Fiberglass Reinforced Plastic (FRP) Rubber Joints
Introduction: Fiberglass reinforced plastic (FRP) rubber joints are essential components used in various industries due to their ability to absorb vibrations, compensate for misalignments, and reduce noise in piping systems. This article provides an insight into the key aspects of FRP rubber joints, including their applications, construction, advantages, and installation considerations.
Section 1: Application FRP rubber joints find application in diverse industries such as chemical processing, power generation, water treatment, and marine engineering. They are used to absorb movement within pipework, compensate for thermal expansion or contraction, and dampen vibrations, thereby extending the service life of piping systems and equipment.
Section 2: Construction FRP rubber joints are typically constructed using a combination of high-quality rubber compounds and layers of fiberglass reinforcement. The rubber component provides flexibility and elasticity, while the embedded fiberglass layers offer strength and resistance to pressure, ensuring the joint's ability to withstand harsh operating conditions.
Section 3: Advantages The combination of rubber and fiberglass in FRP rubber joints provides several advantages, including resistance to corrosion, chemicals, and high temperatures. Additionally, they offer low installation and maintenance costs, excellent noise and vibration reduction, and the ability to accommodate movement and misalignment within piping systems.
Section 4: Installation Considerations Proper installation of FRP rubber joints is crucial for their effective performance. It involves ensuring correct alignment, securely connecting the joints to the pipeline using compatible fastening methods, and considering factors such as the operating temperature, pressure, and media to maintain the joint's integrity and functionality.
Section 5: Maintenance and Service Life Regular inspection and maintenance are essential to enhance the service life of FRP rubber joints. This includes checking for signs of wear, degradation, or damage, as well as ensuring proper anchoring and support to prevent excessive stress on the joints. Following manufacturer recommendations for maintenance intervals is critical to ensure optimal performance.
Section 6: Environmental Considerations FRP rubber joints are engineered to withstand a range of environmental conditions, including exposure to UV radiation, harsh chemicals, and varying temperatures. Proper insulation and protective coatings can further enhance their durability in challenging environments.
Conclusion: In conclusion, FRP rubber joints play a vital role in maintaining the integrity and functionality of piping systems across numerous industries. Understanding their applications, construction, advantages, installation considerations, and maintenance requirements is essential to maximize their performance and contribute to the overall operational reliability of industrial facilities.
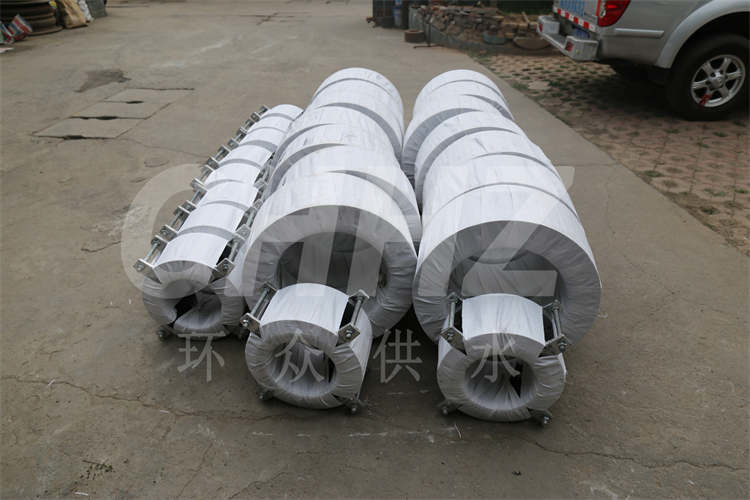