Methods of Connecting Rubber Cables:
The connection and termination of rubber cables play a crucial role in ensuring the efficiency, reliability, and safety of electrical systems across various industrial and commercial applications. Properly connecting rubber cables is essential to maintain electrical integrity and prevent potential hazards. Several methods are utilized for joining and terminating rubber cables, each tailored to specific requirements and environmental conditions.
One of the primary methods for connecting rubber cables is through the use of crimping techniques. Crimping involves mechanically securing a terminal or connector onto the conductor of the rubber cable, creating a permanent and reliable electrical connection. This method is widely employed due to its simplicity, cost-effectiveness, and ability to accommodate a broad range of cable sizes and conductor materials. The crimped connection ensures excellent electrical conductivity while also providing mechanical strength and strain relief, making it suitable for both indoor and outdoor applications.
Another prevalent method for connecting rubber cables is through the use of soldering. Soldering involves heating a metal alloy to create a liquid bond, which is then used to join the conductors of the cable to the terminals or connectors. Soldering is known for its ability to produce a strong, low-resistance connection, making it suitable for applications where high electrical performance is critical. Additionally, soldered connections offer excellent protection against corrosion and oxidation, enhancing the longevity of the electrical joint.
In cases where flexibility and reusability are paramount, the utilization of twist-on wire connectors presents an effective method for connecting rubber cables. Twist-on connectors, also known as wire nuts, provide a convenient means of joining conductors by twisting them together and encapsulating the connection within an insulated housing. This method is particularly advantageous in situations that require frequent modifications or temporary connections, such as during equipment maintenance or troubleshooting.
Furthermore, the method of compression connectors offers a reliable approach to terminating rubber cables, especially in high-voltage applications. Compression connectors are designed to create a robust, gas-tight seal between the cable conductor and the terminal, ensuring optimal electrical performance and minimizing the risk of oxidation or moisture ingress. This method is commonly employed in power distribution and industrial settings where secure and enduring cable terminations are essential for system integrity and safety.
Lastly, the utilization of insulation displacement connectors (IDCs) provides an efficient and cost-effective approach for connecting rubber cables in certain applications. IDCs are designed to create electrical connections by displacing the cable's insulation, thereby establishing direct contact with the conductor. This method is particularly advantageous for mass terminations and rapid installations, contributing to time and labor savings in large-scale projects.
In conclusion, the selection of the appropriate method for connecting rubber cables is contingent upon various factors, including the application environment, the desired electrical performance, and installation requirements. Whether through crimping, soldering, twist-on connectors, compression connectors, or IDCs, each method offers distinct advantages and considerations to ensure the reliable and safe operation of electrical systems utilizing rubber cables. The proper selection and execution of cable connection methods are imperative for upholding electrical integrity and minimizing potential risks associated with cable terminations.
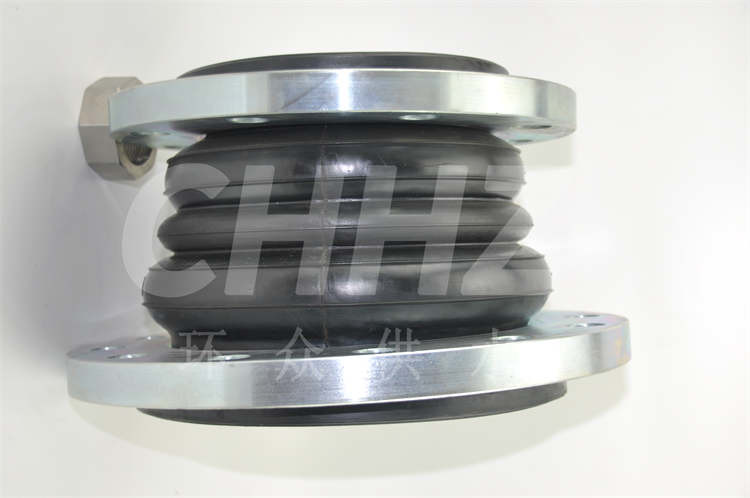