Rubber Joint Model
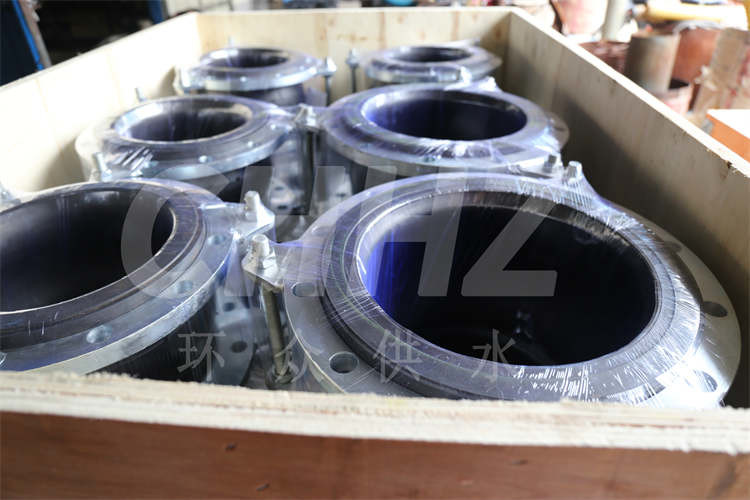
Rubber joints, also known as rubber expansion joints, play a critical role in various industries, providing flexibility and vibration isolation in piping systems. These components are designed to absorb movement, compensate for misalignment, and reduce stress on pipelines, thereby extending the life of the entire system. Engineers and designers utilize rubber joint models to simulate the behavior of these components under different operating conditions and to ensure their effectiveness in maintaining the integrity of the piping network.
Modeling Techniques:The process of modeling rubber joints involves employing various techniques to capture their material behavior, structural response, and performance characteristics. Finite Element Analysis (FEA) is commonly used to simulate the elastic properties of rubber materials, as well as the interaction between the joints and the surrounding piping. By defining the geometry, material properties, and boundary conditions, engineers can analyze the deflection, stress distribution, and reaction forces within the joint.
Material Properties:Accurately representing the material properties of rubber in the model is crucial for predicting the mechanical behavior of the joints. Parameters such as elasticity, hysteresis, and fatigue properties are considered to simulate the stress-strain response under different loading scenarios. Dynamic material models, such as the Mooney-Rivlin or Ogden models, are often utilized to capture the non-linear behavior of rubber materials under compression, extension, and shear.
Load Analysis:Rubber joint models are subjected to various loading conditions to evaluate their performance in real-world applications. The models are analyzed for their ability to withstand pressure, temperature variations, and dynamic forces induced by fluid flow or mechanical vibrations. By incorporating these loading conditions into the simulation, engineers can assess the durability, fatigue resistance, and overall reliability of the rubber joints.
Deflection and Stress Analysis:The behavior of rubber joints under deflection and stress is a critical aspect of the modeling process. By analyzing the joint's response to axial, lateral, and angular movements, engineers can evaluate its ability to accommodate thermal expansion, seismic disturbances, and operational displacements. Stress analysis helps identify potential areas of high stress concentration and deformation, aiding in the design optimization of the joints.
Validation and Optimization:Once the rubber joint model is developed, it undergoes validation through comparison with physical testing results or field data. This iterative process allows engineers to refine the model parameters, boundary conditions, and material properties to achieve better correlation with real-world behavior. The validated model can then be used to optimize the design of rubber joints for specific applications, considering factors such as size, shape, reinforcement, and installation requirements.
In summary, the use of rubber joint models enables engineers to predict the performance and behavior of these critical components in piping systems. Through accurate representation of material properties, comprehensive load analysis, and validation against actual performance, the modeling process contributes to the efficient design and utilization of rubber joints in diverse industrial settings.
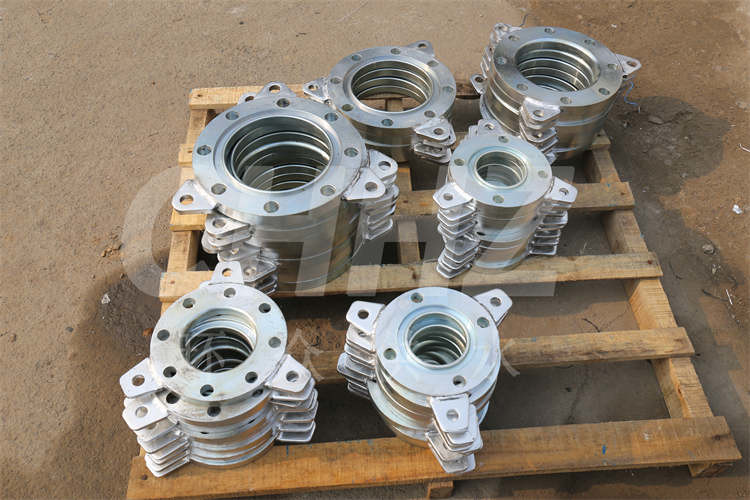