A Brief Overview of Flexible Rubber Joints: Classification and Applications
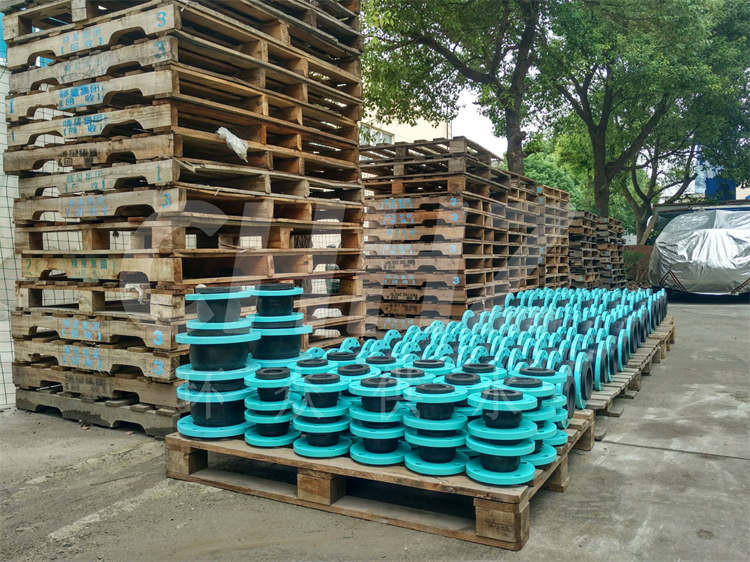
Flexible rubber joints play a crucial role in mitigating the effects of vibration, thermal expansion, and misalignment in piping systems across various industries. This article provides a concise introduction to the classification and applications of flexible rubber joints, highlighting their diverse types and functional advantages in industrial settings.
Introduction to Flexible Rubber Joints Flexible rubber joints, also known as flexible rubber connectors, are designed to absorb and compensate for movement, misalignment, and vibration in piping systems. Their flexibility and resilience make them indispensable in maintaining the integrity of pipelines, while also minimizing stress on adjacent equipment and structures.
Classification based on Configuration:Discuss the various types of flexible rubber joints based on their configuration, including:Straight Rubber Joints: Designed to accommodate axial, lateral, and angular movements in a single plane.Tapered Rubber Joints: Specifically engineered to handle larger movement capacities and provide enhanced flexibility in piping systems.Angular Rubber Joints: Suitable for applications that require significant angular movement compensation, such as in complex pipework layouts.
Classification based on Material:Explore the classification of flexible rubber joints based on their material composition, which may include:Neoprene Rubber Joints: Resistant to oils, chemicals, and weathering, making them ideal for diverse industrial environments.EPDM Rubber Joints: Capable of withstanding a wide range of temperatures and offering excellent ozone and chemical resistance.Nitrile Rubber Joints: Known for their resilience to oils, fuels, and abrasion, making them suitable for applications in petrochemical and automotive industries.
Application Areas:Highlight the broad spectrum of applications for flexible rubber joints, encompassing industries such as:HVAC Systems: Utilized for vibration isolation and movement absorption in heating, ventilation, and air conditioning ductwork.Water Treatment Plants: Deployed to compensate for thermal expansion and contraction in pipelines conveying water and wastewater.Industrial Process Piping: Essential for mitigating movement and vibration in chemical processing, power generation, and manufacturing facilities.
Functional Advantages:Emphasize the functional benefits of flexible rubber joints, including their ability to:Reduce stress on piping and equipment caused by vibration and movement.Provide a durable and cost-effective solution for compensating axial, lateral, and angular movement.Enhance system reliability and minimize the risk of pipeline failures due to mechanical stress.
In conclusion, flexible rubber joints offer a versatile and reliable solution for addressing movement, vibration, and misalignment issues in piping systems. Their diverse configurations and material compositions equip them to handle a wide range of industrial applications, contributing to the efficiency and longevity of critical infrastructure across multiple sectors.
In summary, flexible rubber joints constitute a fundamental component in the maintenance of industrial piping systems, offering tailored solutions to address specific movement and vibration challenges. Understanding the classification and applications of these joints is essential for engineers and maintenance professionals seeking to optimize the performance and longevity of piping systems in diverse industrial settings.
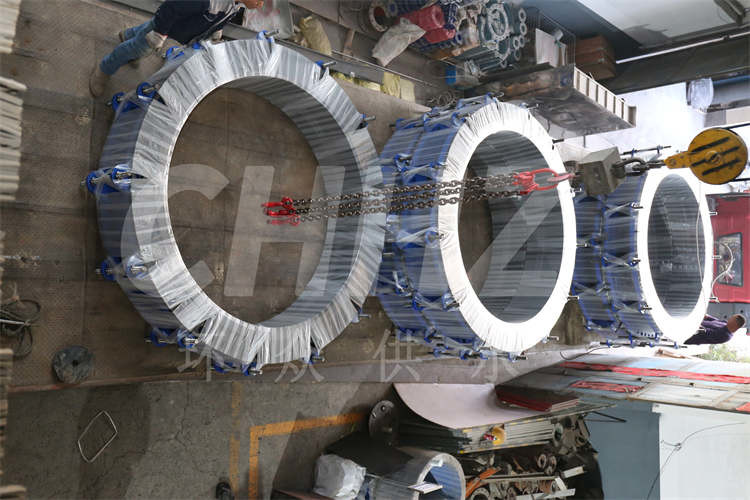