Differences Between Metal Hose and Rubber Joint
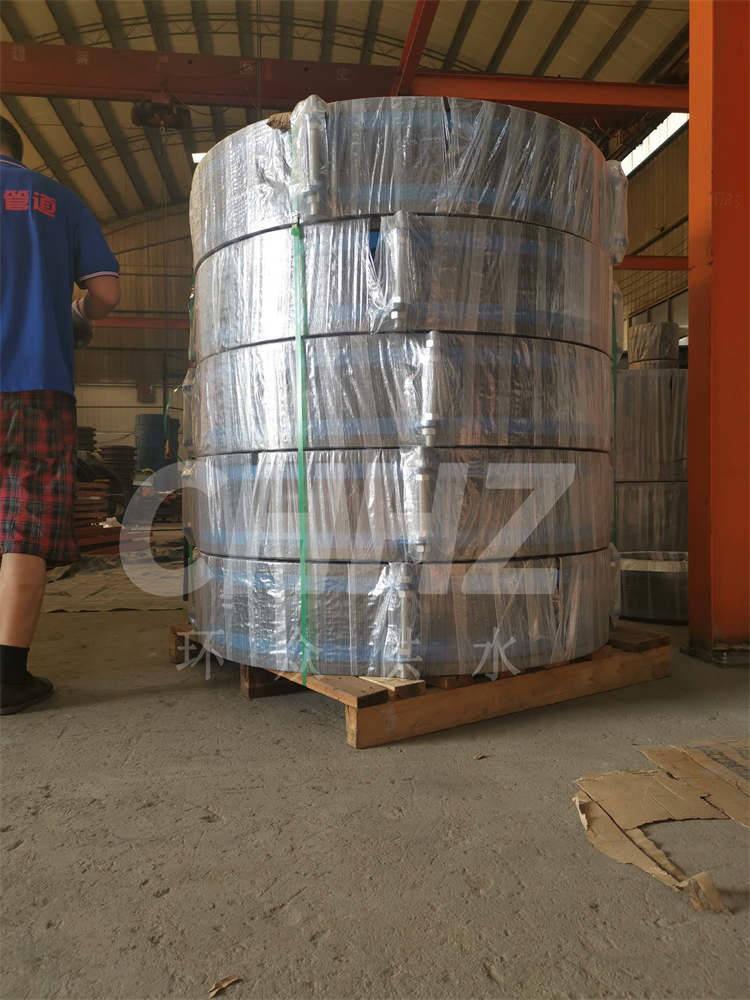
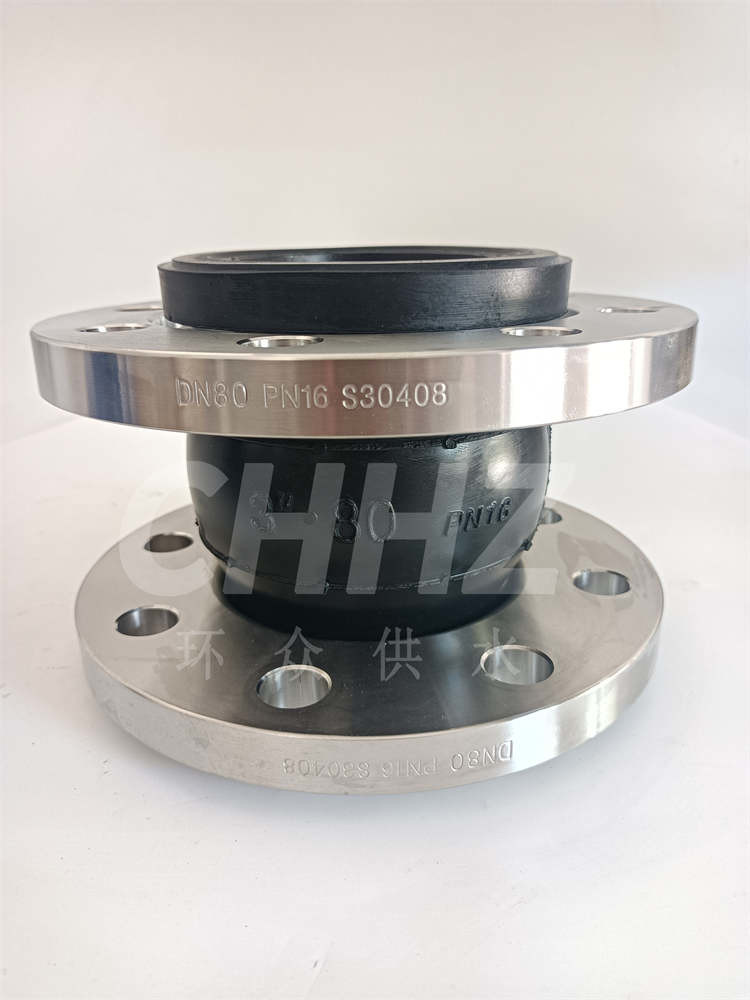
In various industrial applications, the choice between using a metal hose and a rubber joint depends on specific operational requirements. Understanding the differences between these components is crucial for selecting the most suitable option for a given application. This article provides an overview of the distinctions between metal hoses and rubber joints.
