A groove rubber join
A groove rubber joint, also known as a grooved rubber expansion joint, is a vital component in pipeline systems for accommodating movement, dampening vibrations, and absorbing shocks. This article explores the application and advantages of grooved rubber joints in various industrial and commercial settings.
Introduction and Design:A grooved rubber joint is designed to provide flexibility and resilience in piping systems, where it is crucial to address the challenges of thermal expansion, contraction, and dynamic movement. The joint consists of a rubber sleeve with integrated grooves and flanges, allowing it to withstand axial, lateral, and angular movements while maintaining a sealed connection between pipeline components.
Function and Benefits:The primary function of a grooved rubber joint is to mitigate movement, absorb vibrations, and enhance the structural integrity of piping systems under varying operating conditions. By effectively accommodating thermal expansion and contraction, these joints reduce stress on pipelines and equipment, minimizing the risk of fatigue and failure. Additionally, their ability to absorb vibrations contributes to a quieter and more stable operation while extending the service life of the entire system.
Installation and Maintenance:Proper installation of grooved rubber joints involves precise alignment and secure fastening to ensure optimal performance and longevity. Regular inspections are essential to detect signs of wear, damage, or misalignment, facilitating timely repairs or replacements as needed. This proactive approach to maintenance helps prevent costly downtime and potential safety hazards associated with degraded or malfunctioning joints.
Application Considerations:Grooved rubber joints find extensive applications in industries such as water treatment facilities, HVAC systems, chemical processing plants, and power generation units. When selecting grooved joints for specific applications, factors such as pressure ratings, temperature range, chemical compatibility, and environmental conditions must be considered to ensure reliable performance and durability.
Advantages of Rubber Material:The use of rubber materials in grooved rubber joints offers multiple advantages, including excellent flexibility, chemical resistance, and sealing properties. Rubber joints are also known for their durability, cost-effectiveness, and ease of installation, making them a preferred choice in various piping systems where movement and vibrations need to be accommodated.
Types of Movement Absorption:Grooved rubber joints are designed to accommodate axial, lateral, and angular movements in piping systems, providing essential flexibility to handle the dynamic forces and thermal variations encountered during operation. The ability to address these types of movement effectively is critical for the reliable and uninterrupted performance of the entire pipeline network.
Safety and Compliance:Adherence to industry standards and safety guidelines is essential during the installation and operation of grooved rubber joints. Compliance with material specifications, pressure ratings, and performance criteria outlined in industry standards and regulatory guidelines is imperative to ensure the safety, efficiency, and environmental compliance of the piping system.
In conclusion, grooved rubber joints are indispensable components in pipeline systems, where they play a crucial role in accommodating movement, dampening vibrations, and enhancing the overall integrity and operational efficiency of the system. Proper selection, installation, and maintenance of these joints are vital to ensuring their effective and dependable performance across a diverse range of industrial and commercial applications.
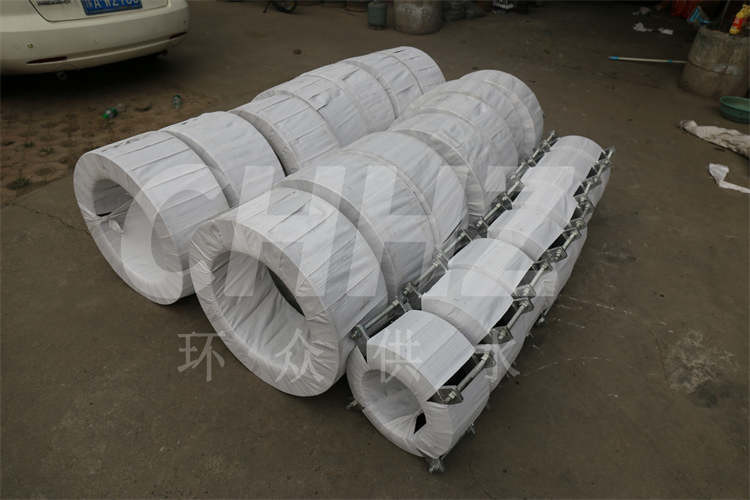