Designing a rubber joint vulcanization mold
Designing a rubber joint vulcanization mold is a critical process that requires careful consideration of various factors to ensure the production of high-quality rubber joints with consistent properties and performance. In this article, we will discuss the key aspects involved in the design of a rubber joint vulcanization mold, outlining the necessary steps and considerations to achieve optimal results.
The design process for a rubber joint vulcanization mold begins with a comprehensive understanding of the desired specifications and requirements for the final product. This involves defining the dimensions, shape, and material properties of the rubber joint, as well as identifying any specific features or surface textures that need to be replicated in the mold.
Once the design specifications are established, the next step involves creating a detailed 3D model of the rubber joint and the corresponding mold cavity. This model serves as the blueprint for the mold design and allows for the visualization and analysis of critical aspects such as parting line location, draft angles, and gating and venting systems. The 3D model also facilitates virtual testing and validation of the mold design before physical prototyping.
One of the key considerations in mold design is the selection of appropriate materials. The mold material must possess the necessary thermal conductivity, mechanical strength, and surface finish characteristics to ensure uniform heat distribution and effective demolding of the rubber joint. Additionally, the mold material should be resistant to the chemical and thermal effects of the vulcanization process to maintain its integrity over multiple production cycles.
Incorporating an efficient cooling system into the mold design is essential for controlling the temperature distribution during the vulcanization process. Proper cooling ensures uniform curing of the rubber material, minimizes cycle times, and reduces the risk of thermal degradation or inconsistencies in the final product. The cooling channels should be strategically positioned to optimize heat transfer and minimize energy consumption.
The mold design also encompasses the layout and configuration of the sprue, runners, and gates, which are integral to the flow of rubber material into the cavity and the subsequent air evacuation. A well-designed gating system facilitates uniform filling of the mold cavity, minimizes material waste, and prevents defects such as air entrapment and uneven cure.
Furthermore, the demolding mechanism and surface treatment of the mold are critical aspects of the design process. The demolding mechanism should be designed to facilitate the easy and safe removal of the rubber joint from the mold while minimizing the risk of damage or distortion. Surface treatments such as coatings or textures can be applied to the mold to impart specific surface finishes or release properties to the finished rubber joint.
In conclusion, designing a rubber joint vulcanization mold involves a meticulous and multidisciplinary approach that encompasses material selection, cooling system design, gating configuration, demolding mechanisms, and surface treatments. By addressing these key aspects in the design process, manufacturers can achieve consistent and high-quality production of rubber joints, meeting the demands of diverse industrial applications.
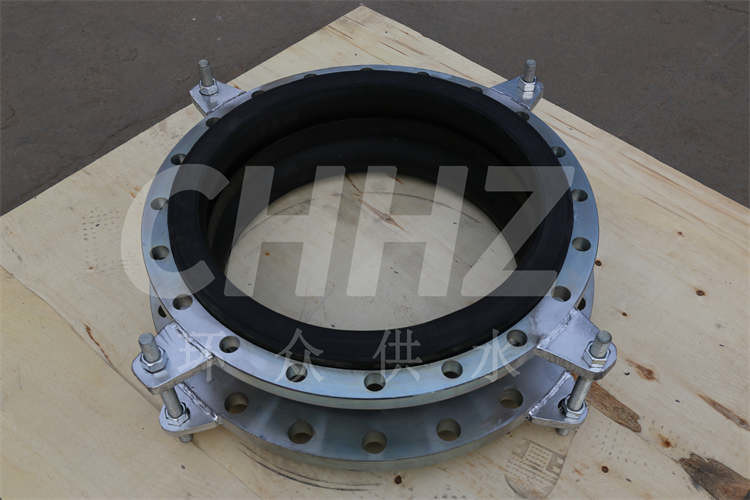