Rubber Shock Absorber Joint for Injection Molding Machine - Time and Effort Saving
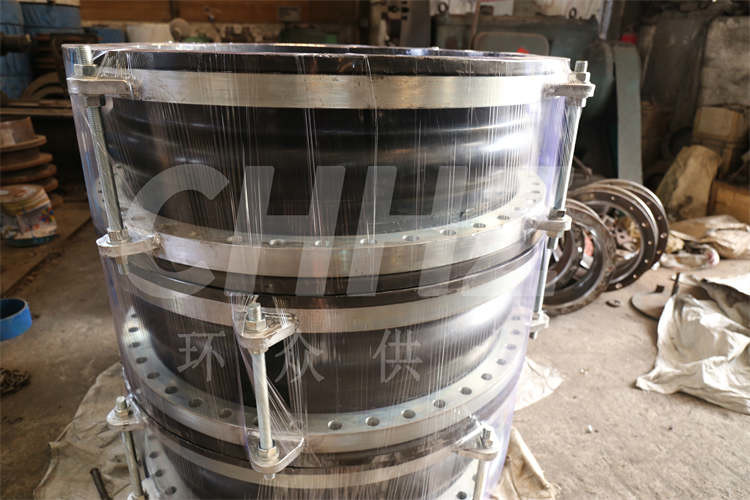
The rubber shock absorber joint, also known as a rubber vibration dampening joint, plays a crucial role in injection molding machines. It effectively reduces vibration and noise, thereby improving the overall performance of the equipment. This article delves into the advantages of using rubber shock absorber joints in injection molding machines, highlighting how they save time and effort.
Vibration Dampening Properties: Rubber shock absorber joints are designed with superior vibration dampening properties, which mitigates the transmission of machine-generated vibrations. As a result, they contribute to a significant reduction in noise and vibration levels during the operation of injection molding machines. This feature not only enhances the working environment but also minimizes wear and tear on the equipment, thereby extending its service life and reducing maintenance requirements.
Easy Installation: The installation of rubber shock absorber joints is a time-efficient process. These joints are typically designed for quick and convenient installation, allowing them to be easily incorporated into the existing structure of the injection molding machine. With minimal time and effort required for installation, the production downtime associated with integrating these components is significantly reduced, leading to improved operational efficiency.
Enhanced Worker Comfort and Safety: By effectively dampening vibrations and reducing noise, rubber shock absorber joints contribute to a more comfortable and safe working environment for machine operators and other personnel. The mitigation of excessive vibration levels helps in preventing fatigue and discomfort among workers, consequently boosting productivity and promoting a healthier workplace.
Maintenance and Downtime Reduction: The integration of rubber shock absorber joints can lead to a reduction in maintenance-related downtime for injection molding machines. The dampening of vibrations and resultant reduction in wear and tear on machine components translate into fewer maintenance interventions and prolonged operational uptime. This time-saving benefit directly contributes to increased production output and minimized disruptions in the manufacturing process.
Improved Product Quality: The use of rubber shock absorber joints contributes to the stable operation of injection molding machines, thereby positively influencing the precision and consistency of the manufactured products. Reduced machine vibrations and noise interference can result in improved product quality, with fewer defects and variations in the output.
In conclusion, the incorporation of rubber shock absorber joints in injection molding machines offers various time and effort-saving benefits. From simplified installation procedures to improved worker comfort and reduced maintenance downtime, these components play a pivotal role in enhancing the operational efficiency and productivity of injection molding processes. Ultimately, the utilization of rubber shock absorber joints contributes to a smoother and more reliable manufacturing environment for the production of high-quality molded products.
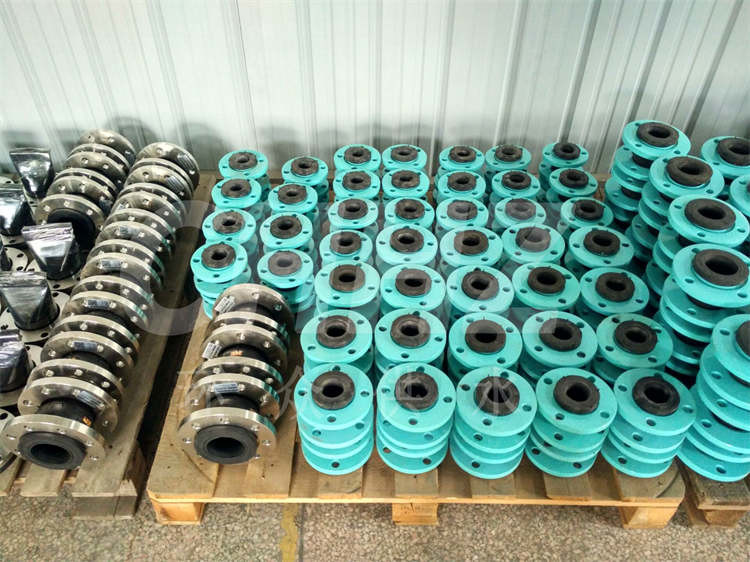