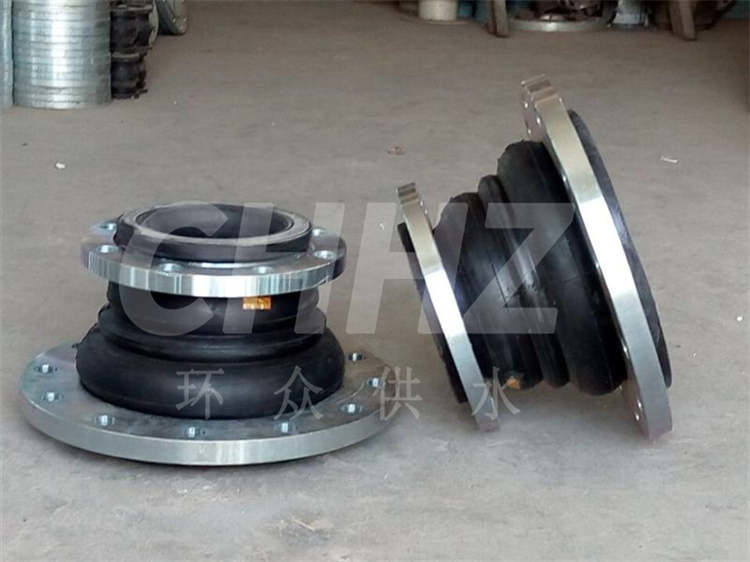