Processing of Large Flanged Rubber Joints
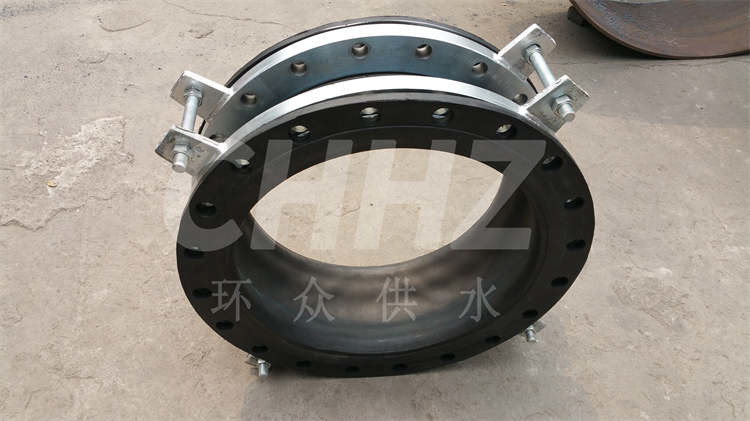
Large flanged rubber joints are crucial components used in various industrial piping systems to absorb movement, compensate for misalignment, and reduce noise and vibration. The manufacturing process for these joints involves several key steps to ensure their quality, performance, and durability in demanding applications.
Material Selection: The production of large flanged rubber joints begins with the careful selection of high-quality elastomeric materials such as natural rubber, neoprene, EPDM, or viton. These materials are chosen for their resilience, chemical resistance, and ability to withstand pressure and temperature fluctuations in diverse operating conditions.
Mold Design and Fabrication: The next step involves the design and fabrication of molds that will be used to shape the rubber components. Precise molds are essential to ensure the accurate formation of the flanged joints, including the size, shape, and placement of the flanges, as well as the overall dimensions of the joint.
Rubber Compounding and Mixing: Once the molds are ready, the rubber compound is prepared by blending the selected elastomeric material with other additives such as curing agents, accelerators, and reinforcing fillers. This process is crucial to achieve the desired physical properties, such as tensile strength, flexibility, and resistance to chemicals and abrasion.
Molding and Vulcanization: The rubber compound is then introduced into the molds and subjected to heat and pressure in a vulcanization process. This process cures the rubber, forming the characteristic properties of the flanged joints, including their elasticity, resilience, and resistance to deformation under operating conditions.
Flange Attachment: After the rubber components are molded and vulcanized, the next step involves attaching the metal flanges to the joints. This is typically achieved through a combination of mechanical bonding and vulcanization, ensuring a strong and secure connection between the rubber and the flanges.
Quality Control and Testing: Throughout the manufacturing process, rigorous quality control measures are implemented to verify the dimensions, material properties, and integrity of the large flanged rubber joints. Additionally, the finished joints undergo testing to assess their performance under pressure, movement, and temperature variations, as well as their ability to withstand vibrations and noise.
Surface Treatment and Finishing: Finally, the surface of the flanged rubber joints is treated to enhance their resistance to environmental factors, such as moisture, UV radiation, and chemical exposure. This may involve the application of protective coatings or surface treatments to prolong the service life of the joints in challenging industrial environments.
In conclusion, the processing of large flanged rubber joints involves a series of critical steps, including material selection, mold design and fabrication, rubber compounding and mixing, molding and vulcanization, flange attachment, quality control and testing, as well as surface treatment and finishing. These steps are essential to ensure the reliability, functionality, and durability of the joints in industrial piping applications.
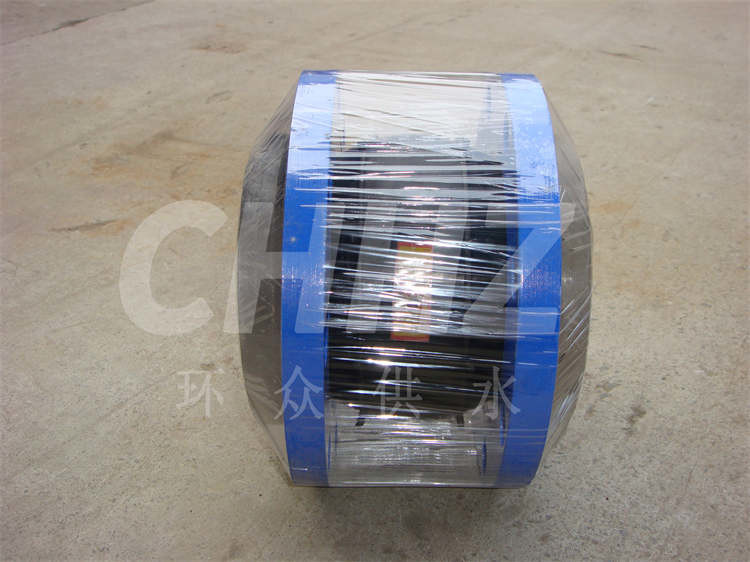