How to Manufacture Rubber Flexible Joints
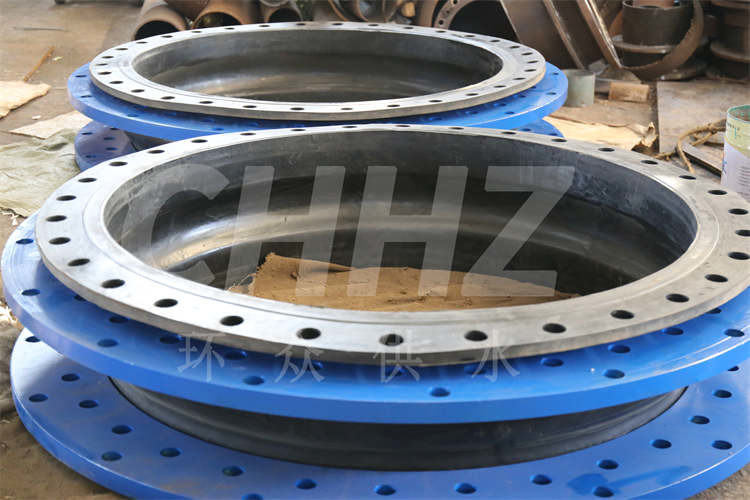
Rubber flexible joints, also known as rubber expansion joints, are essential components in piping systems as they absorb movement, vibration, and noise. Here's a detailed process on how rubber flexible joints are manufactured.
Material Selection: The manufacturing process of rubber flexible joints begins with the selection of high-quality rubber materials. Natural rubber or synthetic rubber compounds with excellent mechanical properties and chemical resistance are often chosen for this application.
Molding: The selected rubber compound is then placed into a mold that is designed to form the desired shape of the flexible joint. The molding process involves the application of heat and pressure to vulcanize the rubber, giving it the necessary strength and elasticity.
Reinforcement: In some cases, the rubber may be reinforced with internal layers of fabric or metal to enhance its structural integrity and resistance to pressure and movement. This reinforcement helps to prevent the rubber from overstretching or being damaged under extreme conditions.
End Fitting Installation: Once the rubber component is formed, it is fitted with end connections, such as flanges or threaded inserts, that allow the flexible joint to be installed within a piping system. The end fittings are securely bonded or mechanically attached to the rubber to ensure a leak-tight and durable joint.
Surface Treatment: Surface treatments, such as coating the rubber with protective compounds or applying anti-corrosive coatings to the metal parts, may be carried out to enhance the joint's performance and longevity in diverse operating environments.
Quality Control: Throughout the manufacturing process, rigorous quality control measures are implemented to verify the dimensions, material properties, and structural integrity of the rubber flexible joints. This ensures that the final products meet the required industry standards and performance specifications.
Testing: Before the rubber flexible joints are released for commercial use, they undergo comprehensive testing to evaluate their ability to withstand pressure, movement, and temperature variations. These tests help to verify the joints' reliability and safety in real-world applications.
In conclusion, producing rubber flexible joints involves precision molding, material reinforcement, fitting installation, and stringent quality control measures. The careful selection of materials and close attention to manufacturing details are critical in ensuring that the final products meet the stringent performance requirements of various industrial and mechanical systems.
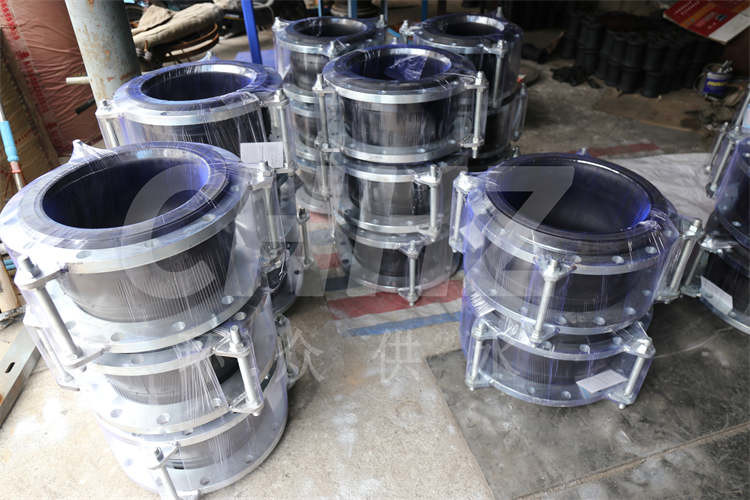