The Differences Between Rubber Hose and Metal Pipe Joints
Introduction: Rubber hoses and metal pipes are critical components in various industrial and domestic applications, serving as conduits for fluid and gas transportation. The joint connections used to connect these components play a pivotal role in ensuring their performance and reliability. This article aims to highlight the key differences between rubber hose joints and metal pipe joints in terms of their construction, properties, and applications.
Material Composition: Rubber Hose Joints: Rubber hose joints are typically composed of flexible rubber or elastomeric materials such as synthetic polymers. These materials offer resilience, flexibility, and resistance to abrasion and impact, making them suitable for applications where vibration and movement are present.
Metal Pipe Joints: In contrast, metal pipe joints are constructed from rigid metallic materials, such as steel, stainless steel, or aluminum. These materials provide structural strength, dimensional stability, and resistance to high pressure and temperature, making them well-suited for demanding industrial environments.
Flexibility and Movement: Rubber Hose Joints: The flexibility and elasticity of rubber hose joints enable them to absorb vibrations, accommodate movement, and bend around obstacles. This makes them ideal for dynamic applications where frequent movement or flexing is required, such as in automotive, hydraulic, and pneumatic systems.
Metal Pipe Joints: Metal pipe joints, being rigid in nature, are less flexible and more susceptible to damage or fatigue when subjected to bending or movement. They are commonly used in stationary or fixed installations where structural rigidity and stability are paramount, such as in plumbing, industrial piping, and structural frameworks.
Sealing and Leakage Prevention: Rubber Hose Joints: The inherent resilience and compressibility of rubber materials allow rubber hose joints to form tight, reliable seals, even in irregular or uneven mating surfaces. This property minimizes the risk of leakage in fluid or gas transfer applications.
Metal Pipe Joints: Metal pipe joints rely on threaded, welded, or flanged connections to achieve sealing, often requiring additional sealing materials such as gaskets, sealing compounds, or welding techniques. While effective, these methods may be more prone to leaks or failure under dynamic or high-vibration conditions.
Application Diversity: Rubber Hose Joints: The flexibility and chemical compatibility of rubber hose joints make them suitable for a wide range of applications, including conveying water, air, gases, oils, and various fluids in industries such as automotive, construction, agriculture, and manufacturing.
Metal Pipe Joints: Metal pipe joints are commonly employed in applications involving high-pressure or high-temperature fluids, corrosive chemicals, or structural support requirements, such as in petrochemical processing, HVAC systems, hydraulic systems, and industrial plumbing.
Conclusion: In summary, rubber hose joints and metal pipe joints offer distinct advantages and characteristics, catering to different operational requirements and environmental conditions. Understanding the differences between these joint types is essential for selecting the most suitable connection method for specific fluid and gas transfer applications in diverse industries.
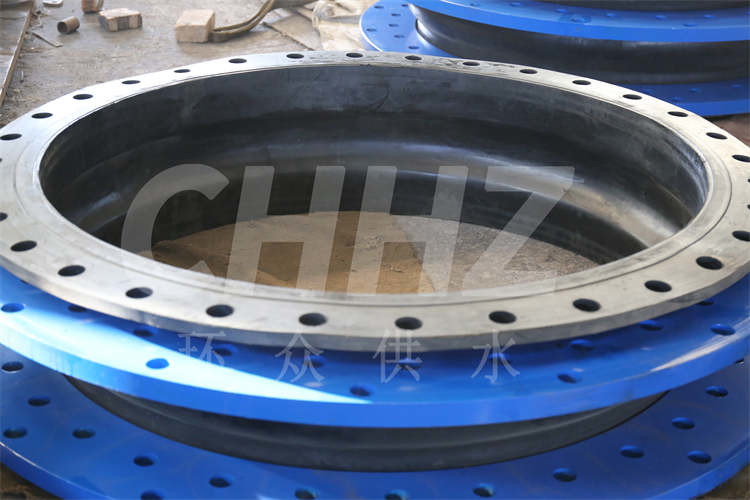