Material Composition: The most apparent difference between metal hoses and rubber joints lies in their material composition. Metal hoses are typically constructed from stainless steel or other metals, ensuring high durability and resistance to corrosion and extreme temperatures. In contrast, rubber joints are primarily made from elastomeric materials such as natural or synthetic rubber, which provide flexibility and resilience for accommodating movement and vibration.
Flexibility and Movement: Metal hoses and rubber joints differ significantly in their capacity to handle movement and flexibility. Metal hoses are capable of withstanding high-pressure loads and are often employed in applications where rigidity and resistance to high temperatures are crucial. On the other hand, rubber joints excel in absorbing and compensating for movement, thermal expansion, and vibration within the piping system, making them suitable for applications involving dynamic conditions.
Sealing Performance: Another key distinction between metal hoses and rubber joints is their sealing performance. Metal hoses are known for their excellent sealing capabilities, ideal for applications requiring airtight or watertight connections. In contrast, rubber joints provide effective sealing along with the ability to accommodate misalignments and movement, making them suitable for applications where flexibility and vibration absorption are paramount.
Noise and Vibration Damping: Rubber joints are preferred over metal hoses in applications where noise and vibration damping are critical. The inherent flexibility and elasticity of rubber joints allow them to minimize the transmission of vibrations and noise from the piping system, contributing to a quieter and more stable operational environment.
Environmental Resistance: Metal hoses are renowned for their exceptional resistance to a wide range of chemicals, high temperatures, and harsh environmental conditions, making them suitable for demanding applications in chemical processing, power generation, and aerospace industries. Meanwhile, rubber joints exhibit superior resistance to abrasion, impact, and environmental exposure, making them ideal for applications where protection against physical wear and tear is essential.
In conclusion, metal hoses and rubber joints offer distinct advantages based on their material composition, flexibility, sealing performance, noise and vibration damping capabilities, and environmental resistance. Understanding the differences between these components is essential for selecting the most appropriate solution to meet the specific requirements of industrial applications.
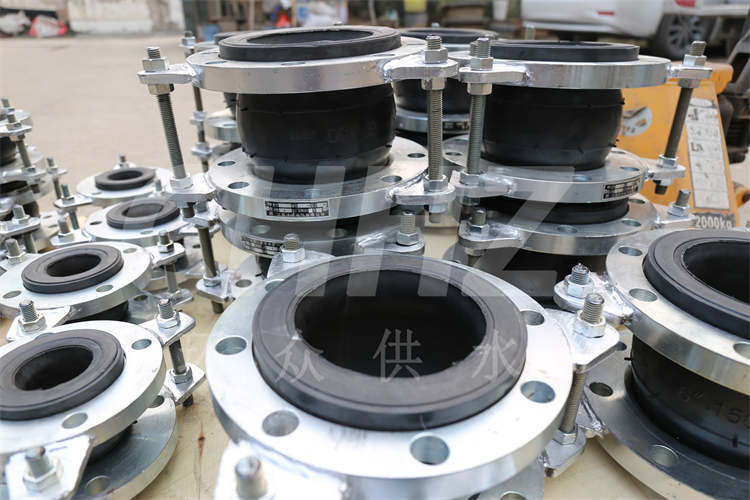