Rubber Expansion Joints: Enhancing Flexibility and Reliability
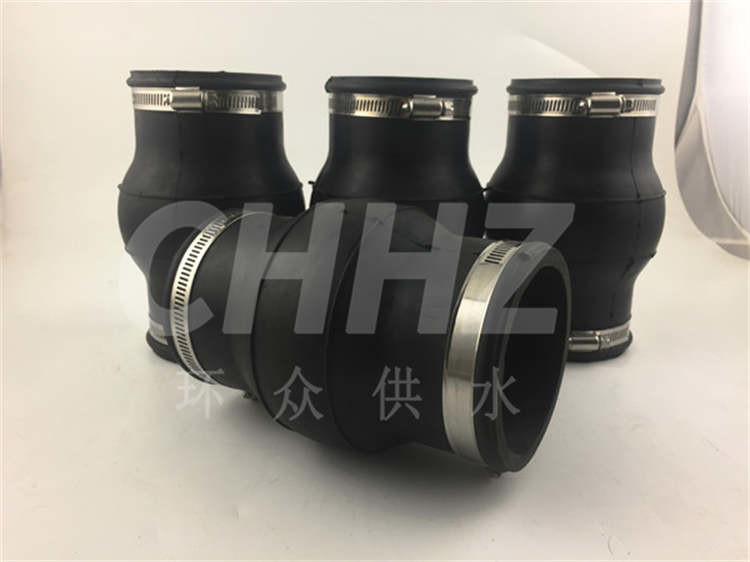
In various industrial and mechanical systems, the utilization of rubber expansion joints plays a critical role in mitigating the effects of thermal expansion, vibration, and misalignment. These components are designed to accommodate movement and provide flexibility within piping and ducting systems while effectively reducing stress on interconnected equipment.
Rubber expansion joints, also known as flexible connectors, are engineered using durable elastomeric materials such as natural rubber, EPDM, neoprene, or silicone. These materials possess excellent elasticity and resilience, allowing the expansion joints to absorb movements and vibrations within the system, thus preventing potential damage to piping and associated equipment.
One of the primary functions of rubber expansion joints is to compensate for thermal expansion and contraction in piping systems, particularly in high-temperature environments. When exposed to fluctuating temperatures, pipelines and ducts undergo dimensional changes, and the inclusion of expansion joints helps to mitigate the resulting stress and displacement, thereby extending the service life of the overall infrastructure.
Moreover, rubber expansion joints effectively dampen vibration and noise, making them valuable components in systems where noise reduction and machinery protection are essential. By isolating vibrations and shocks, these joints contribute to the longevity and reliability of interconnected equipment and structures.
In addition to their mechanical benefits, rubber expansion joints offer superior chemical resistance, making them suitable for a wide range of industrial applications where exposure to corrosive substances is a concern. The elastomeric nature of the rubber material allows the expansion joints to withstand various chemicals and aggressive fluids, thus enhancing the overall durability and reliability of the system.
Proper installation and maintenance are paramount to ensuring the optimal performance and longevity of rubber expansion joints. Regular inspection and replacement of worn or damaged expansion joints are essential to maintaining the integrity of the system and preventing potential leaks or failures.
The design and engineering of rubber expansion joints encompass various factors, including pressure rating, movement capability, and environmental considerations. Manufacturers adhere to industry standards and specifications to ensure that the expansion joints meet or exceed the performance requirements for specific applications.
In summary, rubber expansion joints play a crucial role in enhancing the flexibility, reliability, and longevity of piping and ducting systems across a wide range of industrial sectors. By incorporating these components, engineers and facility operators can effectively manage thermal expansion, vibration, and misalignment, thereby contributing to the overall efficiency and safety of the infrastructure. With their unique ability to accommodate movements and absorb stresses, rubber expansion joints continue to be integral components in modern industrial applications.
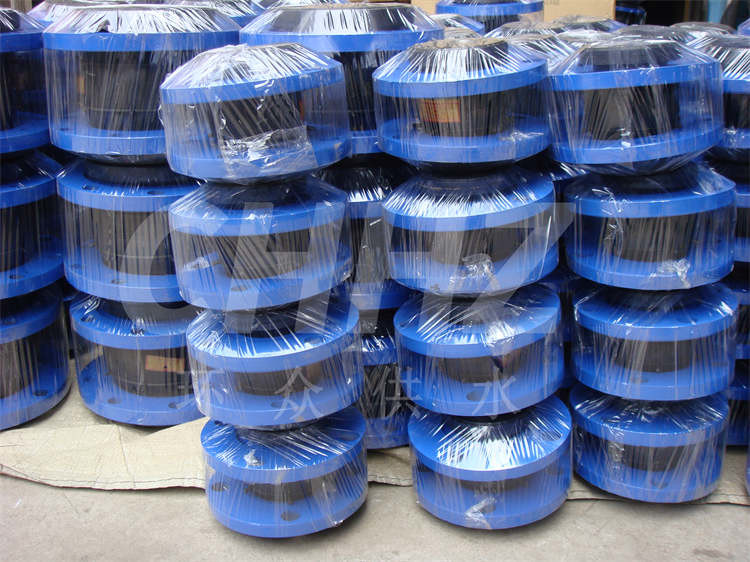