Rubber Joints in Automotive Applications
Rubber joints play a critical role in automotive systems, providing flexibility, vibration isolation, and resistance to movement and misalignment. These components are utilized in various parts of a vehicle to minimize stress and ensure smooth operation. In this article, we will discuss the importance and applications of rubber joints in automotive engineering.
1. Exhaust System:Rubber joints are commonly employed in the exhaust system to absorb vibrations and movements generated by the engine and the road. They are often integrated into the exhaust pipe connections, helping to minimize noise, vibration, and harshness (NVH) in the vehicle. The flexibility and damping properties of rubber joints contribute to improved ride comfort and reduced stress on the exhaust system components.
2. Suspension System:In the suspension system, rubber joints are utilized to connect various components, such as control arms, stabilizer bars, and subframes. These joints enable articulation and flexibility while maintaining structural integrity. By absorbing shocks and vibrations, rubber joints contribute to the overall stability and comfort of the vehicle, enhancing its handling and ride quality.
3. Drivetrain:Rubber joints are essential in the drivetrain to accommodate angular misalignment and axial movement between the engine, transmission, and wheels. Constant velocity (CV) joints, which employ rubber boots to enclose the joint and protect it from contaminants, are a common example in this application. The flexibility and resilience of rubber joints contribute to smooth power transmission and prolonged component life in the drivetrain.
4. Engine Mounts:Rubber isolation mounts are used to secure the engine to the vehicle's body or frame. These mounts serve two primary purposes: they dampen engine vibrations and help isolate the cabin from the engine's noise and harshness. By mitigating the transmission of engine vibrations, rubber mounts contribute to a quieter and more comfortable driving experience.
5. Fluid Handling Systems:Rubber joints also find application in various fluid handling systems within the vehicle, including fuel lines, coolant hoses, and power steering assemblies. These joints provide flexibility to accommodate engine movement and thermal expansion, while effectively sealing and containing fluids. The resilience and chemical resistance of rubber joints are crucial in maintaining the integrity and reliability of these critical automotive systems.
In conclusion, rubber joints are integral components within automotive engineering, contributing to vehicle performance, comfort, and reliability. Their ability to absorb vibrations, accommodate movement, and provide isolation in diverse applications within the vehicle is essential for maintaining overall functionality and passenger comfort. As automotive technology continues to advance, the demand for high-performance rubber joints that can meet stringent requirements for durability, safety, and NVH will remain a key focus for vehicle manufacturers and suppliers.
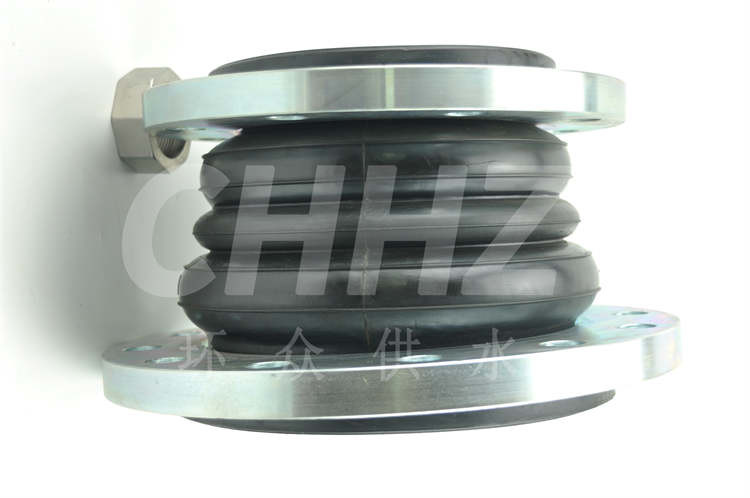