Rubber Expansion Joints: Finding the Best Fit for Your Needs
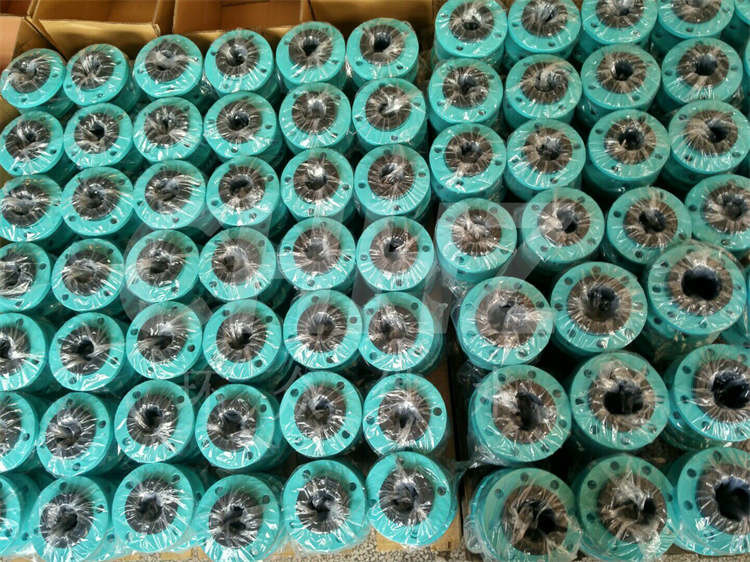
Rubber expansion joints, also known as rubber flexible connectors, are essential components in piping systems, offering critical flexibility and vibration isolation. When choosing the best rubber expansion joint for your application, several factors should be considered to ensure optimal performance, durability, and cost-effectiveness.
1. Material Quality:The quality of the rubber compound used in the expansion joint is crucial for its performance and longevity. High-quality elastomers, such as EPDM, neoprene, and natural rubber, offer excellent resistance to corrosion, abrasion, and environmental factors. EPDM rubber is known for its superior ozone and chemical resistance, making it suitable for a wide range of applications. Neoprene provides exceptional oil and heat resistance, ideal for demanding industrial environments. Assessing the material's compatibility with the media being conveyed and the surrounding environment is essential in selecting the most suitable rubber expansion joint.
2. Reinforcement and Construction:The reinforcement of the rubber expansion joint, typically achieved with synthetic textiles or metal wire, enhances its strength and pressure resistance. The construction of the joint, including the number of layers and the method of bonding, influences its capacity to withstand internal pressures and movements. Consideration of the joint's construction and reinforcement is crucial in ensuring it can withstand the operating conditions within the piping system.
3. Movement and Flexibility:The ability of the expansion joint to accommodate various forms of movement, including axial, lateral, and angular displacement, is a critical factor in its performance. The design and configuration of the joint, such as its corrugated or convoluted shape, dictate its flexibility and range of movement. Additionally, the presence of arches or molded spherical shapes contributes to the joint's ability to absorb vibrations and compensate for thermal expansion, making it essential to evaluate these design features based on the specific requirements of the piping system.
4. Temperature and Pressure Rating:Understanding the anticipated temperature and pressure conditions is vital when selecting a rubber expansion joint. Different rubber compounds and materials exhibit varying tolerance to extreme temperatures and pressure levels. It is imperative to match the joint's temperature and pressure rating with the expected operating conditions to ensure its reliability and longevity.
5. Industry Standards and Compliance:Compliance with industry standards and certifications, such as those from ASTM International, ANSI, or ISO, ensures that the rubber expansion joint meets the necessary quality and performance criteria. Additionally, adherence to specific standards relevant to the application, such as those for food-grade or pharmaceutical applications, is essential for regulatory compliance and safety.
In conclusion, the selection of the best rubber expansion joint depends on a thorough evaluation of material properties, reinforcement, flexibility, temperature and pressure rating, and industry compliance. By considering these factors, you can identify the most suitable rubber expansion joint that will deliver optimal performance, longevity, and cost-effectiveness for your specific piping system requirements.
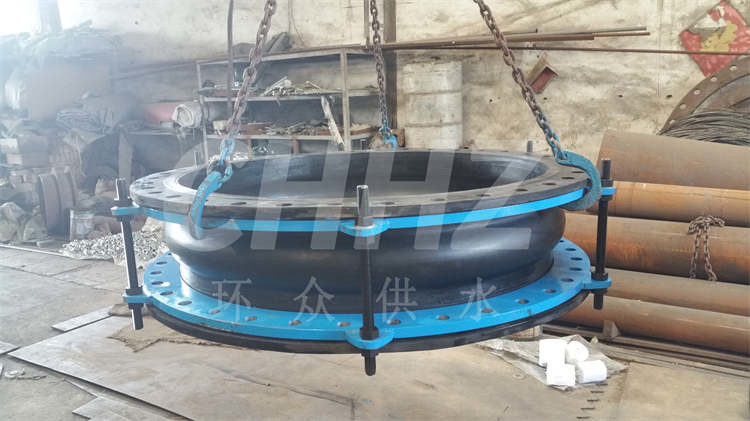