Rubber joint wear
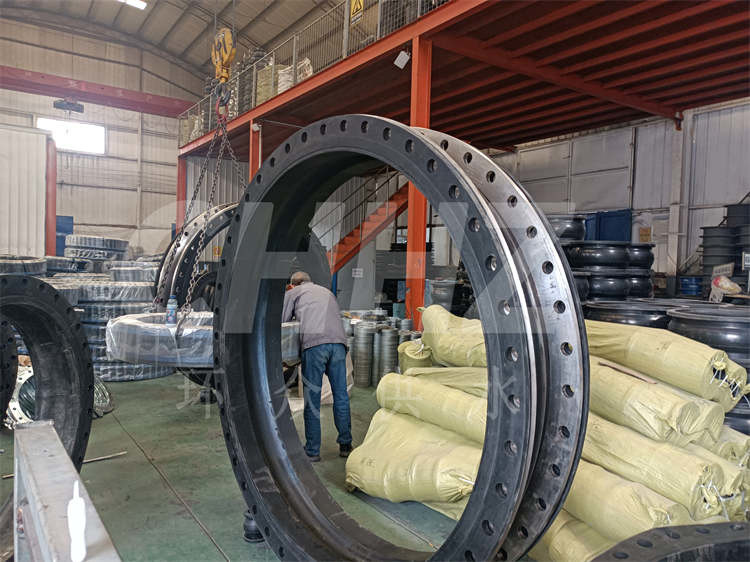
Rubber joint wear is a common issue encountered in industrial systems where flexibility, vibration isolation, and movement compensation are required. This article discusses the factors contributing to rubber joint wear and methods to mitigate its effects.
Rubber joints, also known as expansion joints, are critical components used in piping systems to absorb movement, dampen vibration, and compensate for thermal expansion and contraction. However, over time, these joints may experience wear due to various factors.
One primary contributor to rubber joint wear is the exposure to abrasive media or harsh chemicals. The continuous flow of abrasive materials through the piping system can lead to erosion and degradation of rubber surfaces. Additionally, exposure to chemicals, such as acids or alkalis, can accelerate the deterioration of the rubber material, causing it to weaken and lose its flexibility.
Furthermore, excessive movement and misalignment within the system can cause stress on the rubber joints, leading to wear and fatigue. Inadequate support or improper installation can result in excessive stretching, bending, or torsion of the joints, accelerating their wear and reducing their functionality.
Another factor influencing rubber joint wear is the operating temperature. Extreme temperatures can affect the resilience and elasticity of the rubber material, leading to hardening and eventual cracking or failure of the joints.
To address and prevent rubber joint wear, several measures can be implemented. Choosing a high-quality rubber material with superior resistance to abrasion and chemicals can significantly extend the service life of the joints. Moreover, routine inspection and maintenance are crucial to identify signs of wear and address them before they become critical issues.
Proper system design and installation, including the correct selection of joint type, size, and placement, can help minimize excessive movement and stress on the joints, thereby reducing wear and prolonging their lifespan.
Additionally, implementing protective measures such as liners or coatings to mitigate the impact of abrasive media can help preserve the integrity of the rubber joints. Furthermore, selecting expansion joints with suitable temperature ratings that align with the operating conditions is essential in preventing premature wear due to temperature extremes.
In conclusion, rubber joint wear is a common concern in industrial piping systems, arising from factors such as abrasive media, chemical exposure, excessive movement, and temperature extremes. Through careful material selection, proper installation, and regular maintenance, the detrimental effects of wear on rubber joints can be mitigated, ensuring the longevity and reliability of these critical components in industrial applications.
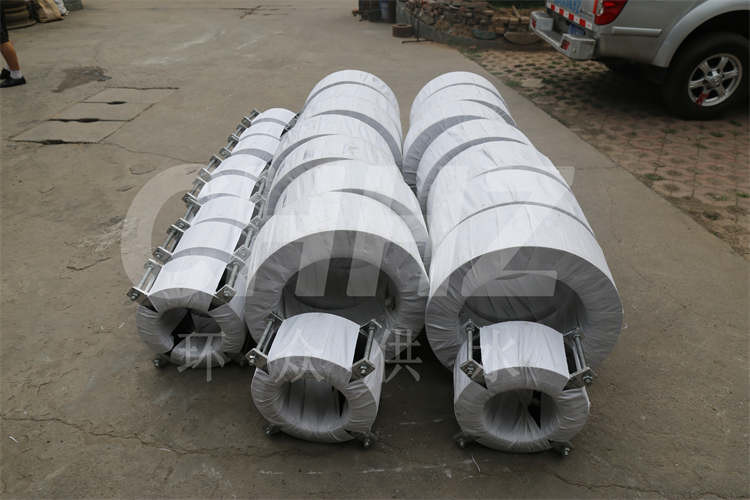