How to Heat Weld Plastic or Rubber Waterstops: An English Article
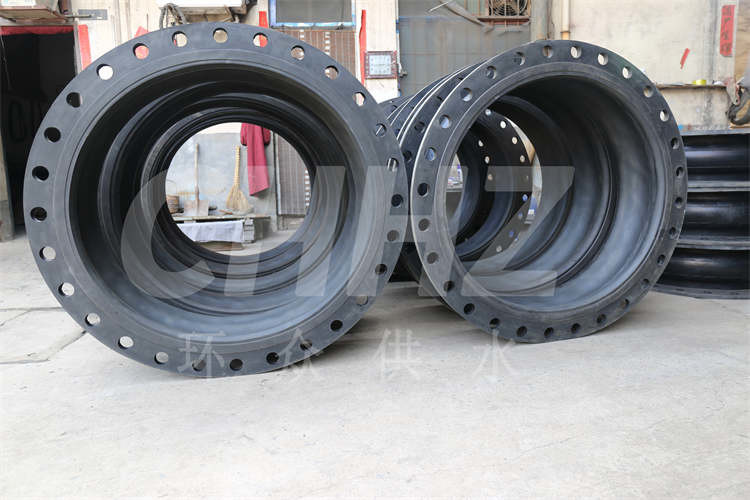
Heat welding plastic or rubber waterstops is a crucial process for creating effective barrier systems in construction and civil engineering projects. Properly executed heat welding ensures seamless and watertight joints, thereby safeguarding structures against water infiltration and damage. In this article, we will explore the steps and techniques involved in heat welding plastic or rubber waterstop joints, emphasizing the importance of precision and adherence to best practices.
1. Surface Preparation:Before heat welding, it is essential to prepare the surfaces of the plastic or rubber waterstop components. This involves removing any dirt, debris, or foreign materials that could hinder the welding process. The surfaces must be clean, dry, and free from contaminants to facilitate optimal bonding during the heat welding procedure.
2. Heating Equipment and Temperature Control:Using specialized heat welding equipment is fundamental to achieving consistent and reliable results. Heat welding machines, equipped with controlled heating elements, are employed to heat the plastic or rubber waterstop materials to their fusion temperature. It is crucial to set the welding temperature according to the specific requirements of the material being joined, as overheating or underheating can compromise the integrity of the weld.
3. Joint Alignment and Clamping:Proper alignment of the waterstop components is critical for establishing a uniform and secure weld. Aligning the edges of the materials to be joined and using clamps or fixtures to hold them in place is necessary to prevent shifting during the welding process. This ensures that the resulting bond is structurally sound and resistant to water pressure.
4. Welding Technique:The heat welding technique involves bringing the prepared surfaces of the plastic or rubber waterstop into close contact with the heated welding equipment. As the materials reach the fusion temperature, pressure is applied to bond them together, resulting in a homogenous and continuous joint. Careful control of the welding speed, pressure, and dwell time is essential to achieve a consistent and watertight weld across the entire joint length.
5. Inspection and Quality Assurance:Following the completion of the heat welding process, a thorough visual and, if necessary, non-destructive inspection is carried out to assess the quality of the joint. Weld integrity, uniformity, and the absence of defects or voids are key aspects evaluated during the inspection. Only joints that meet the designated quality standards are approved for installation in water containment structures.
In conclusion, heat welding plastic or rubber waterstops demands meticulous attention to detail and adherence to established procedures. By diligently preparing surfaces, using specialized welding equipment, ensuring joint alignment and clamping, employing precise welding techniques, and conducting thorough quality inspections, constructors and engineers can produce robust and reliable waterstop joints that effectively prevent water ingress and enhance the durability of civil infrastructure.
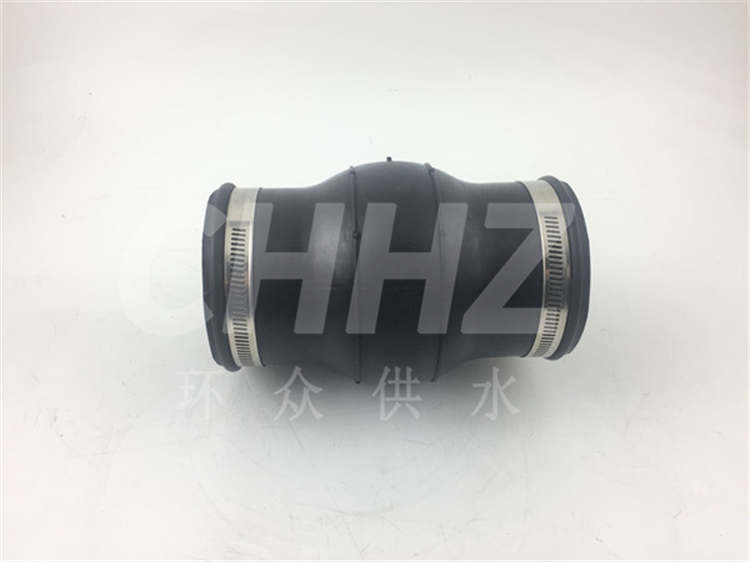