The Vulcanization Process for Rubber Gasket Joints
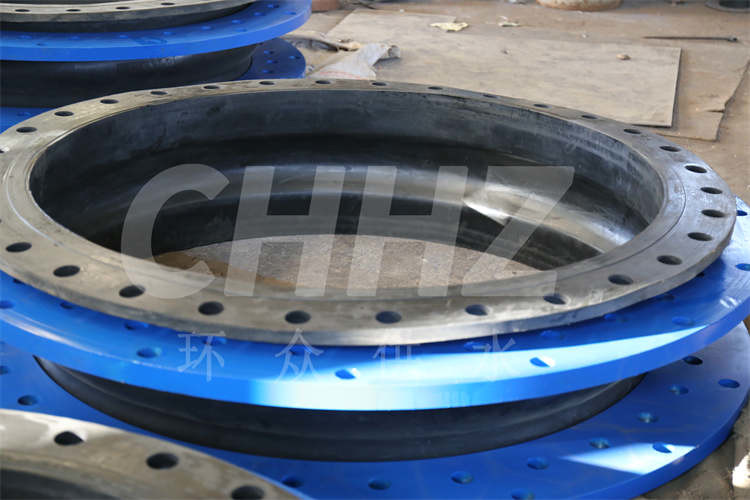
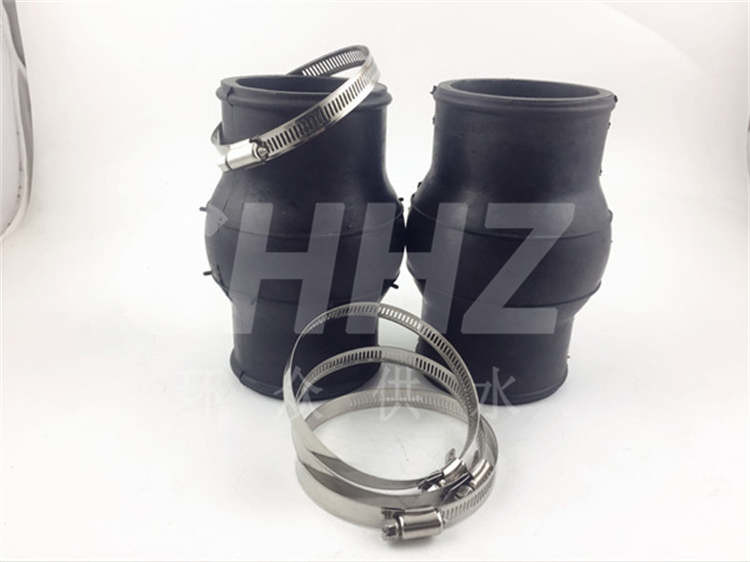
Vulcanization is a crucial process in the production of rubber gasket joints, and it plays a significant role in enhancing the durability, resilience, and performance of these essential components. This article provides an overview of the vulcanization process for rubber gasket joints, highlighting its importance in creating reliable and long-lasting sealing solutions for diverse industrial applications.
The vulcanization process involves the treatment of raw rubber or elastomers with sulfur or other cross-linking agents to improve their mechanical properties. For rubber gasket joints, this process is fundamental in transforming the raw material into a resilient and chemically stable material that can effectively withstand the demands of sealing applications.
The process begins with the preparation of the rubber compound, which typically includes the raw rubber material, fillers, curing agents, and other additives. The compound is thoroughly mixed to ensure uniform distribution of ingredients, followed by shaping or molding to achieve the desired form and dimensions of the gasket joint. Once the rubber compound is shaped, the vulcanization process takes place to impart the necessary properties.
During vulcanization, the shaped rubber gasket joints are exposed to elevated temperatures, typically in the presence of sulfur or sulfur-bearing compounds. This triggers a chemical reaction that forms cross-links between the polymer chains, resulting in a three-dimensional network structure within the rubber material. As a result, the rubber gasket joint undergoes significant changes, including increased elasticity, tensile strength, and resistance to abrasion, heat, and chemicals.
The duration and temperature of the vulcanization process are carefully controlled to achieve the desired balance of physical properties in the rubber gasket joint. Once the vulcanization is completed, the gasket joints undergo post-curing processes to further enhance their mechanical properties and stability.
The benefits of vulcanization in the production of rubber gasket joints are manifold. The cross-linking of polymer chains significantly improves the resistance of the material to deformation, aging, and environmental factors, making it well-suited for sealing applications in demanding industrial environments. Additionally, vulcanized rubber gasket joints exhibit superior compressibility and elastic recovery, ensuring effective sealing under varying loads and conditions.
In conclusion, the vulcanization process is integral to the production of high-quality rubber gasket joints. By imparting key mechanical and chemical properties to the rubber material, vulcanization contributes to the reliability, durability, and performance of gasket joints in diverse applications, ranging from plumbing systems to industrial machinery. As advancements in materials science and manufacturing technologies continue, the vulcanization process is expected to play an ongoing role in producing innovative and dependable rubber gasket joints for evolving industrial needs.
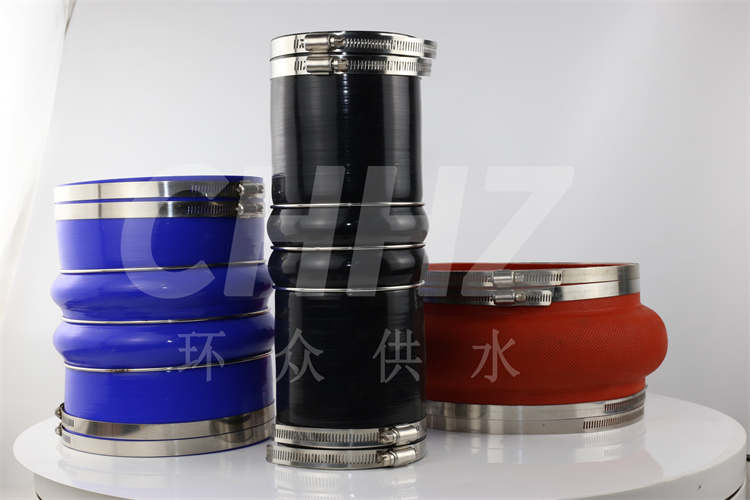