The Production Process of Rubber Cable Connectors
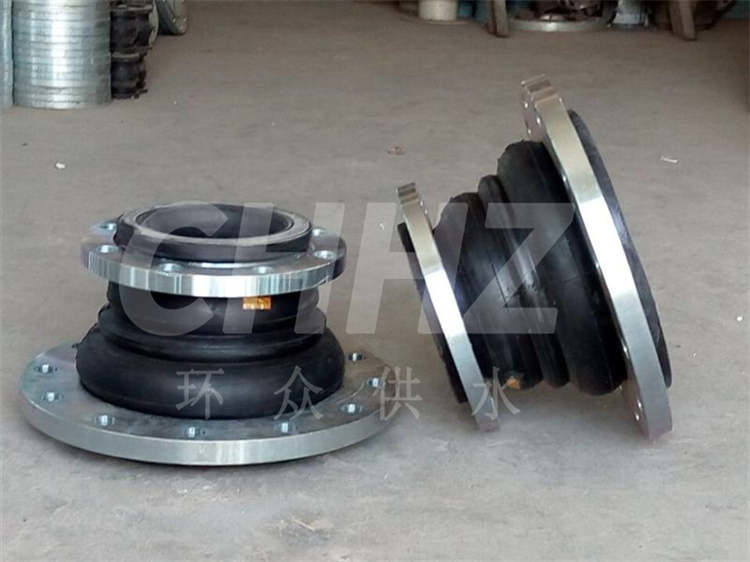
Rubber cable connectors play a crucial role in the transmission and distribution of electrical power, making them essential components in various industrial and commercial applications. The production process of rubber cable connectors involves several stages of manufacturing and assembly, each of which is critical to ensuring the quality, performance, and safety of the final product. This article provides an overview of the production process of rubber cable connectors, highlighting the key steps involved in their fabrication.
1. Raw Material Preparation: The production process begins with the preparation of raw materials, including high-quality rubber compounds, conductive materials, insulating agents, and metal components such as terminals and connectors. The rubber compounds are formulated to possess the required electrical and mechanical properties, while the conductive and insulating materials are selected based on their performance characteristics.
2. Extrusion and Molding: The rubber compounds are processed through extrusion and molding techniques to form the basic structure of the cable connector. Extrusion involves forcing the rubber material through a specially designed die to produce uniform cross-sectional shapes, such as cables and insulating sleeves. Molding is used to create more complex components, including connector housings and insulation layers, through the application of heat and pressure.
3. Vulcanization: Vulcanization is a crucial stage in the production process, during which the molded or extruded rubber components are subjected to heat and pressure to cross-link the rubber molecules. This results in improved elasticity, strength, and resistance to electrical and thermal stress, thereby enhancing the overall performance and durability of the cable connectors.
4. Conductive Element Assembly: The conductive elements, including copper or aluminum conductors, are assembled and integrated into the rubber components to establish electrical connectivity. This involves precise positioning and bonding of the conductors within the cable connector structure, ensuring reliable current transmission and minimizing power losses.
5. Insulation and Sheathing: Insulation layers are applied to the conductive elements to prevent electrical leakage, enhance dielectric strength, and provide protection against environmental factors. Additionally, the rubber cable connectors are sheathed with an outer layer of rubber or synthetic material to enhance mechanical strength, abrasion resistance, and resistance to chemical and environmental hazards.
6. Quality Control and Testing: Throughout the production process, rigorous quality control measures are implemented to monitor the dimensions, material properties, and performance characteristics of the cable connectors. Various tests, including electrical conductivity, insulation resistance, mechanical strength, and environmental resistance, are conducted to ensure compliance with industry standards and specifications.
7. Final Assembly and Packaging: Following the completion of manufacturing and testing, the rubber cable connectors undergo final assembly, where terminals, connectors, and accessories are installed as per customer requirements. The finished products are then carefully packaged to protect them from damage during transportation and storage.
In summary, the production process of rubber cable connectors involves a series of well-defined stages, encompassing raw material preparation, extrusion, molding, vulcanization, assembly, quality control, and final packaging. Each stage plays a crucial role in ensuring the quality, performance, and safety of the cable connectors, thereby meeting the diverse needs of electrical power distribution in industrial and commercial settings. By adhering to stringent manufacturing standards and implementing robust quality assurance measures, manufacturers can produce rubber cable connectors that exhibit reliability, durability, and optimal electrical performance.
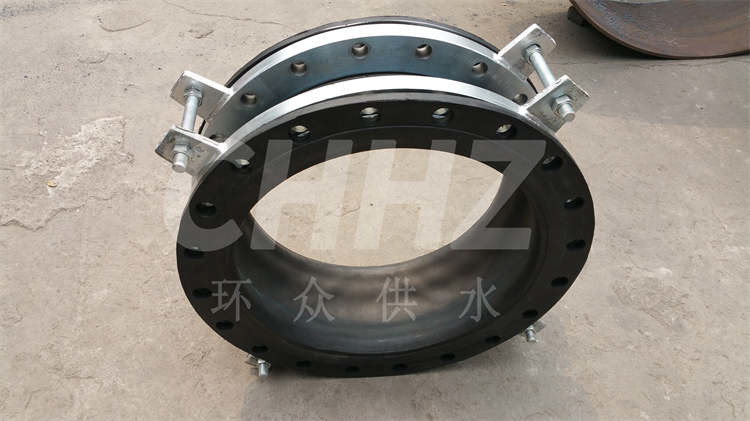