Rubber Flexible Joint Materials: A Comprehensive Overview
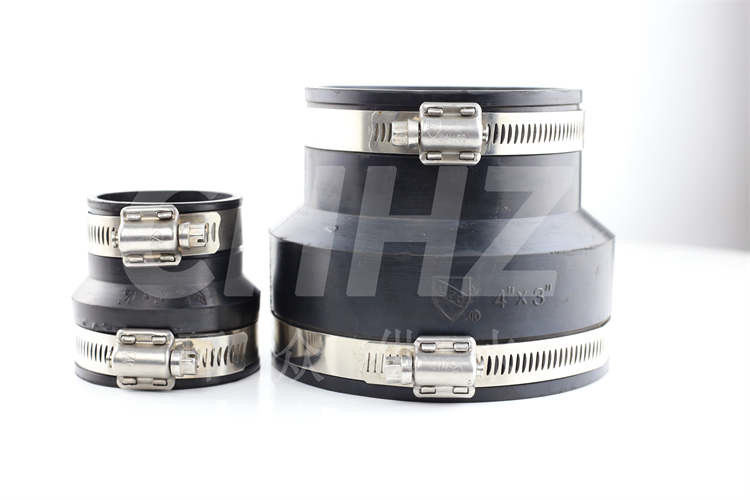
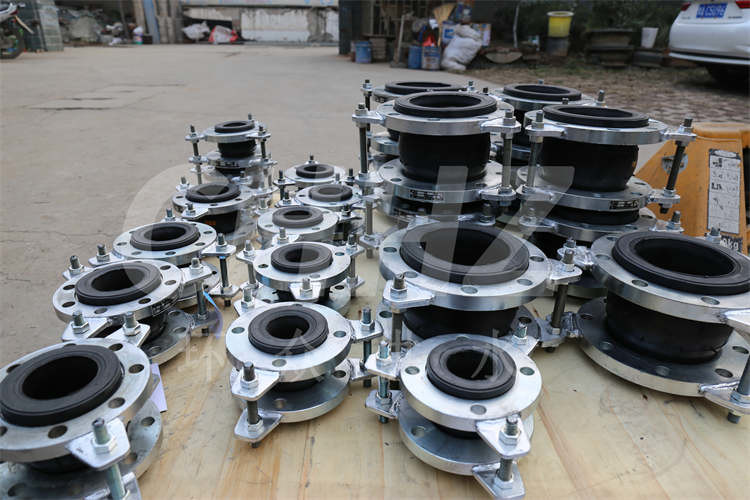
Rubber flexible joints are vital components in piping systems, providing flexibility and vibration isolation to accommodate thermal expansion, misalignment, and movement in various industrial applications. The choice of material for these joints plays a crucial role in determining their performance, longevity, and resistance to specific operating conditions. Here's a comprehensive overview of the different types of materials used in rubber flexible joints.
1. Natural Rubber (NR):Natural rubber is derived from the latex of rubber trees and exhibits excellent tensile strength, tear resistance, and flexibility. It is commonly used in applications where moderate chemical resistance, low temperatures, and good abrasion resistance are required. Natural rubber flexible joints are suitable for water, air, and low-concentration acid or alkali environments.
2. Neoprene (CR):Neoprene rubber is known for its remarkable resistance to weathering, ozone, and oil, making it well-suited for outdoor and marine applications. It also offers good flame resistance and performs well in moderate temperature ranges. Neoprene flexible joints are utilized in HVAC systems, refrigeration units, and outdoor piping installations.
3. Nitrile Rubber (NBR):Nitrile rubber is a synthetic rubber with excellent oil and fuel resistance, making it a popular choice for applications involving petroleum-based fluids. Its resilience to deformation and good adhesion properties make NBR flexible joints suitable for hydraulic systems, fuel lines, and oil transfer applications.
4. EPDM (Ethylene Propylene Diene Monomer):EPDM rubber offers superior resistance to heat, weathering, and ozone, along with excellent electrical insulating properties. It is widely employed in outdoor applications, water-based systems, and as a sealant in the automotive industry. EPDM flexible joints are preferred for hot and cold water piping, steam systems, and roofing applications.
5. Silicone Rubber:Silicone rubber exhibits exceptional resistance to extreme temperatures, UV radiation, and aging, making it a material of choice for high-temperature and sanitary applications. Its non-reactive nature and biocompatibility also extend its usage to pharmaceutical, food, and medical industries. Silicone flexible joints are utilized in food processing equipment, pharmaceutical systems, and high-temperature exhaust systems.
6. Fluoroelastomers (FKM):Fluoroelastomers offer exceptional chemical resistance, high-temperature stability, and resistance to fuels and oils, making them suitable for demanding industrial environments. FKM flexible joints find applications in aerospace, automotive, and chemical processing industries where exposure to aggressive fluids and elevated temperatures is prevalent.
In conclusion, the diverse range of materials used in rubber flexible joints provides engineers and designers with options to tailor the joint's performance to specific application requirements. Each material offers unique characteristics, allowing for the selection of the most suitable rubber flexible joint material based on factors such as chemical resistance, temperature range, flexibility, and environmental durability. Understanding the characteristics of each material is crucial in optimizing the performance and longevity of rubber flexible joints in various industrial settings.
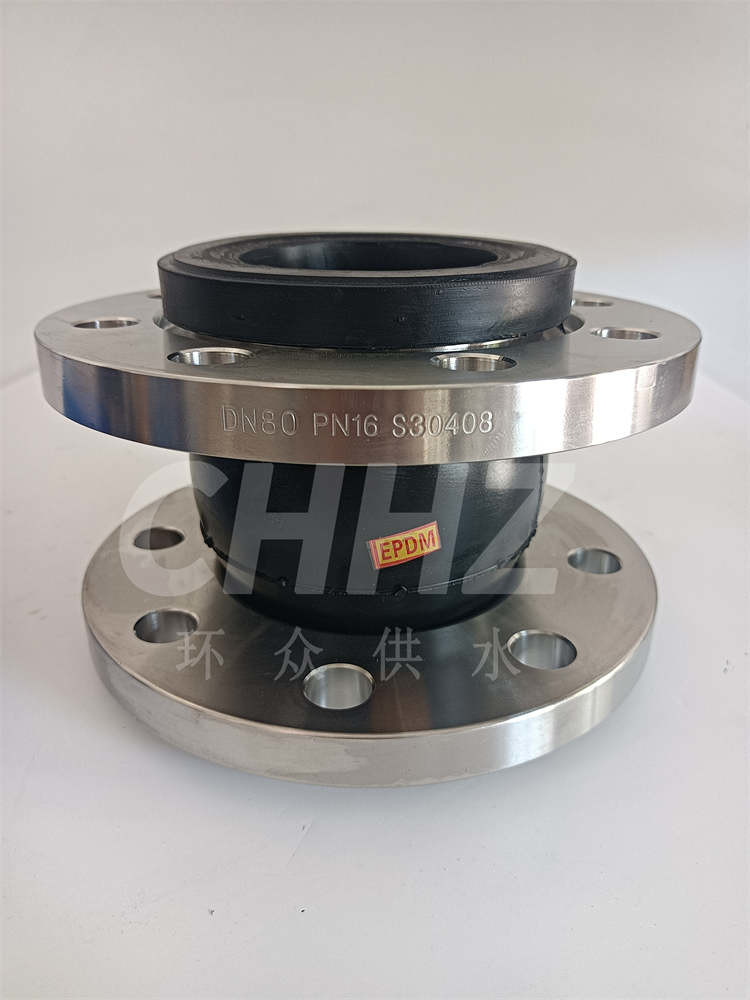