Rubber Cable Joint Molding Process
The molding process for rubber cable joints is a crucial step in ensuring the proper formation and integrity of electrical connections. This article outlines the key steps and considerations involved in the molding process for rubber cable joints, emphasizing the importance of precision, material selection, and adherence to industry standards.
Preparation: The molding process begins with the careful preparation of the rubber material to be used for the cable joint. The rubber compound selected must possess the appropriate physical and chemical properties to withstand the environmental conditions and operational requirements to which the cable joint will be subjected. Factors such as elasticity, insulation properties, and resistance to heat, moisture, and chemicals are critical in determining the suitability of the rubber compound for the molding process.
Mold Design and Fabrication: The next step involves the design and fabrication of the mold that will shape the rubber material into the desired form of the cable joint. The mold is crafted to precise specifications, considering the dimensions, contours, and features required for accommodating the electrical components and creating a secure and reliable connection. The design of the mold is tailored to the specific requirements of the cable joint, ensuring a customized and precise molding process.
Injection Molding: Injection molding is a widely used technique for shaping rubber cable joints. In this process, the prepared rubber compound is heated to a molten state and injected into the mold under controlled pressure. The mold is then cooled to solidify the rubber material, resulting in the formation of the cable joint in the desired shape and configuration. Injection molding allows for high precision and repeatability, enabling the production of cable joints with consistent quality and dimensional accuracy.
Curing and Vulcanization: Following the injection molding process, the molded cable joint undergoes curing and vulcanization to achieve the desired physical and chemical properties. Curing involves subjecting the rubber material to controlled heat and pressure, allowing it to undergo cross-linking reactions that enhance its strength, resilience, and durability. Vulcanization further reinforces the rubber compound, imparting qualities such as resistance to environmental stress, aging, and mechanical strain.
Trimming and Finishing: Once the rubber cable joint has undergone curing and vulcanization, it is trimmed and finished to remove any excess material, refine the surface contours, and ensure that the dimensions conform precisely to the design specifications. Finishing processes such as polishing and surface treatments may be applied to enhance the aesthetic appearance and facilitate the installation of the cable joint.
Quality Assurance: Throughout the molding process, stringent quality control measures are implemented to assess the integrity, dimensional accuracy, and material properties of the rubber cable joint. Inspection, testing, and adherence to industry standards are essential to verify the performance and reliability of the molded joints, ensuring that they meet the required specifications and regulatory requirements.
In conclusion, the molding process for rubber cable joints involves a series of critical steps aimed at achieving precision, functionality, and durability. By carefully selecting the rubber compound, designing and fabricating molds, implementing injection molding techniques, and subjecting the molded joints to curing and vulcanization, manufacturers can produce cable joints of high quality and performance. Adherence to stringent quality assurance practices reinforces the reliability and safety of the molded cable joints, contributing to their long-term effectiveness in electrical applications.
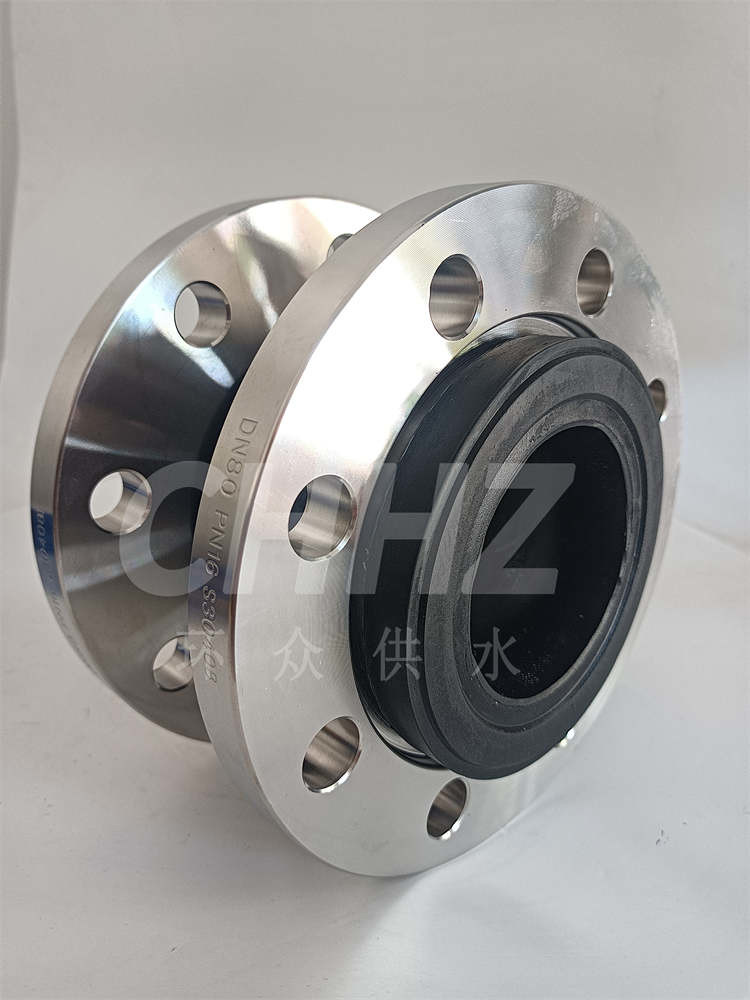