Differences Between Metal Flexible Connectors and Rubber Flexible Joints
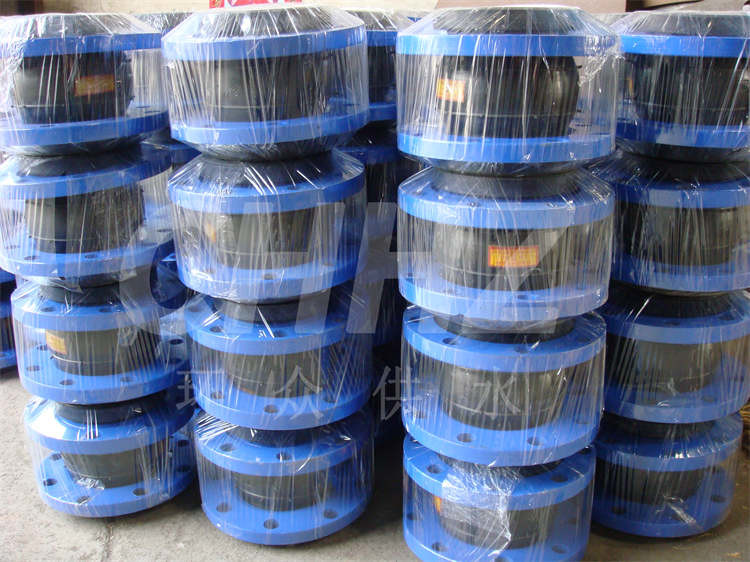
Metal flexible connectors and rubber flexible joints are both important components used in piping systems, offering flexibility and vibration isolation. Although they serve similar purposes, they have distinct characteristics and applications. This article will explore the key differences between metal flexible connectors and rubber flexible joints in piping systems.
Material Composition:The most obvious difference lies in the material composition. Metal flexible connectors are typically made of stainless steel, carbon steel, or other metallic alloys. These materials provide high tensile strength and corrosion resistance, making metal connectors suitable for high-pressure and high-temperature applications. In contrast, rubber flexible joints are constructed from elastomeric materials, such as natural rubber or synthetic rubber compounds. Rubber joints offer exceptional flexibility and damping properties, making them ideal for absorbing vibration and noise in a system.
Flexibility and Movement:Metal flexible connectors are designed to absorb thermal expansion, contraction, and dynamic motion within the piping system. Their flexibility allows for angular, axial, and lateral movement, and they are often used in applications where rigid connections would be impractical due to vibrations or misalignment. On the other hand, rubber flexible joints excel in absorbing and isolating vibration and noise generated by the piping system. They are particularly effective in reducing the transmission of sound and vibrations, protecting the surrounding equipment and structures from damage.
Pressure and Temperature Resistance:Metal flexible connectors are engineered to withstand high-pressure and high-temperature conditions. Their robust construction and metallic composition make them well-suited for demanding industrial applications, such as steam, gas, and chemical transfer lines. Rubber flexible joints are generally not intended for high-pressure or high-temperature environments. Instead, they are commonly used in lower pressure systems where vibration dampening and noise reduction are the primary concerns.
Corrosion Resistance:Metal flexible connectors offer superior corrosion resistance due to their metallic composition. They are often employed in corrosive environments to prevent leaks and structural damage caused by chemical exposure. Rubber flexible joints, while offering some degree of resistance to mild chemical exposure, may not be suitable for prolonged use in highly corrosive environments.
Installation and Maintenance:
Metal flexible connectors require precise installation to ensure proper alignment and performance under pressure. Additionally, periodic inspection and maintenance are necessary to monitor for signs of fatigue or wear. Rubber flexible joints are relatively easy to install and maintain, making them a preferred choice for applications where simplicity and ease of maintenance are valued.
In summary, the choice between metal flexible connectors and rubber flexible joints depends on the specific requirements of the piping system, including pressure, temperature, vibration, and corrosion considerations. Each type of connector offers unique benefits and performance characteristics, and understanding these differences is crucial for selecting the appropriate component to optimize the overall functionality and longevity of the piping system.
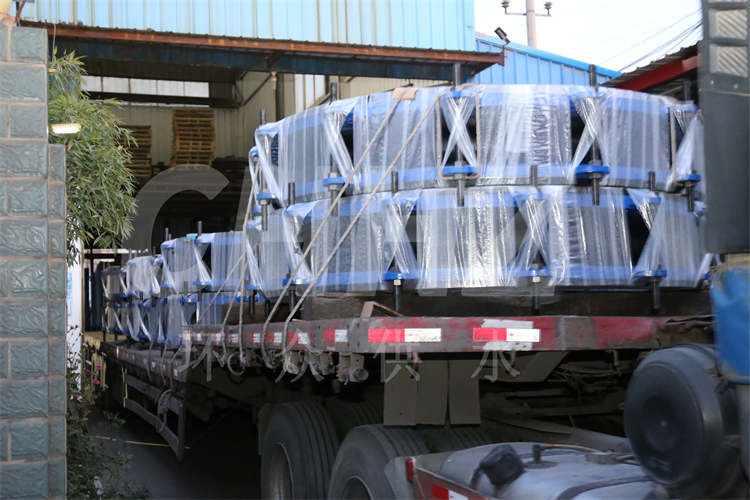