Rubber Flexible Joint in Mechanical Equipment: A Comprehensive Overview
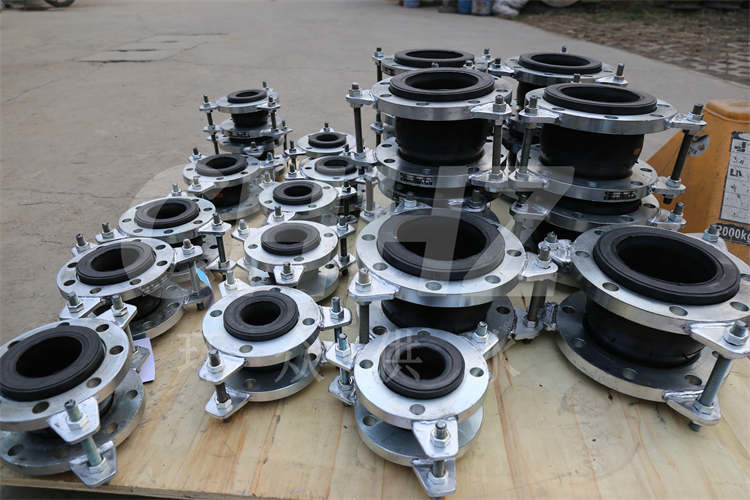
Rubber flexible joints, also known as rubber expansion joints, play a critical role in mechanical equipment by compensating for misalignments, reducing vibration, and absorbing movement. These essential components are utilized in a wide range of industries, including industrial, HVAC, marine, and automotive. In this article, we will provide a comprehensive overview of rubber flexible joints, their functions, installation, and significance in mechanical systems.
Introduction to Rubber Flexible Joints: Rubber flexible joints are designed to provide flexibility and movement in piping systems, allowing for axial, lateral, and angular movement. They consist of rubber elements, reinforced with metal components, that can absorb vibrations and mitigate stress caused by thermal expansion, contraction, or equipment movement. These joints are available in various configurations to suit specific system requirements, and their versatility makes them indispensable in the realm of mechanical equipment.
Functions and Benefits: The primary function of rubber flexible joints is to absorb and isolate vibrations, noise, and movement within piping systems. By doing so, they contribute to the longevity of the equipment and reduce the risk of damage to the connected components. Additionally, rubber flexible joints effectively compensate for thermal expansion and contraction, thereby extending the service life of the entire system. Their ability to accommodate misalignments and eliminate the transmission of noise and vibration makes them integral in maintaining the integrity of mechanical equipment.
Installation and Maintenance: The installation of rubber flexible joints demands careful consideration and adherence to best practices. It is imperative to select the appropriate joint size and type based on the operating conditions, temperature, pressure, and media being transported. Furthermore, the joint should be installed in a manner that allows for its full range of motion and flexibility without undue stress. Routine inspection and maintenance are crucial to ensure the continued performance of rubber flexible joints, as they may deteriorate over time due to exposure to environmental factors, chemicals, and mechanical stress.
Industry Applications: Rubber flexible joints find widespread application across multiple industries, including power generation, petrochemical, water treatment, and HVAC systems. In power generation facilities, these joints are used to compensate for thermal expansion and contraction in piping systems, while in the petrochemical industry, they provide flexibility in handling various chemicals and abrasive materials. Additionally, rubber flexible joints are incorporated in marine applications to absorb movement and vibration in piping systems aboard ships and offshore structures.
Significance in Mechanical Systems: The significance of rubber flexible joints in mechanical systems cannot be overstated. They serve as crucial components that maintain the integrity and functionality of piping networks, ensuring the safe and efficient operation of mechanical equipment. By mitigating stress, absorbing movement, and reducing vibration, rubber flexible joints contribute to the reliability, longevity, and safety of the entire system.
In conclusion, rubber flexible joints are indispensable components in mechanical equipment, providing flexibility, vibration isolation, and movement absorption in piping systems. Their vital role in various industries underscores their significance, making them essential for the smooth and reliable operation of mechanical systems.
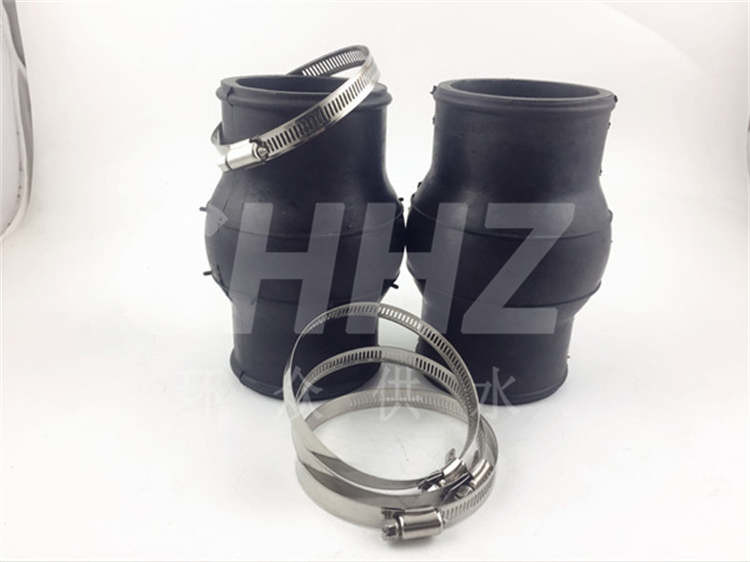