Rubber Hose Joint: Flexible Connection for Engineering Applications
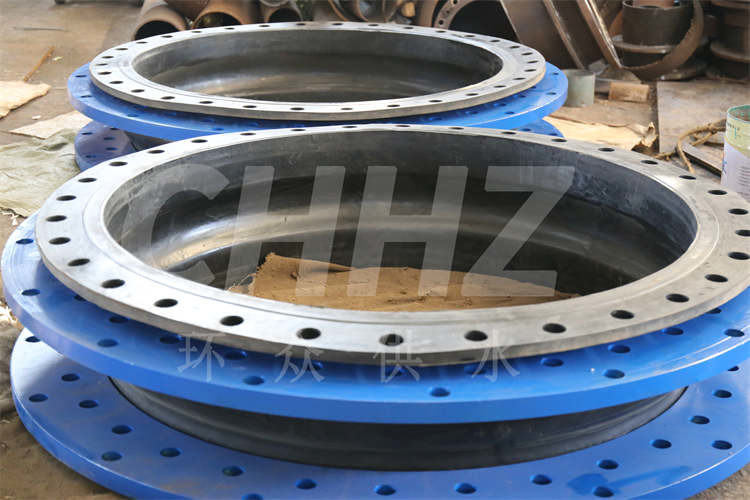
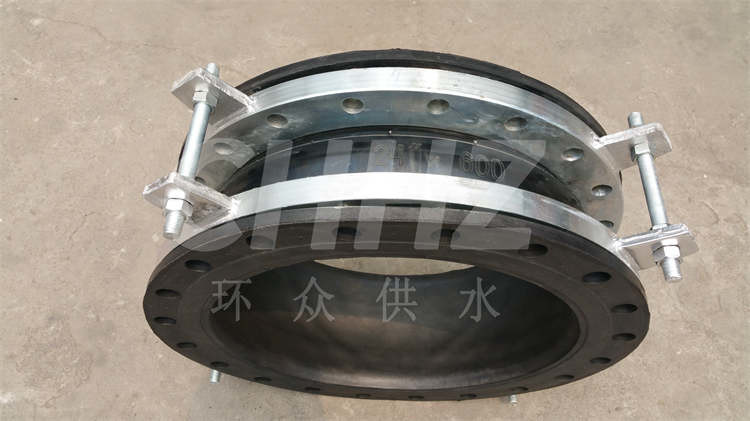
Rubber hose joints are critical components that enable flexible connections within various engineering applications across industries such as automotive, manufacturing, and construction. These joints play a pivotal role in accommodating movement, absorbing vibrations, and providing a reliable conduit for the transfer of fluids or gases. This article aims to expound on the significance, characteristics, and key considerations related to rubber hose joints in engineering applications.
1. Flexibility and Absorption of Movement:Rubber hose joints are designed to provide flexibility, allowing for the movement and misalignment of components while maintaining a sealed connection. This flexibility proves indispensable in situations where machinery undergoes vibrations, thermal expansion, or dynamic loads. By absorbing these movements, rubber hose joints help to protect the integrity of the overall system and minimize stress on interconnected components.
2. Material Selection and Compatibility:The materials used in the production of rubber hose joints are carefully chosen to ensure compatibility with the conveyed media and environmental conditions. Common materials include natural rubber, neoprene, EPDM, and silicone, each offering distinct advantages in terms of temperature resistance, chemical compatibility, and durability. The choice of material is crucial in safeguarding against degradation and ensuring the long-term reliability of the joint.
3. Structural Reinforcement:Rubber hose joints may incorporate internal or external reinforcements to enhance their structural integrity and resistance to pressure. Reinforcements such as fabric layers, wire helixes, or metal rings serve to prevent the expansion or deformation of the hose under the influence of internal pressure, thereby bolstering the overall performance and safety of the connection.
4. End Fittings and Attachments:The selection of appropriate end fittings and attachments is paramount to ensuring a secure and leak-proof connection to the adjoining components or systems. These fittings can include clamps, flanges, threaded connectors, or quick-release couplings, each tailored to the specific requirements of the application. Proper installation and sealing techniques further contribute to the effectiveness and longevity of the joint.
5. Maintenance and Inspection:Regular inspection and maintenance of rubber hose joints are essential to detect signs of wear, damage, or deterioration that could compromise their performance. Visual checks for leaks, swelling, or cracking, combined with periodic replacement schedules, are vital practices to uphold the integrity of the joints and minimize the risk of system failures.
In conclusion, rubber hose joints serve as indispensable components in engineering applications, providing the required flexibility, movement absorption, and fluid transfer capabilities. By considering factors such as material selection, structural reinforcement, end fittings, and maintenance practices, engineers can ensure the reliable and efficient performance of rubber hose joints within their systems. Embracing these considerations fosters the safe and uninterrupted operation of various engineering applications, reinforcing the indispensable role of rubber hose joints in modern engineering practices.
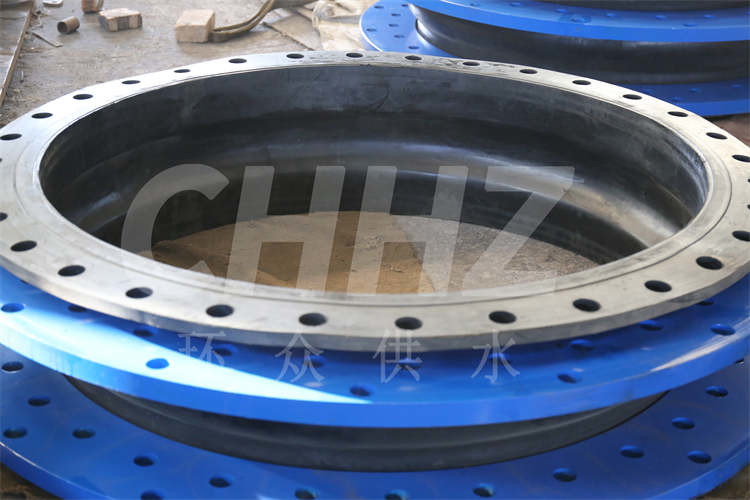