Metal Expansion Joints vs. Rubber Expansion Joints: A Comparison
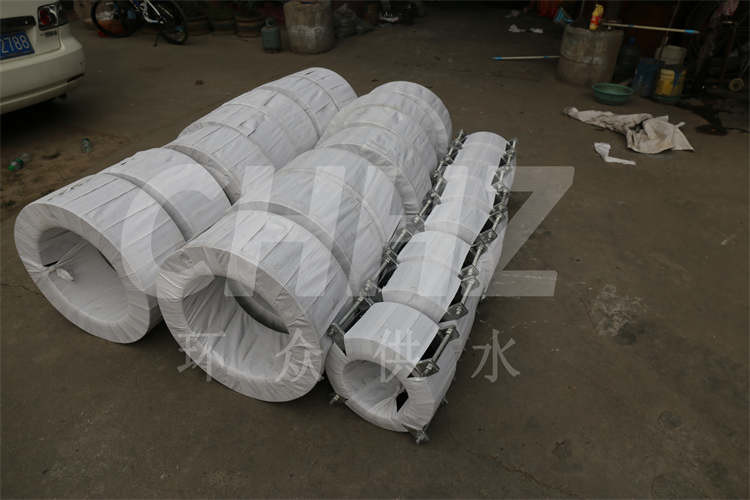
Introduction:Both metal expansion joints and rubber expansion joints serve critical roles in accommodating thermal expansion, misalignment, and vibration in piping systems and industrial applications. Each type of joint offers unique characteristics and advantages. This article aims to compare the features and benefits of metal expansion joints and rubber expansion joints to determine the suitability of each for different applications based on their specific attributes.
Metal Expansion Joints:Metal expansion joints, often fabricated from stainless steel or other alloys, are known for their exceptional resistance to high temperatures, corrosive environments, and high-pressure conditions. The inherent strength and durability of metal expansion joints make them well-suited for applications involving extreme operating conditions, such as petrochemical plants, power generation facilities, and industrial processing systems. Their ability to withstand thermal cycling and exposure to aggressive media makes them a reliable choice for critical process piping where safety, longevity, and leak-proof performance are paramount.
The flexibility of metal expansion joints allows them to absorb thermal expansion and contraction while maintaining structural integrity. Their robust construction and resistance to vibration make them ideal for applications subject to mechanical movement and dynamic loads. Additionally, metal expansion joints offer precise control over movements in multiple directions, making them suitable for complex piping configurations and systems with variable operating conditions.
Rubber Expansion Joints:Rubber expansion joints, constructed from elastomeric materials such as neoprene, EPDM, or natural rubber, provide excellent flexibility and vibration isolation properties. These joints are particularly effective in applications that require noise reduction, shock absorption, and minimal transmission of vibration, such as HVAC systems, pump connections, and water treatment facilities. Their ability to dampen vibrations and accommodate moderate thermal movements makes them a preferred choice for applications where cost-effectiveness and ease of installation are key considerations.
Rubber expansion joints offer good chemical resistance and can be designed to handle a wide range of temperatures, although they may have limitations in extreme temperature or abrasive environments compared to metal expansion joints. Their lightweight and flexible nature simplifies installation and maintenance, making them suitable for retrofitting or replacing existing piping systems without significant modifications.
Choosing the Right Joint for Your Application:The selection of metal expansion joints or rubber expansion joints depends on the specific requirements of the application. Factors such as temperature range, pressure conditions, media compatibility, movement capacity, and environmental considerations should be carefully evaluated to determine the most suitable type of expansion joint. While metal expansion joints excel in high-temperature, high-pressure, and corrosive environments, rubber expansion joints offer advantages in applications requiring vibration isolation, noise reduction, and cost-effective solutions.
In conclusion, both metal expansion joints and rubber expansion joints have distinct advantages that cater to different needs in industrial and piping applications. The decision to choose one over the other should be based on a thorough assessment of the operating conditions, performance requirements, and long-term reliability of the system. By understanding the unique characteristics and capabilities of metal and rubber expansion joints, engineers and operators can make informed decisions to optimize the efficiency, safety, and integrity of their piping systems.
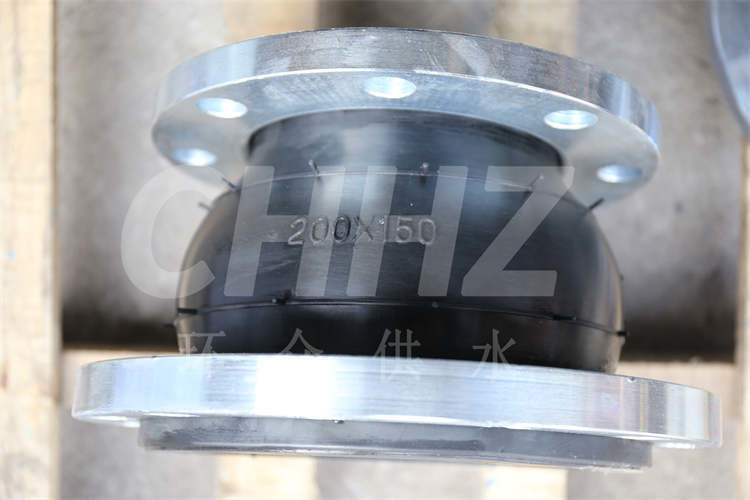