Rubber Sealing Joint Molds: Ensuring Precision and Quality in Sealing Solutions
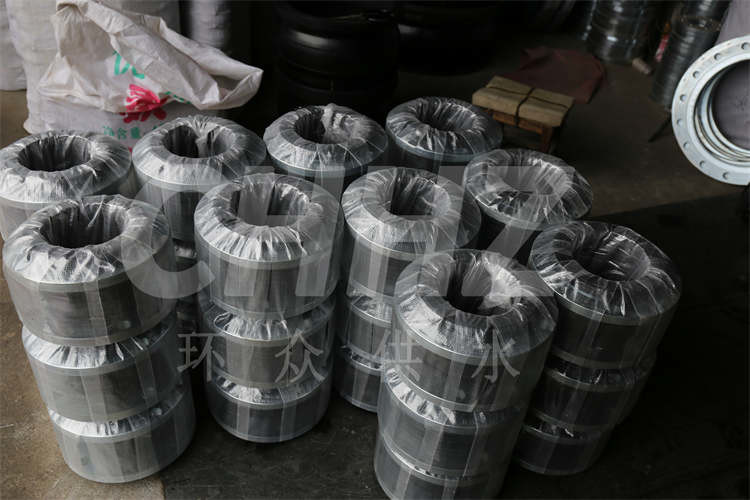
Rubber sealing joint molds play a pivotal role in the manufacturing process of rubber seals and joints. These molds are essential tools used to create precision-engineered rubber seal components for a wide range of applications in industries such as automotive, aerospace, construction, and machinery. By leveraging advanced mold design and manufacturing techniques, rubber sealing joint molds contribute to the production of high-quality, durable, and reliable sealing solutions.
Mold Design and Precision Engineering: The design of rubber sealing joint molds involves intricate engineering to ensure that the final product meets specific dimensional and performance requirements. Advanced computer-aided design (CAD) and computer-aided manufacturing (CAM) technologies are employed to create intricate mold designs with precise specifications. These molds are strategically crafted to produce rubber seals and joints that fit seamlessly into their intended applications, providing effective sealing and protection against environmental factors such as moisture, dust, and temperature variations.
Material Selection and Mold Construction: The choice of materials for rubber sealing joint molds is critical in determining the quality and durability of the produced seals. High-grade tool steels and alloys are commonly used in the construction of molds to withstand the rigors of high-pressure rubber molding processes. Additionally, sophisticated surface treatment methods, such as nitriding or coating with advanced wear-resistant materials, are employed to enhance the longevity and performance of the molds, ensuring consistent and high-quality seal production over extended periods.
Precision in Manufacturing Processes: During the manufacturing of rubber sealing joint molds, precision machining techniques such as CNC milling, turning, and grinding are employed to create mold cavities with exceptional accuracy and surface finish. The use of cutting-edge manufacturing technologies and equipment allows for the production of intricately detailed mold components, resulting in rubber seals and joints that meet tight tolerance requirements and exhibit uniform precision across large production batches.
Quality Control and Assurance: Stringent quality control measures are implemented throughout the mold manufacturing process to ensure the reliability and consistency of the produced rubber seals and joints. Advanced metrology and inspection equipment are utilized to verify the dimensional accuracy of mold cavities, confirming adherence to design specifications. Furthermore, comprehensive testing protocols are employed to validate the molds' ability to withstand the demands of rubber molding processes while maintaining precise replication of sealing profiles.
Conclusion: Rubber sealing joint molds are integral to the manufacturing of high-quality, precision-engineered sealing solutions used in diverse industrial applications. Through meticulous design, construction, and quality control processes, these molds enable the production of rubber seals and joints that exhibit exceptional dimensional accuracy, durability, and performance characteristics, ultimately contributing to the reliability and longevity of sealing systems in critical applications.
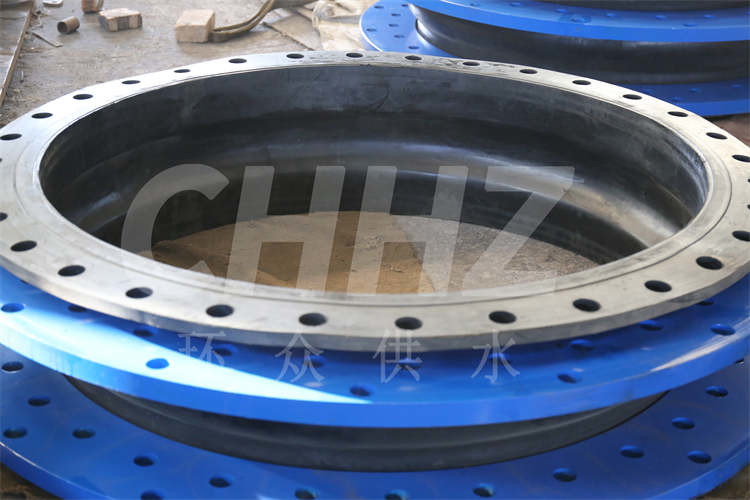