Formation of Rubber Cable Joint Molding
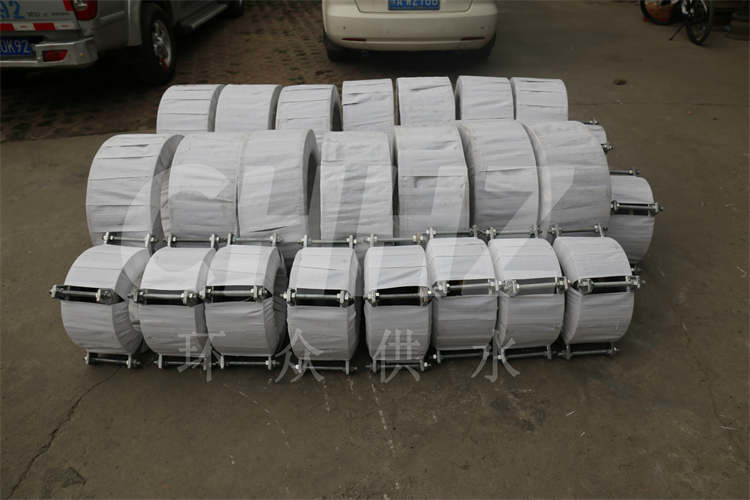
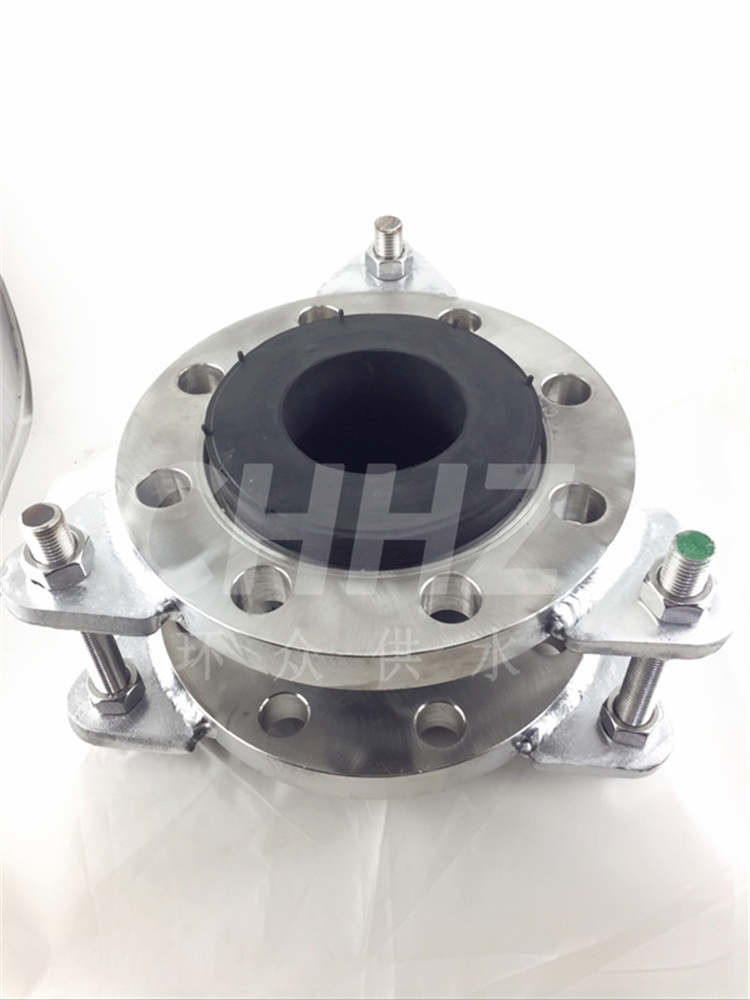
The formation of rubber cable joint molding is a critical process within the electrical industry, ensuring secure and reliable connections for various applications. This article discusses the key steps and considerations involved in the molding process, outlining best practices to achieve high-quality joint formations while maintaining electrical safety and reliability.
Preparation and Inspection: Before initiating the molding process, thoroughly inspect the cable ends to ensure they are clean, undamaged, and properly stripped of insulation. Any contaminants or irregularities may compromise the integrity of the joint formation. Additionally, ensure that the appropriate mold and accessories are in place and ready for use.
Selection of Molding Material: Select a high-quality, electrically insulating rubber or polymer material suitable for the specific environmental and operational conditions of the application. The molding material should exhibit excellent mechanical strength, thermal stability, and resistance to moisture, chemicals, and other environmental factors that the joint may encounter during service.
Application of Molding: Carefully position the prepared cable ends within the mold, ensuring the proper alignment and spacing to accommodate the molding material. Apply the chosen molding material to encapsulate and bond the cable ends, forming a seamless, solid connection that provides electrical insulation and mechanical protection. Adhere to the recommended curing time and temperature for the selected molding material to ensure optimal performance.
Compression and Curing: Utilize appropriate compression techniques, such as the application of pressure or use of compression molding equipment, to ensure uniform distribution of the molding material around the cable joint. Following the application of compression, initiate the curing process according to the material specifications, allowing the molding material to solidify and form a strong, durable connection.
Post-Molding Inspection: Upon completion of the curing process, conduct a thorough inspection of the molded joint to verify the absence of any voids, air pockets, or imperfections. Inspect the surface finish and structural integrity of the joint to ensure conformity to specifications and standards. Any deviations or deficiencies should be addressed to maintain the quality and reliability of the joint formation.
Electrical Testing and Quality Assurance: Perform electrical testing, such as insulation resistance measurements and dielectric strength tests, to validate the electrical integrity of the molded joint. Additionally, implement quality assurance procedures to confirm compliance with industry standards and ensure that the molded joint meets the required performance and safety criteria for the intended application.
By adhering to these best practices, the formation of rubber cable joint molding can be executed with precision, resulting in robust and durable connections that facilitate the safe and efficient operation of electrical systems. Attention to detail, material selection, and adherence to industry standards are crucial in achieving consistently high-quality joint formations for diverse electrical applications.
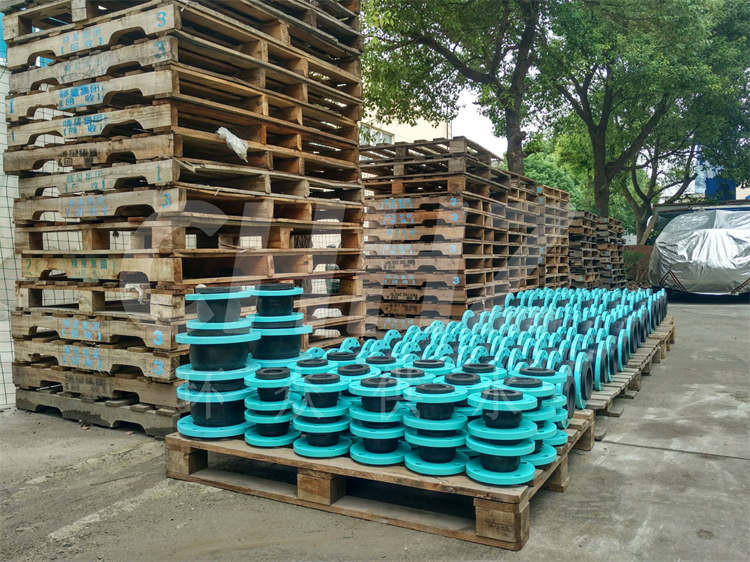