Application of Rubber Joints in Die Casting Machines
Die casting machines are essential for the manufacturing of a wide range of metal components used in numerous industries. The proper functioning of these machines relies on the efficient management of hydraulic and mechanical forces. Rubber joints play a crucial role in ensuring the smooth operation and long-term durability of die casting machines. This article will discuss the application of rubber joints in die casting machines and their significance in maintaining operational integrity.
Sealing and Damping Properties Rubber joints in die casting machines are commonly used to provide sealing and damping functions for hydraulic and pneumatic systems. These joints effectively absorb pressure surges, reduce vibration, and compensate for minor misalignments, thus protecting the machine's components from excessive wear and tear.
Preventing Transmission of Mechanical Shock The high-pressure nature of die casting operations necessitates the prevention of mechanical shock transmission throughout the system. Rubber joints effectively isolate and dampen shock waves and vibrations, safeguarding sensitive components such as pumps, valves, and hydraulic cylinders from damage.Flexibility and Alignment Compensation Rubber joints offer flexibility to accommodate minor misalignments and thermal expansions that occur during the operation of the die casting machine. This flexibility aids in maintaining the integrity of the hydraulic and pneumatic circuits, ensuring consistent performance under varying operational conditions.
Corrosion and Chemical Resistance In die casting environments, exposure to hydraulic fluids, coolants, and other chemicals is common. Rubber joints are designed to resist the effects of corrosion and deterioration caused by chemical exposure, thus contributing to the longevity of the machine's hydraulic and pneumatic systems.
Noise Reduction The damping properties of rubber joints also contribute to the reduction of noise generated during die casting operations. By absorbing mechanical vibrations and minimizing resonance, rubber joints help create a more comfortable and safe working environment for machine operators.
Enhancing Overall System Reliability With their ability to maintain tight seals, absorb shock, and provide flexibility, rubber joints enhance the overall reliability and operational efficiency of die casting machines. This leads to reduced downtime, lower maintenance costs, and improved productivity.
In conclusion, the application of rubber joints in die casting machines is instrumental in ensuring the efficiency, safety, and longevity of these critical manufacturing systems. The unique properties of rubber joints contribute to the smooth and reliable operation of hydraulic and pneumatic circuits, thereby optimizing the performance of die casting machines and enhancing the quality of manufactured components.
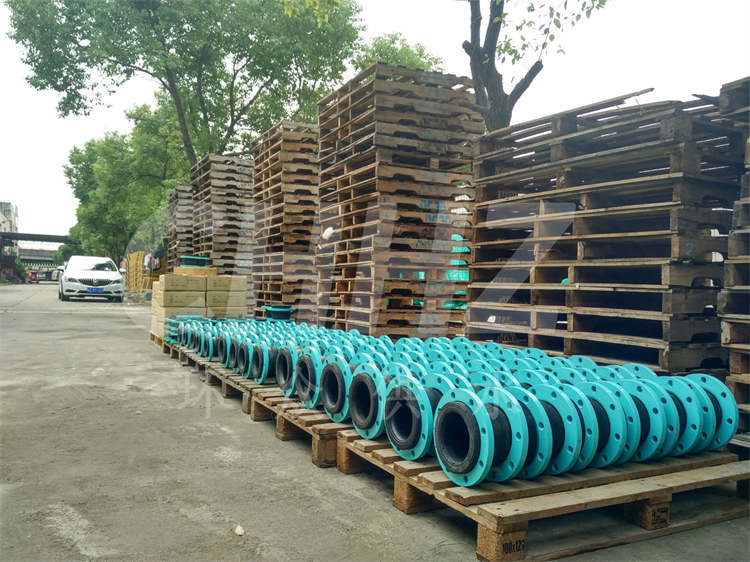