The Basic Materials of Rubber for Automotive Hose Connectors
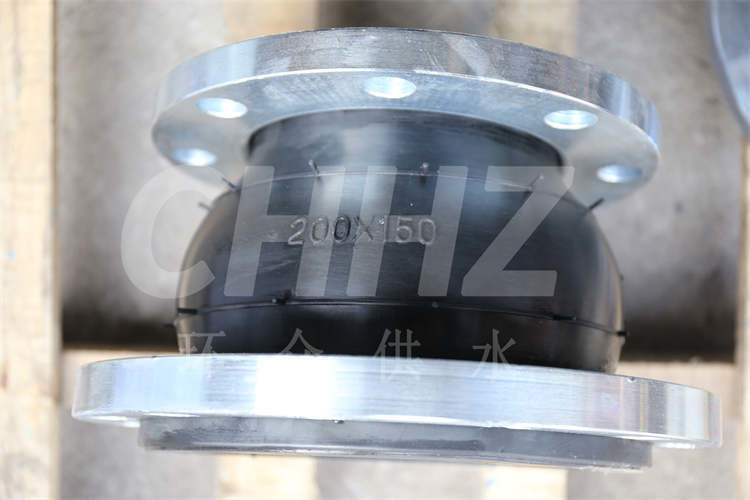
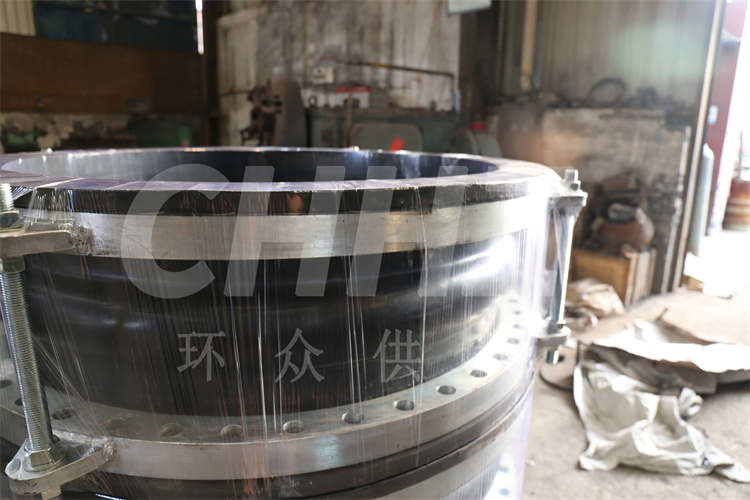
Introduction: Rubber plays a critical role in the production of automotive hose connectors, providing essential sealing and flexibility properties. This article explores the fundamental materials used in the manufacturing of rubber for automotive hose connectors and the key considerations associated with their selection and performance.
Material Composition: The rubber materials employed in automotive hose connectors primarily consist of elastomers, which are polymers displaying elastic properties. Key rubber compounds utilized in hose connectors include Ethylene Propylene Diene Monomer (EPDM), Nitrile Butadiene Rubber (NBR), Silicone, and Fluorocarbon Rubber (Viton). Each of these materials has distinct attributes, making them suitable for specific operating conditions and environmental exposures.
EPDM: Ethylene Propylene Diene Monomer (EPDM) is widely used in automotive hose connectors due to its exceptional resistance to weathering, ozone, and heat. EPDM rubber is known for its ability to withstand exposure to water and steam, making it an ideal choice for coolant system components and applications requiring resistance to environmental elements.
NBR: Nitrile Butadiene Rubber (NBR) is valued for its excellent oil and fuel resistance, making it a preferred material for automotive fuel system hose connectors. NBR rubber provides robust sealing properties, durability, and resilience, essential for maintaining leak-free connections vital in fuel handling applications.
Silicone: Silicone rubber is favored for its high-temperature resistance, flexibility, and aging characteristics. It is commonly utilized in automotive hose connectors for applications requiring resistance to extreme temperatures, such as in turbocharger and intercooler systems, as well as in radiator hoses.
Viton: Fluorocarbon Rubber or Viton is renowned for its exceptional resistance to high temperatures, chemicals, and automotive fluids. As a result, Viton is utilized in automotive hose connectors for applications that demand resistance to aggressive fluids, including engine oil, transmission fluid, and various automotive fluids.
Performance Considerations: When selecting rubber materials for automotive hose connectors, factors such as chemical compatibility, temperature resistance, environmental exposure, and mechanical properties need to be carefully evaluated. Proper material selection is vital to ensure that the rubber used in hose connectors can withstand the specific demands of the intended application, thereby ensuring long-term performance and reliability.
Conclusion: The diverse range of rubber materials available for automotive hose connectors underscores the critical role of rubber in facilitating superior sealing, flexibility, and durability in automotive applications. By understanding the unique attributes of rubber materials such as EPDM, NBR, silicone, and Viton, automotive manufacturers and engineers can make informed decisions to meet the stringent performance requirements of hose connectors in various automotive systems. Effective evaluation and selection of rubber materials can contribute to the longevity and functionality of automotive hose connectors, ensuring optimal performance and safety in automotive operations.
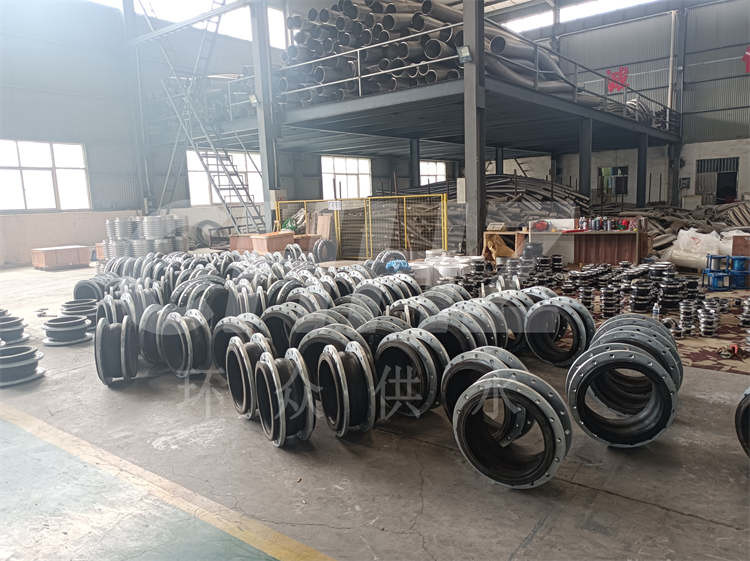