Production Process of Rubber Cable Connectors
Introduction:The production of rubber cable connectors involves a meticulous manufacturing process aimed at creating durable, reliable, and safe components for electrical applications. This article provides an overview of the key stages and techniques involved in the production process of rubber cable connectors, emphasizing the importance of quality, precision, and performance in meeting the diverse demands of electrical connectivity in various industrial and consumer settings.
Raw Material Compounding and Preparation:The production process commences with the careful selection and compounding of raw rubber materials, including elastomers, fillers, curing agents, and other additives essential for achieving the desired mechanical, electrical, and thermal properties. The compounded rubber undergoes rigorous testing and quality control to ensure its compliance with industry standards and specific performance requirements, such as flexibility, insulation resistance, and environmental durability, essential for cable connector applications.
Molding and Vulcanization:Once the rubber compound is prepared, it undergoes molding processes to shape the connector components, such as insulating sleeves, grommets, and sealing elements, according to precise design specifications. The use of injection molding or compression molding techniques enables the creation of intricate geometries and configurations, ensuring a precise fit and sealing interface for the cable connectors. Subsequently, the molded components are subjected to vulcanization processes, where they undergo controlled heat and pressure treatment to attain the desired mechanical properties, such as resilience, tear resistance, and sealing effectiveness.
Metal Insertion and Assembly:Incorporating metal components, such as contact pins, terminals, and conductive elements, into the rubber cable connectors is a crucial step in the production process. Precision assembly techniques, such as overmolding or insert molding, are employed to securely encapsulate and integrate the metal inserts within the rubber components, ensuring robust electrical connections, mechanical strength, and protection against environmental elements. The assembly process also involves meticulous inspection and testing to verify the integrity and functionality of the completed cable connectors.
Quality Control and Testing:Throughout the production process, stringent quality control measures are implemented to assess the dimensional accuracy, material consistency, and functional properties of the rubber cable connectors. Quality assurance protocols encompass electrical testing for insulation resistance, dielectric strength, and continuity, as well as mechanical testing for durability, sealing performance, and environmental resistance. Compliance with industry standards, such as ISO, UL, and IEC, is paramount in ensuring that the manufactured connectors meet the safety, reliability, and performance requirements of diverse applications.
Packaging and Distribution:Upon completion of the production process and successful quality validation, the rubber cable connectors undergo packaging and labeling procedures, facilitating their safe handling, storage, and distribution to customers and end-users. Appropriate packaging materials and protective measures are employed to safeguard the connectors from damage during transit and storage, thereby preserving their quality and performance attributes until they are deployed in electrical systems and applications.
Conclusion:In conclusion, the production process of rubber cable connectors involves a series of precise and controlled manufacturing techniques aimed at creating high-quality, reliable, and durable components for electrical connectivity. From raw material compounding and molding to metal insertion, assembly, quality control, and packaging, every stage of the process emphasizes precision, performance, and compliance with industry standards to ensure that the manufactured connectors meet the demands of diverse electrical applications. By adhering to these rigorous production practices, manufacturers contribute to the supply of safe, dependable, and resilient cable connectors essential for the efficient and secure operation of electrical systems across industries.
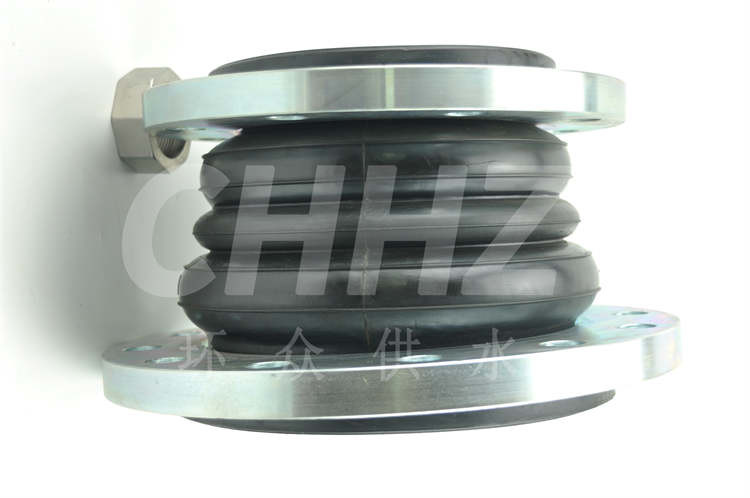