Rubber cable
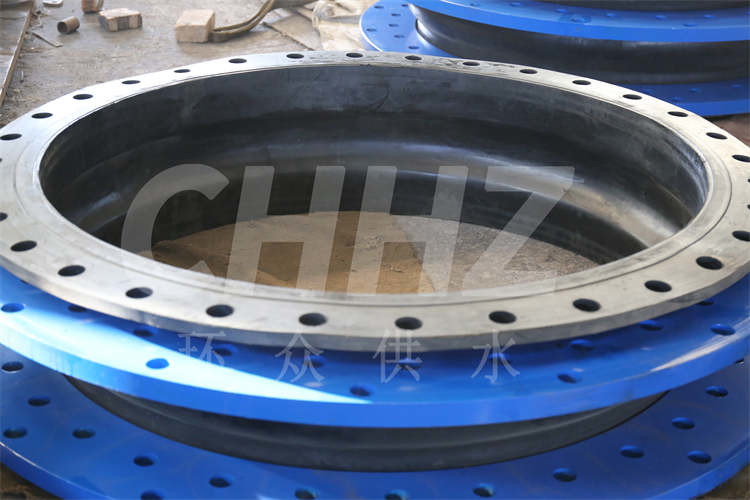
Rubber cable is widely used in various industries due to its flexibility and durability. When it comes to joining the bends of rubber cables, it is crucial to ensure a proper and secure connection to maintain the integrity of the electrical system.
The process of joining the bends of rubber cables, commonly referred to as splicing, involves several steps. The first step is to carefully strip the insulation from the ends of the cables to expose the conductors. This is usually done using a specialized cable stripper or a sharp knife, taking care not to damage the conductors inside.
Once the conductors are exposed, the next step is to twist and solder them together. This creates a solid electrical connection between the two cables. Soldering is a process that involves using a soldering iron and solder to join the conductors. The solder creates a bond between the conductors, ensuring a reliable electrical connection.
After the conductors are soldered together, it is essential to insulate the connection to prevent any electrical faults or short circuits. This is commonly done using electrical tape or heat-shrink tubing. The insulation material should be applied carefully to completely cover the exposed conductors and provide protection against moisture and other environmental factors.
Finally, it is advisable to perform a continuity test to ensure that the spliced connection is conductive and free from any defects. This can be done using a multimeter or a continuity tester to check for the presence of a continuous electrical path between the two cables.
In summary, joining the bends of rubber cables involves stripping the insulation, soldering the conductors, insulating the connection, and performing a continuity test. Properly executed, this process ensures a secure and reliable connection, maintaining the safety and efficiency of the electrical system.
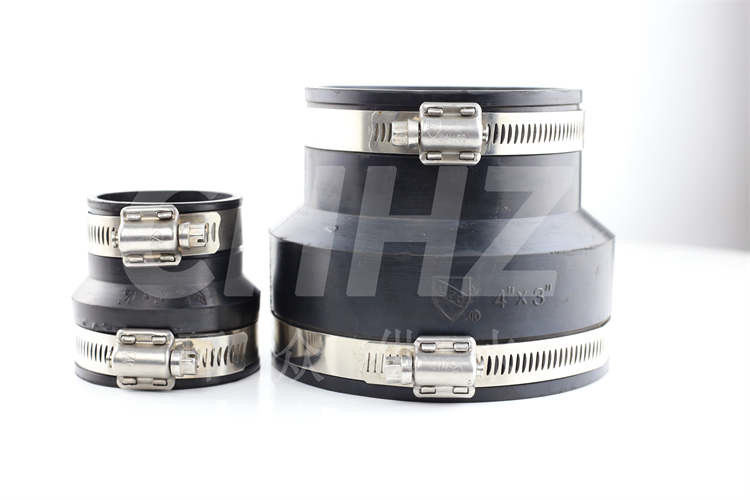