Rubber Joint Processing Equipment
Rubber joints are essential components used in various industries and applications such as pipeline systems, industrial machinery, and HVAC systems. The efficient production of high-quality rubber joints relies on a range of specialized processing equipment. This article explores the key types of equipment used in the manufacturing and processing of rubber joints, emphasizing their significance and impact on the industry.
Mixing Equipment: One of the initial stages in rubber joint production involves the mixing of raw rubber compounds with various additives and materials. The mixing equipment, such as internal mixers or open mill mixing machines, is crucial for achieving a homogeneous blend of rubber and other components. These machines ensure uniform dispersion of ingredients, leading to consistent physical properties and improved processability of the rubber compounds.
Molding and Extrusion Machines: Molding and extrusion are fundamental processes in shaping raw rubber compounds into the desired forms of rubber joints. Injection molding machines, compression molding presses, and rubber extruders play a vital role in forming the rubber into specific shapes and dimensions. These machines provide the capability to produce various types of rubber joints, including straight connectors, angles, T-shapes, and custom-designed profiles, meeting diverse application requirements.
Vulcanization Equipment: Vulcanization is a critical step that imparts the necessary mechanical strength, elasticity, and heat resistance to the rubber joints. Autoclaves, vulcanizing presses, and continuous vulcanization lines are used for curing the molded or extruded rubber components. These machines subject the rubber joints to controlled heat and pressure, initiating the cross-linking of polymer chains and the formation of a stable network structure, resulting in the desired mechanical and thermal properties.
Cutting and Trimming Machinery: After vulcanization, rubber joints often undergo further processing to achieve precise dimensions and surface finishes. Cutting machines, such as water jet cutters, laser cutters, or die-cutting presses, are employed to trim excess material and achieve specific geometries. Trimming equipment ensures the accurate and uniform dimensions of the rubber joints while minimizing material waste and enhancing the overall quality of the finished products.
Testing and Inspection Systems: Quality control is integral to the production of rubber joints, and testing and inspection equipment play a crucial role in ensuring compliance with industry standards and specifications. These systems include hardness testers, dimensional inspection equipment, and various non-destructive testing methods to evaluate the physical properties, dimensions, and performance characteristics of rubber joints, providing assurance of their quality and reliability.
In conclusion, the efficient and precise manufacturing of rubber joints is reliant on a diverse range of processing equipment that encompasses mixing, molding, vulcanization, cutting, and testing aspects. The proper selection and utilization of these specialized machines are essential in achieving consistent product quality, meeting the demands of diverse applications, and contributing to the overall efficiency and advancement of the rubber joint industry. Embracing technological advancements in processing equipment is an imperative strategy for enhancing productivity, product innovation, and the competitiveness of manufacturers in the dynamic and evolving landscape of rubber joint production.
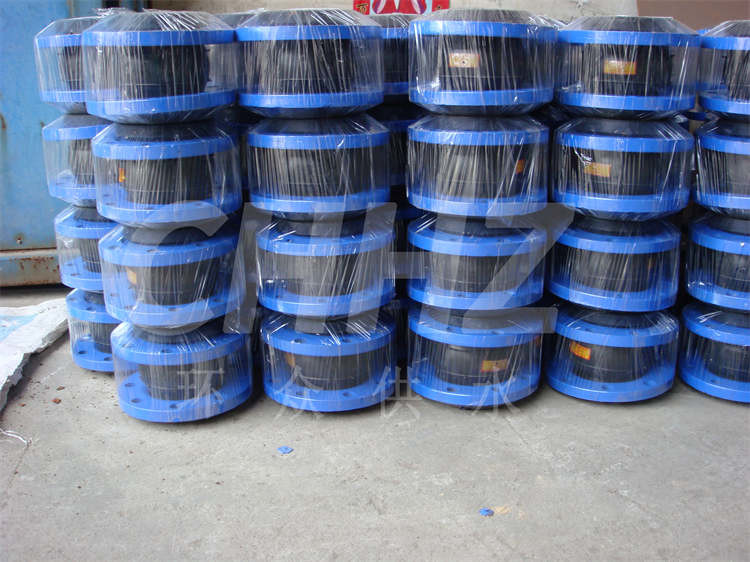